
Che cosa sono gli NDAs?
NDA: il valore degli accordi di riservatezza alla base di un rapporto di fiducia fra service e aziende manifatturiere
Gli Accordi di Riservatezza, comunemente identificati come NDA (Non-Disclosure Agreements), costituiscono un elemento giuridico di fondamentale importanza nel contesto dell’industria manifatturiera, essendo finalizzati alla tutela delle informazioni di natura confidenziale e riservata.
I contratti NDA godono di un’applicazione diffusa sia nell’ambito industriale che tecnologico, nonché nel campo della ricerca e sviluppo, con l’esplicito obiettivo di impedire la divulgazione di dati sensibili a parti terze, salvo previo consenso esplicito da parte del titolare di tali informazioni.
La gestione dei segreti industriali in Prosilas
Prosilas opera a stretto contatto con le aziende, contribuendo alla realizzazione di progetti destinati a debuttare sul mercato entro i prossimi tre anni.
In questo contesto, la salvaguardia delle informazioni assume un ruolo critico. Pertanto forniamo supporto sia per la produzione di componenti in fase prototipale che per la produzione in serie, avvalendoci di un ventaglio completo di tecnologie, che spaziano dalle complesse metodologie di manifattura additiva e stampa 3D alle più tradizionali tecniche di stampaggio ad iniezione.

All’interno del gruppo Prototal Industries vantiamo un accesso privilegiato a risorse tecnologiche eterogenee, occasionalmente facendo ricorso a collaborazioni con fornitori esterni. Proprio per questo motivo è fondamentale estendere la riservatezza a tutta la catena di produzione quando si scambiano informazioni con colleghi e partner.
Cybersecurity: protezione delle informazioni online
La comunicazione di informazioni si effettua attraverso piattaforme digitali o mediante la trasmissione di file per posta elettronica, accentuando la rilevanza delle questioni relative alla sicurezza informatica.
In tal senso, Prosilas investe costantemente per potenziare i propri sistemi di sicurezza informatica, garantendo un adeguato monitoraggio e protezione delle informazioni scambiate.
Il nostro personale, a sua volta, riceve formazione specialistica continua, al fine di mantenere elevate competenze in materia.
Spazi dedicati: protezione dei progetti “off-line”
La riservatezza costituisce un pilastro fondamentale della nostra operatività, ed è assicurata attraverso l’impiego degli NDA. Nonostante ciò, vi sono circostanze in cui un grado di segretezza superiore è richiesto.
Abbiamo dedicato appositi spazi all’interno dei nostri laboratori, garantendo l’accesso esclusivamente al personale autorizzato.
La sicurezza delle informazioni rappresenta una priorità indiscutibile, in modo da preservare la fiducia e il rispetto dei nostri clienti.
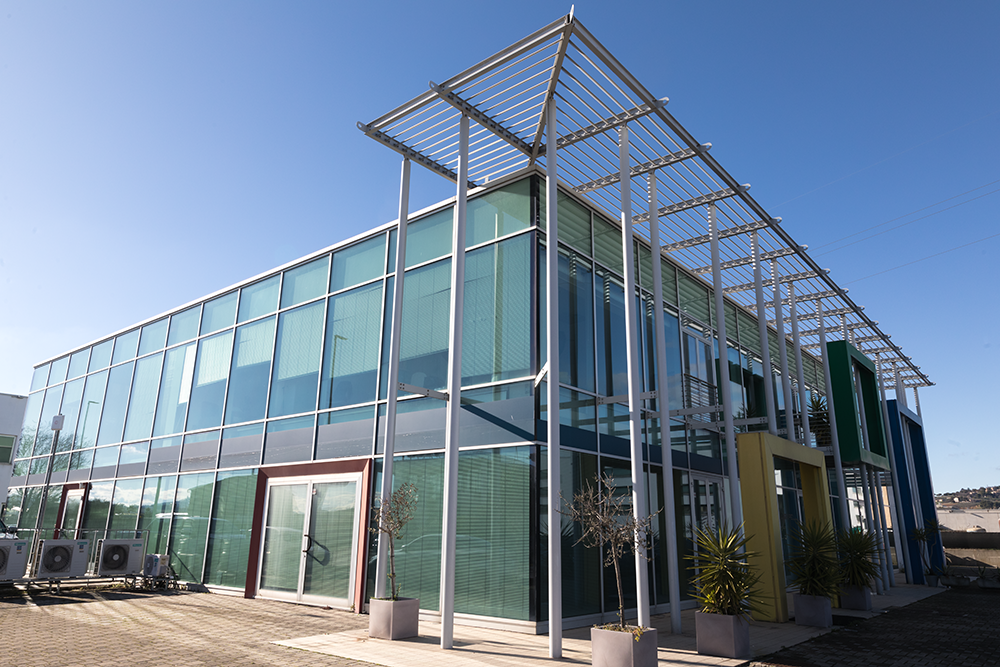