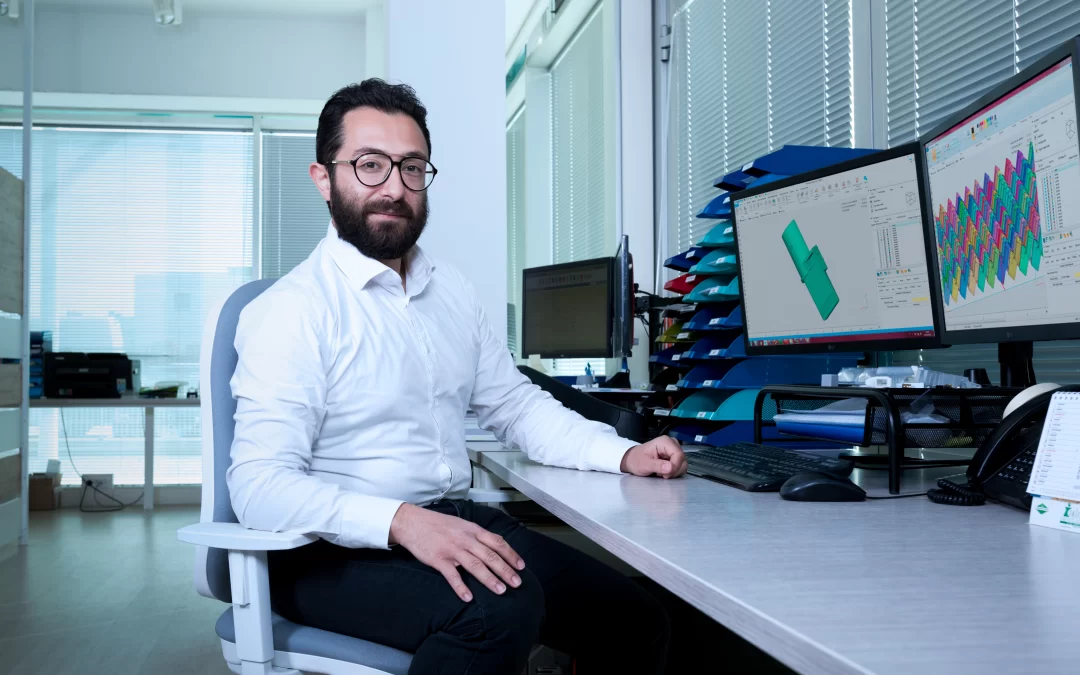
File STL : gli errori più comuni
Parliamo di normali invertite, presenza di fori e shell multiple
Alcuni degli errori più comuni che possiamo riscontrare in un file STL riguardano solitamente l’inversione delle normali, la presenza di fori o di shell multiple.
Questi derivano spesso da errori commessi durante la modellazione oppure in fase di esportazione, dove il file viene trasformato in STL tramite un software CAD.
Per poter procedere con la produzione additiva utilizzando le stampanti 3D, i difetti devono prima essere revisionati e corretti.
Facciamo prima un passo indietro, ricordando che il file STL, necessario per la stampa 3D, rappresenta una geometria tridimensionale composta da triangoli orientati nello spazio.
Puoi approfondire le caratteristiche dei file STL nell’ articolo precedente.
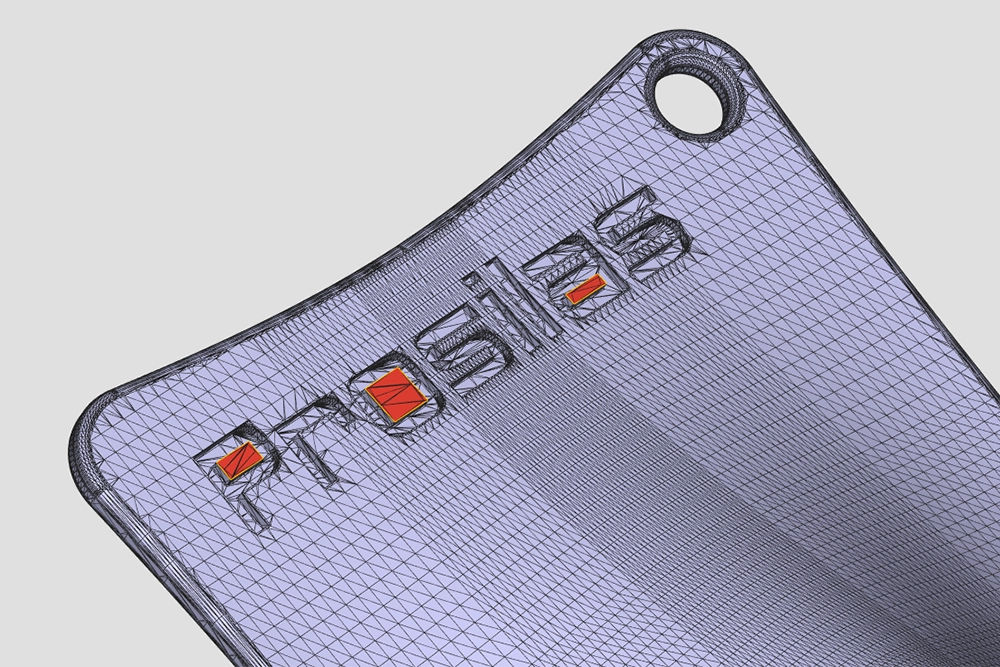
Normale invertita
Ogni triangolo è descritto non solo dalle coordinate dei vertici, ma anche dalla normale, ovvero un vettore perpendicolare al piano su cui è posizionato il triangolo, il cui orientamento definisce il lato esterno. In alcuni casi, la normale di questi triangoli può essere invertita, identificando erroneamente un lato esterno come interno e viceversa. Tale situazione causa errori durante la fase di stampa.
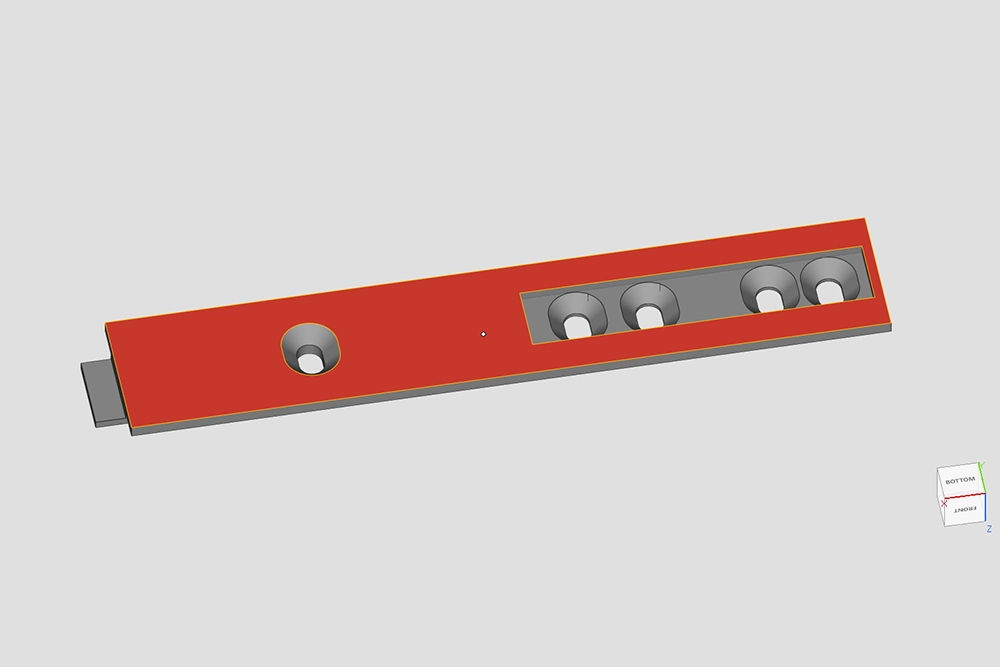
Normale invertita in un file SLT
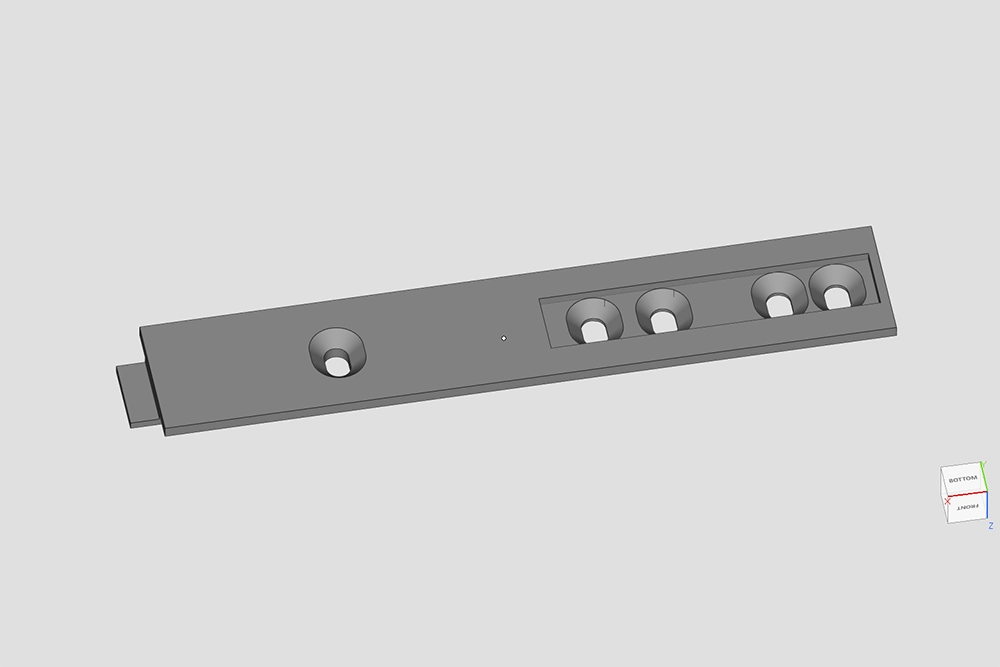
Normale corretta in un file STL
Fori nel file STL
Il secondo errore più comune è la presenza di fori, che può essere causata da superfici mancanti o da uno scostamento tra i vertici dei triangoli. Tali fori devono essere corretti manualmente se di dimensioni considerevoli, o automaticamente mediante l’utilizzo di appositi software se di dimensioni minori.
La presenza di fori può compromettere la qualità e la realizzazione della stampa della parte.
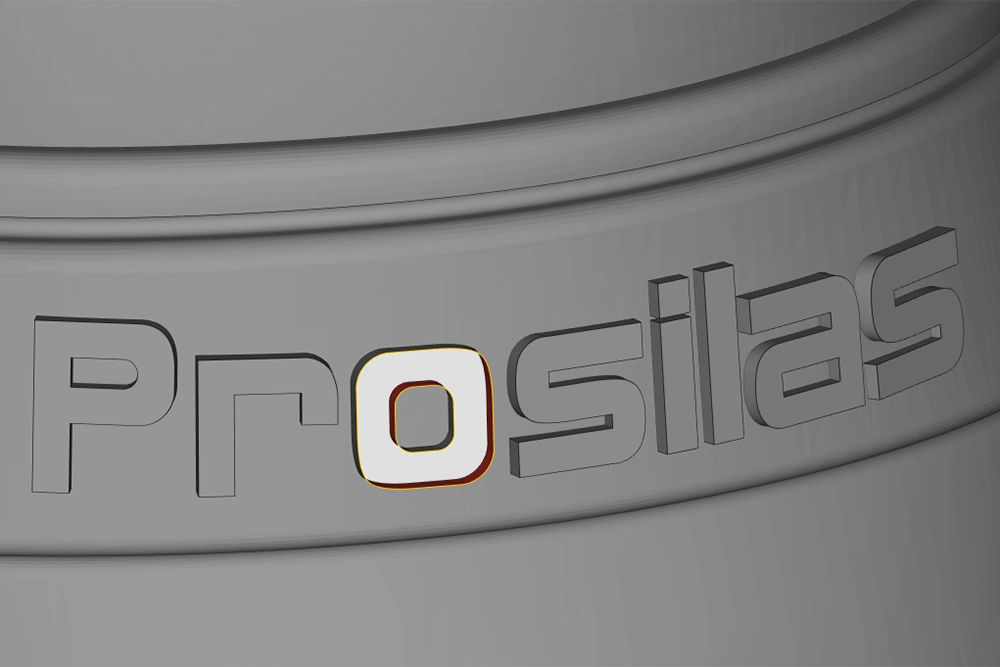
Fori in un file STL
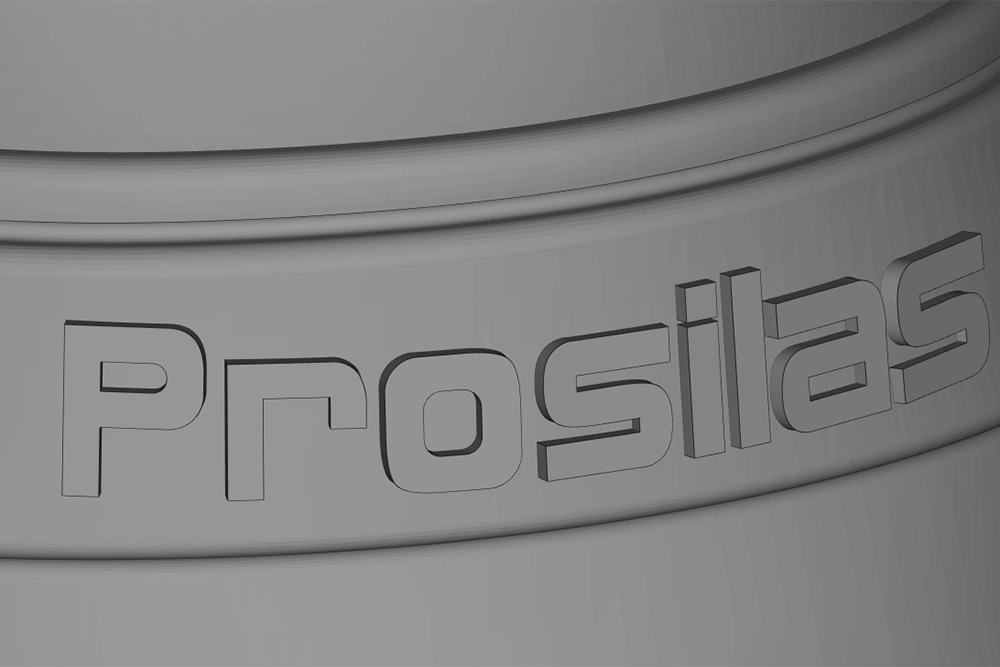
Correzione dei fori nel file STL
Shell Multiple
Infine, incontriamo il problema delle shell multiple. Per shell si intende un gruppo di triangoli connessi tra loro.
La presenza di più shell in una parte indica la presenza di gruppi di triangoli separati. In questo caso, la shell della figura interna si sovrappone alla shell della figura esterna. La risoluzione di questo tipo di errori è necessaria per evitare anomalie durante la suddivisione del modello in strati o superfici errate (slicing), nonché per evitare che la stampante si blocchi.
È importante che tutte le shell siano correttamente unite per ottenere una parte stampata coerente e funzionale.
Tale situazione può verificarsi anche quando, nella fase di progettazione, le forme che compongono il modello CAD non vengono unite al resto della shell, ma rimangono separate.
È fondamentale assicurarsi che tutte le componenti del modello siano correttamente integrate nella shell principale per evitare problemi.
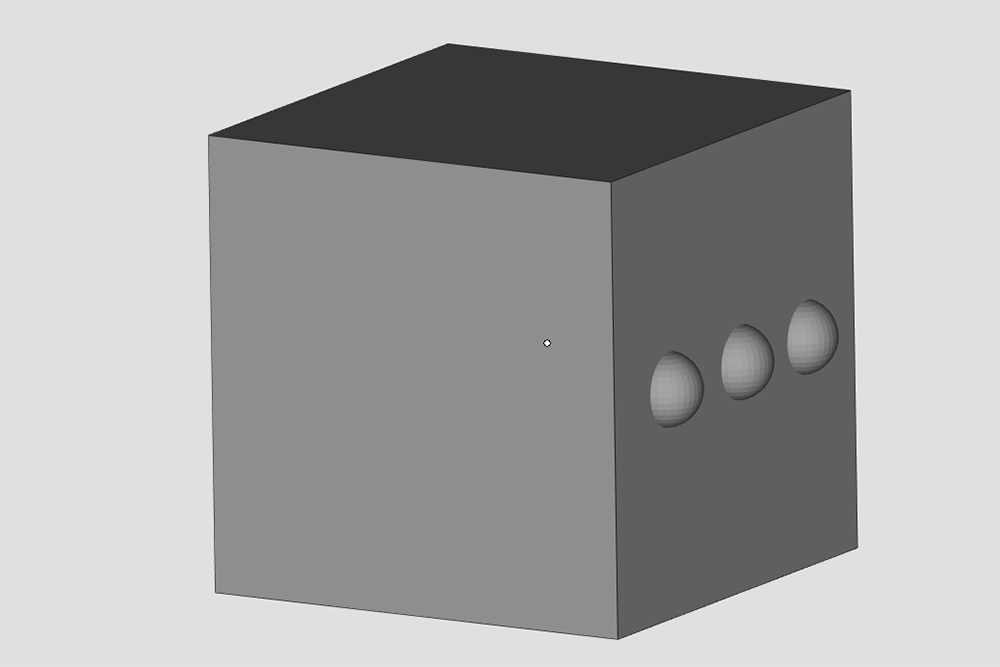
Esempio di Shell Multiple in un file STL
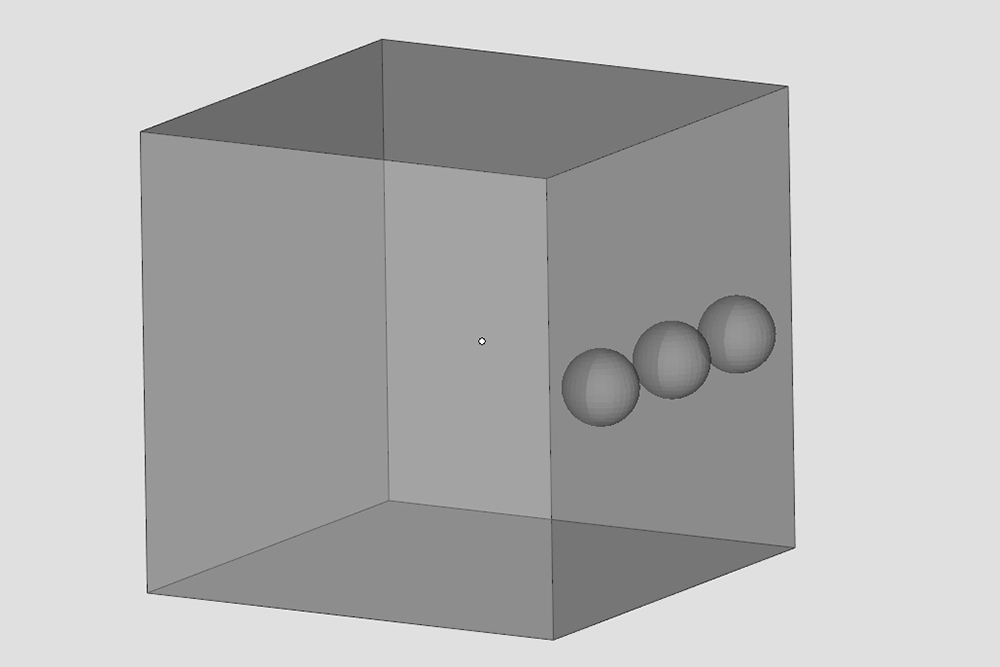
Esempio di Shell Multiple in un file STL
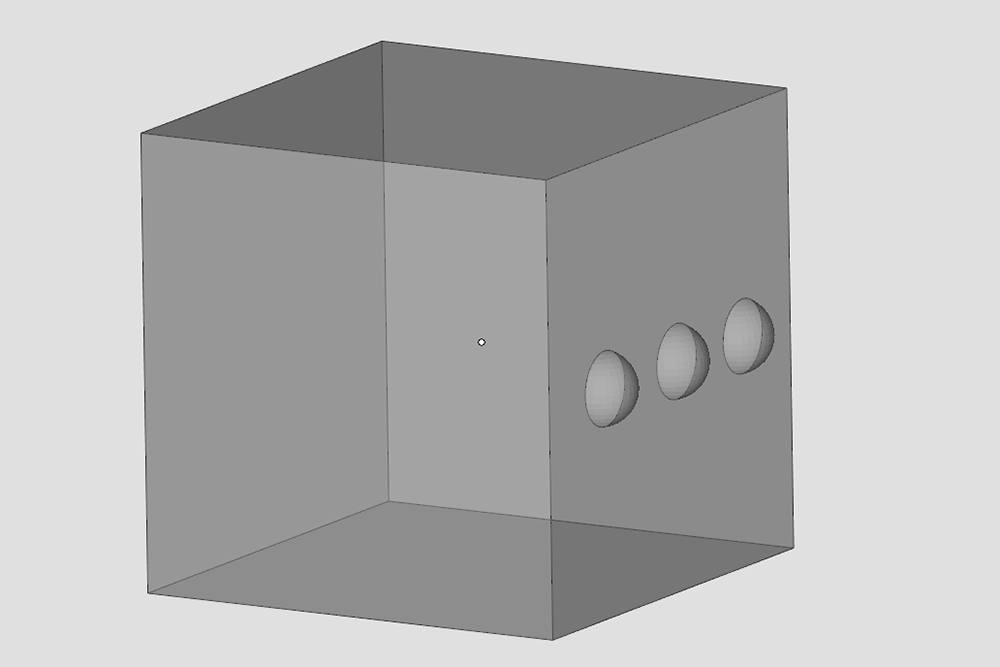
Esempio di risoluzione di Shell Multiple in un file STL
Quando riceviamo i file STL si verifica frequentemente la necessità di apportare modifiche e correzioni prima di procedere con la messa in macchina.
La correzione dei file STL richiede competenze specifiche e l’utilizzo di software dedicati che consentano di riparare le imperfezioni e garantire che la parte sia pronta per essere sottoposta alla stampa.
Il nostro team si impegna appieno nell’effettuare tali correzioni con la massima precisione e tempestività, al fine di garantire che le parti stampate raggiungano elevati standard qualitativi e soddisfino appieno le aspettative dei clienti.