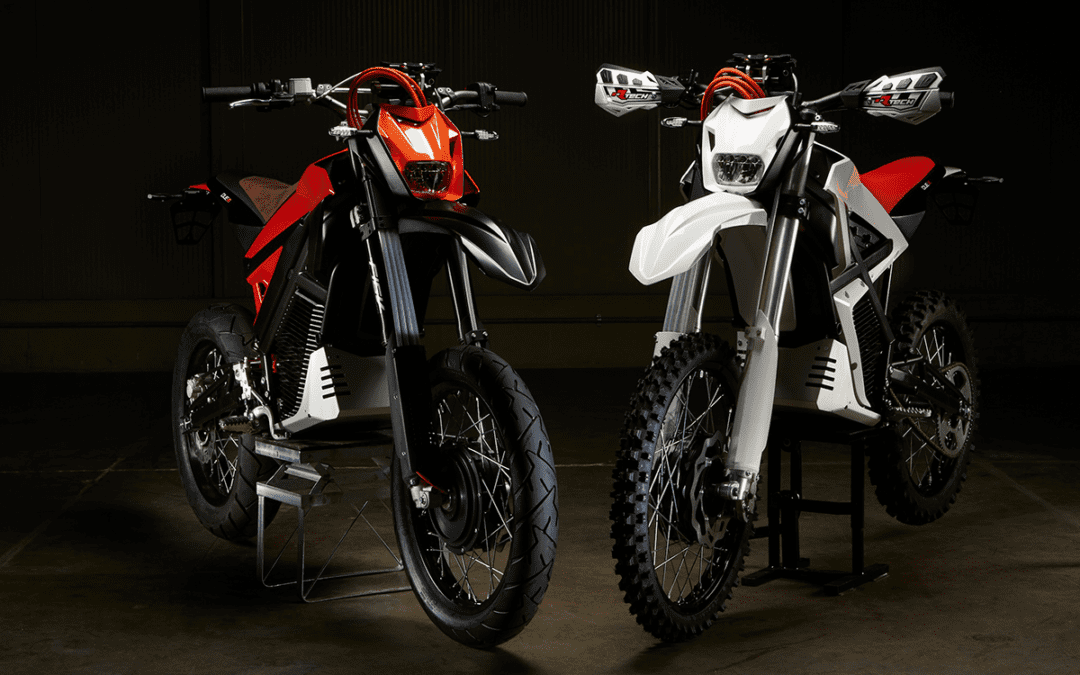
Progetto Armotia – Caso Studio
Armotia + Prosilas Case History
Prototipi di moto elettriche: il contributo della stampa 3d.
Prosilas ha svolto un ruolo chiave nella realizzazione del progetto di Armotia, una ditta con sede ad Osimo che si è dedicata alla progettazione e produzione di moto elettriche da cross ed enduro. Grazie alla collaborazione tra queste due aziende, è stato possibile creare prototipi innovativi e di alta qualità, che rappresentano una vera e propria rivoluzione nel mondo del motociclismo.
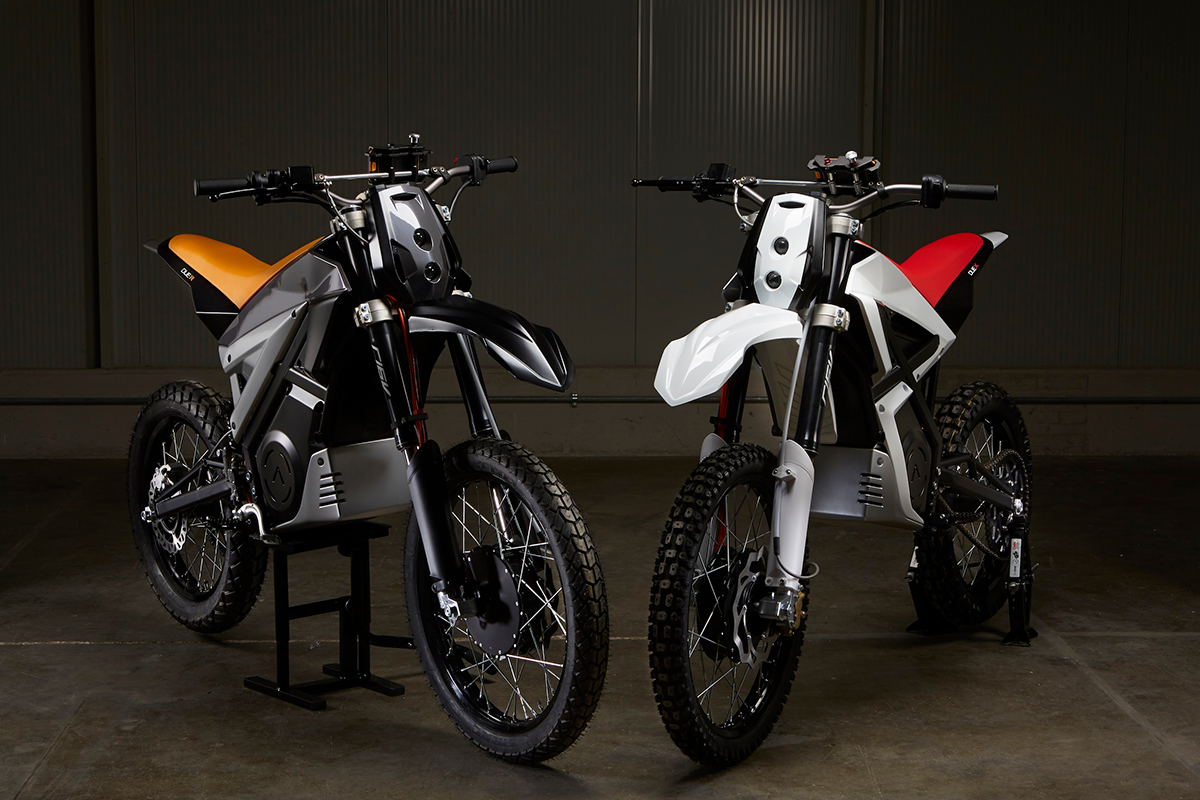
Armotia: il progetto
ARMOTIA presenta DUE X e DUE R, le prime due moto di serie elettriche con due ruote motrici a ripartizione elettronica della coppia.
Le nostre moto hanno caratteristiche di motricità eccezionali, che ti regaleranno sensazioni di guida incredibili per vivere ogni tipo di tracciato, on e off road, come non è mai stato possibile.
Le ARMOTIA, oltre a tutto questo, offrono di serie features e possibilità davvero intelligenti. Come lo smartphone integrato per fare video, controllare le prestazioni, salvare i dati della telemetria e condividere ogni tuo percorso. O come la possibilità di personalizzare le parti più accattivanti delle carene con la stampante 3D, per rendere ancora più “special” le moto più special che hai mai visto. Perché se è vero che due ruote muovono l’anima, con ARMOTIA scoprirai che due ruote motrici lo fanno decisamente meglio.
Dal sito di Armotia
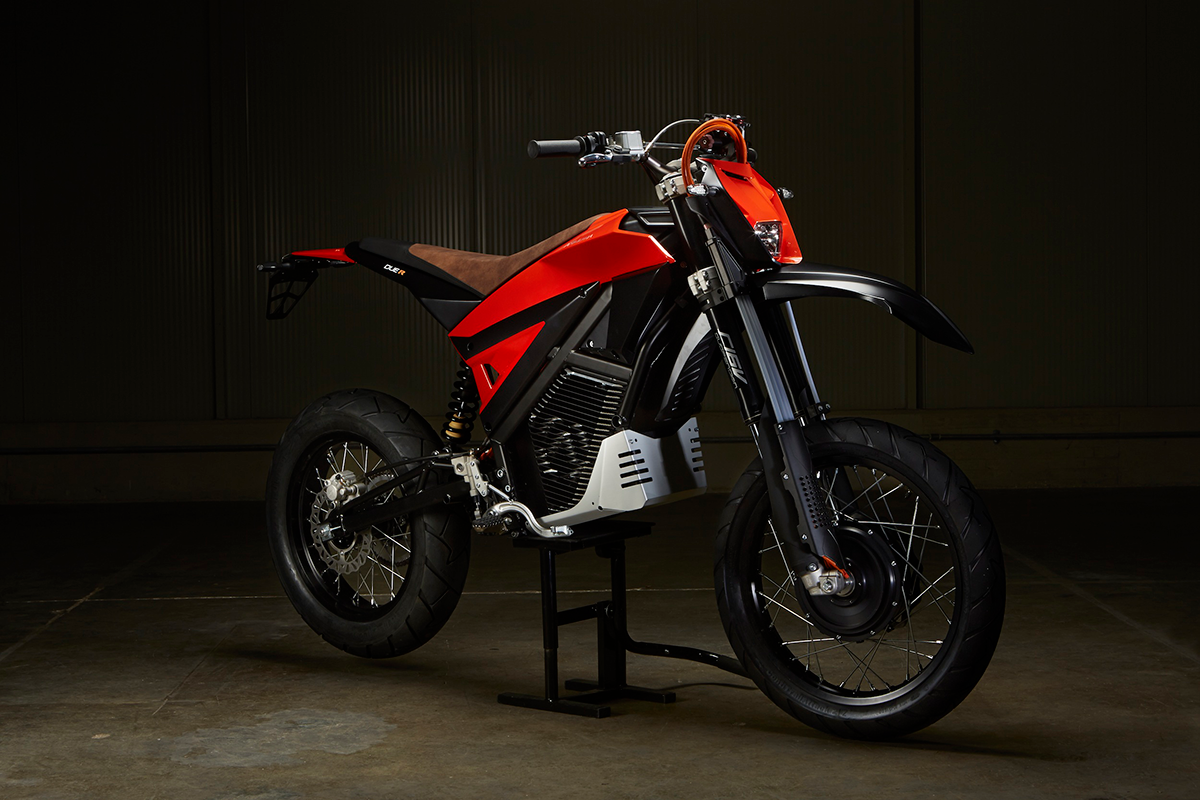
Il contributo di Prosilas
Armotia ha puntato sulla tecnologia della stampa 3D per la produzione di parti e componenti per la realizzazione dei prototipi delle moto DUE R e DUE X. In questo contesto, Prosilas ha fornito un supporto prezioso grazie alla sua competenza in fatto di materiali e finiture per gli oggetti 3D.
Grazie alla consulenza fornita da Prosilas, Armotia ha potuto scegliere i materiali più adatti per la realizzazione dei suoi prototipi, garantendo un elevato livello di resistenza e finitura superficiale: PA12 ALU e poliammide caricata vetro (PA12 GF) per carene e scocche.
il PA12 caricato alluminio è un materiale molto resistente e che presenta una buona finitura superficiale, rendendolo ideale per la realizzazione di parti che richiedono una finitura di alta qualità. Inoltre, questo materiale può essere facilmente verniciato, permettendo di personalizzare ulteriormente i prototipi realizzati.
La poliammide caricata vetro, invece, è un materiale altamente resistente, che si presta perfettamente alla produzione di parti che richiedono una maggiore robustezza e anche a trattamenti CNC.
Grazie alla consulenza di Prosilas, Armotia ha potuto scegliere il materiale più adatto per ogni specifica applicazione.
Questa sinergia dimostra come la stampa 3D e la consulenza di aziende specializzate come Prosilas possano fare la differenza nella realizzazione di progetti innovativi e di alta qualità.
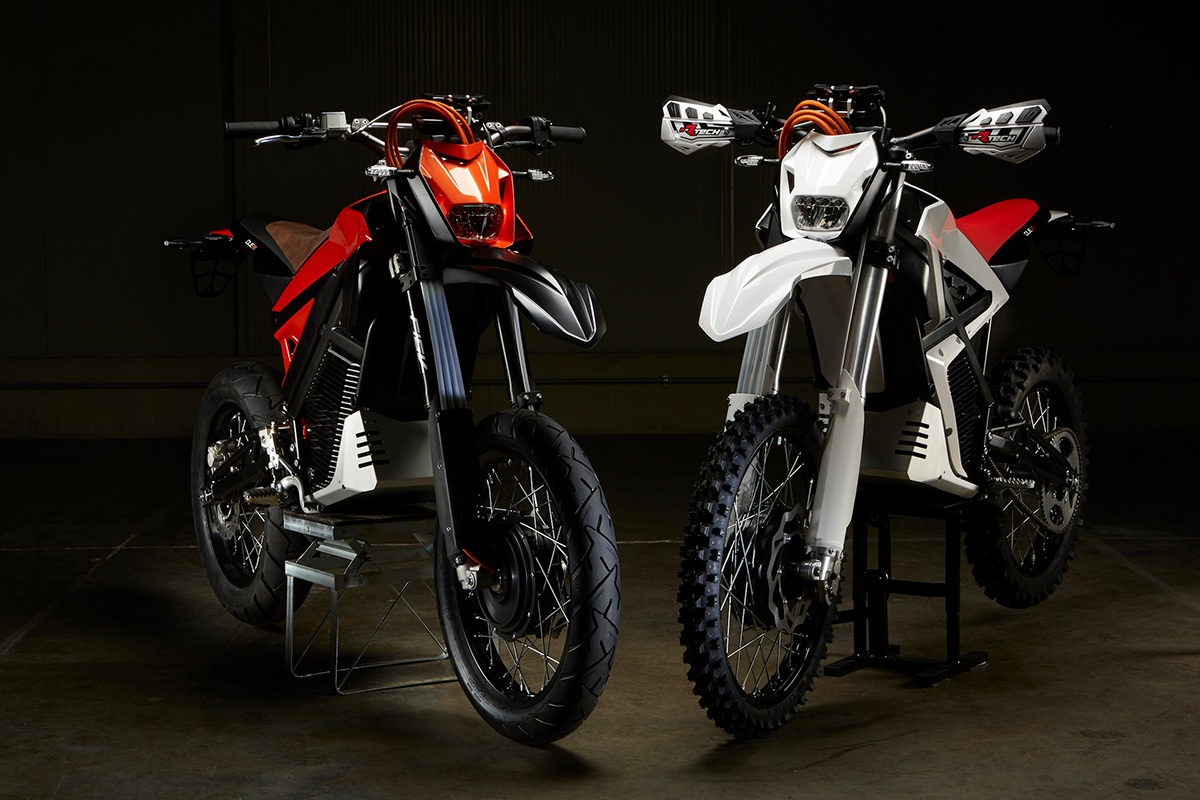
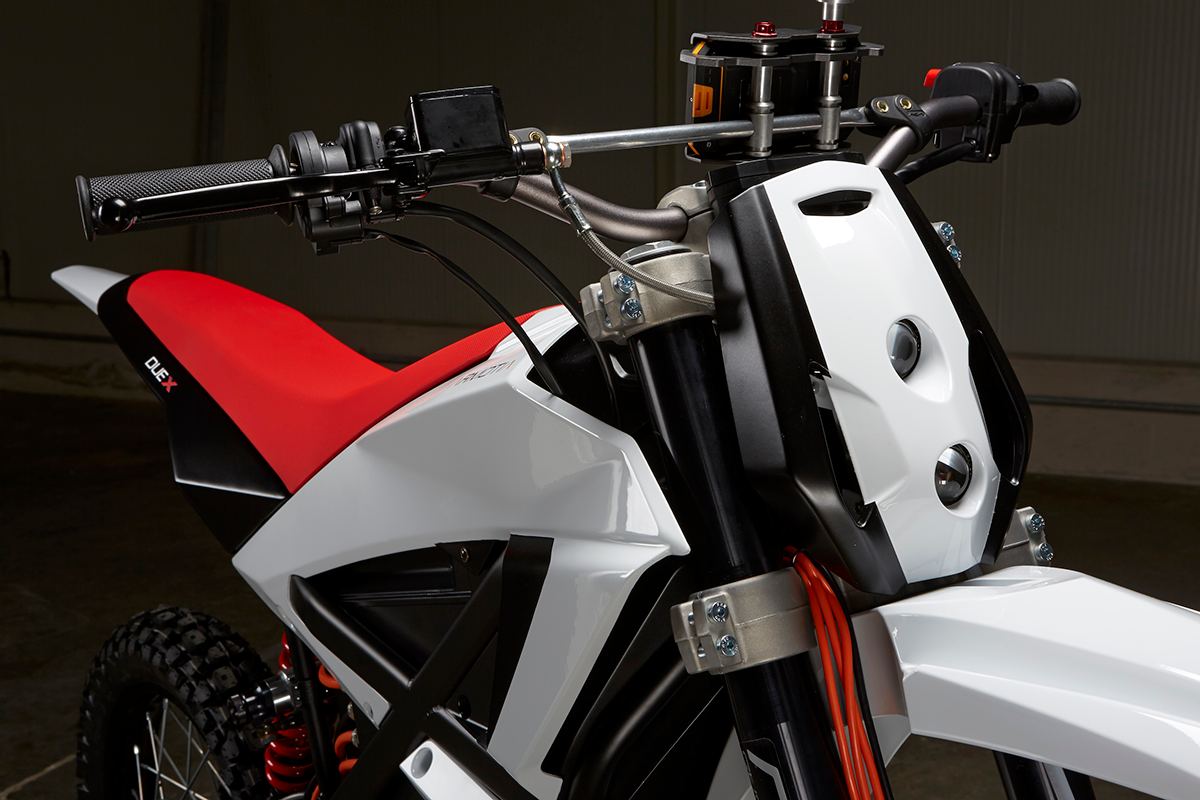
I trattamenti di post-processo: la verinicatura
Oltre alla consulenza sulla scelta ottimale dei materiali, offriamo consulenza su quale trattamento di post-process sia il più adatto per ottenere il miglior risultato possibile.
Il servizio post processo di verniciatura consente di ottenere parti in diverse colorazioni personalizzabili con una finitura superficiale simile a quella delle parti prodotte con lo stampaggio ad iniezione. Il nostro reparto finitura è in grado di ripodurre tutta la gamma di colori RAL e colorazioni speciali in base alle richieste del cliente.
La veniciatura, aspetto importante da considerare nella produzione di parti in 3d, conferisce un valore aggiunto in quanto consente di avere un prototipo esteticamente accattivante e vicinissimo al prodotto finale.
Grazie a tecnologie e materiali avanzati, i prototipi e le serie prodotte in Prosilas, potranno inoltre avere finiture opache, lucide e metallizzate o resitente ai raggiu UV o agli idrocarburi.
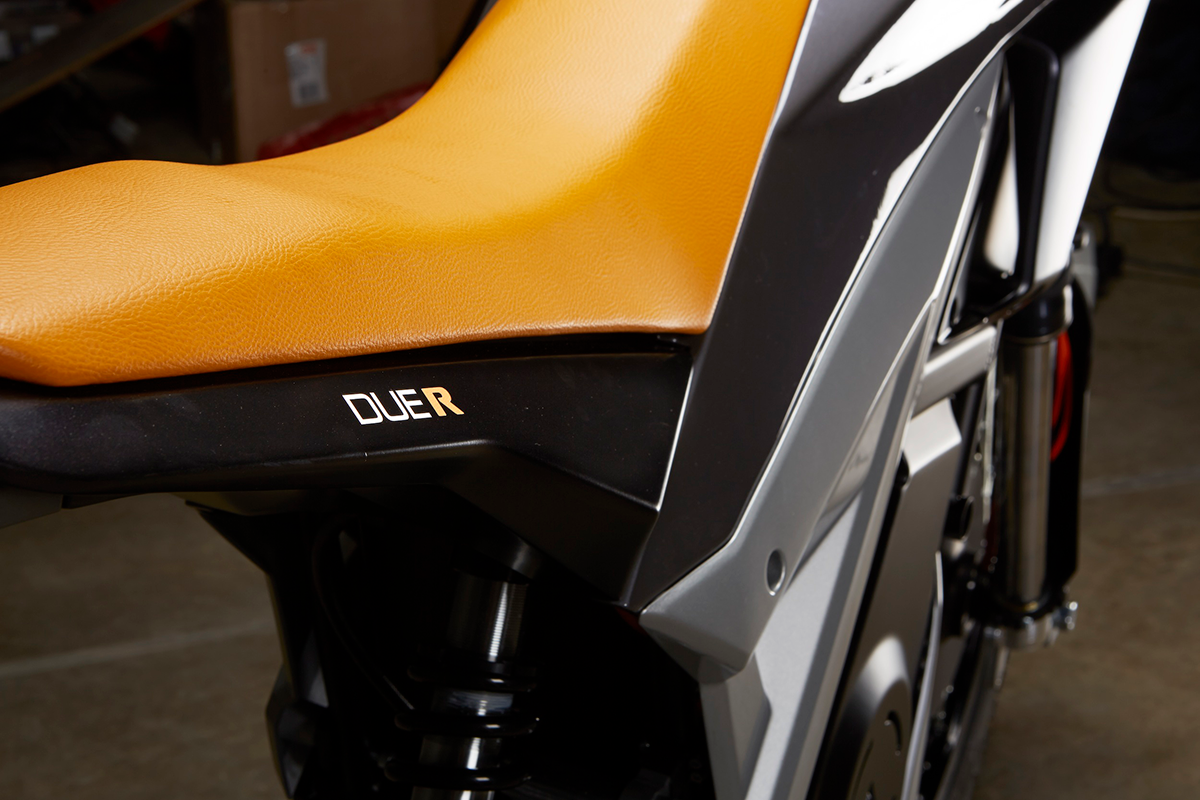