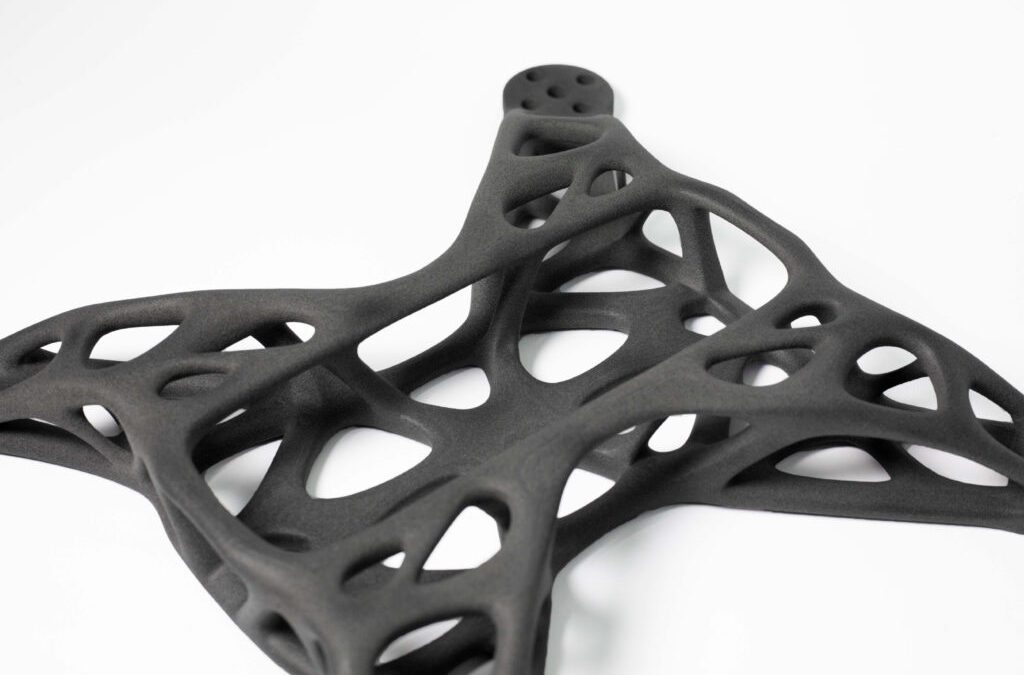
Ottimizzazione topologica nella stampa 3D
Caso studio: Ottimizzazione topologica e stampa 3D per un telaio di drone leggero e resistente
Droni sempre più performanti e leggeri richiedono componenti all’avanguardia.
Prosilas presenta un caso studio che illustra l’utilizzo dell’ottimizzazione topologica e della stampa 3D SLS per la produzione di un telaio per drone in poliammide caricata con fibra di carbonio.
Le sfide:
- Ridurre il peso del telaio per migliorare l’efficienza e l’autonomia del drone.
- Garantire la resistenza del telaio alle sollecitazioni e vibrazioni durante il volo.
- Creare una geometria complessa e ottimizzata non realizzabile con metodi di produzione tradizionali.
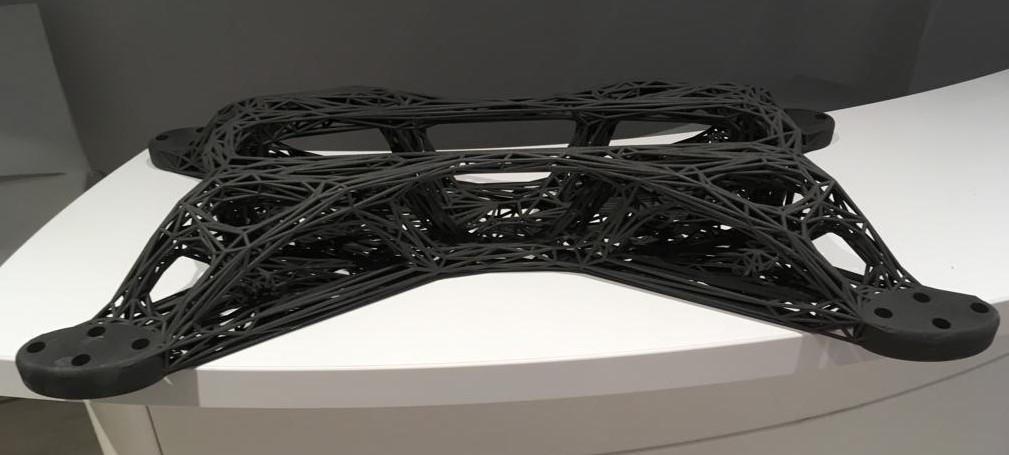
Progettazione e ottimizzazione
Il telaio del drone è stato progettato utilizzando un software di ottimizzazione topologica. Questo software ha analizzato le sollecitazioni e i vincoli a cui il telaio sarebbe stato sottoposto durante il volo e ha generato una geometria ottimale che utilizza solo la quantità di materiale necessaria per soddisfare i requisiti di resistenza.
Produzione
Il telaio è stato prodotto utilizzando la tecnologia di stampa 3D SLS (Selective Laser Sintering) con poliammide caricata con fibra di carbonio.
Questo materiale è stato scelto per la sua elevata resistenza meccanica, la sua leggerezza e la sua resistenza alle alte temperature.
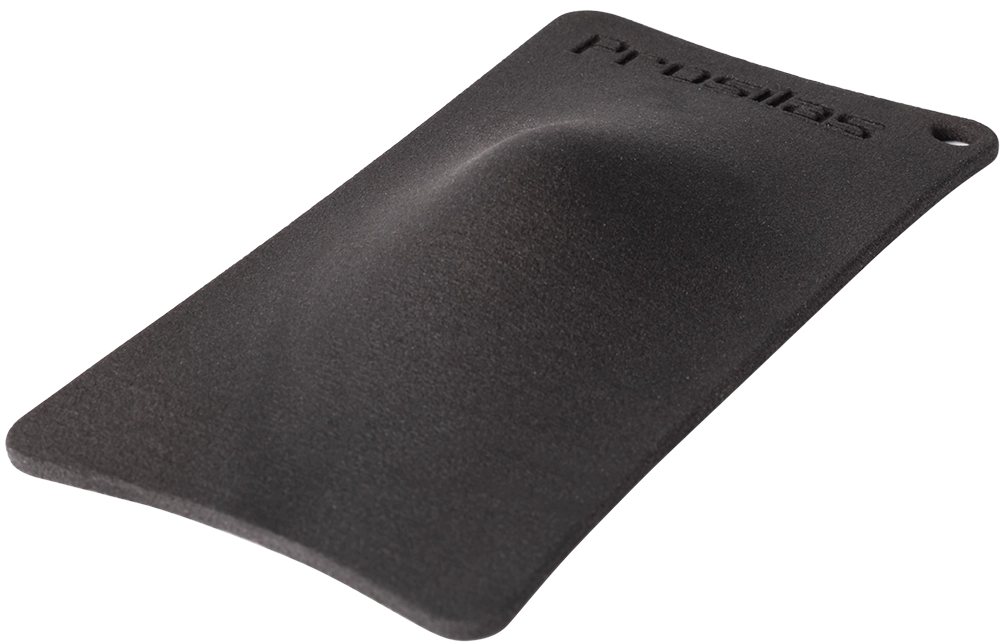
Risultati
Il telaio del drone prodotto con poliammide caricata con fibra di carbonio è risultato essere il 50% più leggero rispetto a un telaio realizzato con un materiale tradizionale, come l’alluminio.
Inoltre, il telaio in questo materiale ha dimostrato una resistenza meccanica superiore e una migliore capacità di assorbire le vibrazioni.
Benefici
L’utilizzo dell’ottimizzazione topologica e della stampa 3D SLS ha portato a una serie di benefici per il telaio del drone:
- Riduzione del peso: Il telaio è il 50% più leggero rispetto a un telaio in alluminio, migliorando l’efficienza e l’autonomia del drone.
- Maggiore resistenza: Il telaio in poliammide caricata con fibra di carbonio ha una resistenza meccanica superiore e una migliore capacità di assorbire le vibrazioni, aumentando la durata e l’affidabilità del drone.
- Libertà di design: L’utilizzo della stampa 3D ha permesso di creare una geometria complessa e ottimizzata che non sarebbe possibile realizzare con i metodi di produzione tradizionali.
- Riduzione dei costi: La stampa 3D ha permesso di ridurre i costi di produzione del telaio, rendendolo più accessibile per un’ampia gamma di applicazioni.
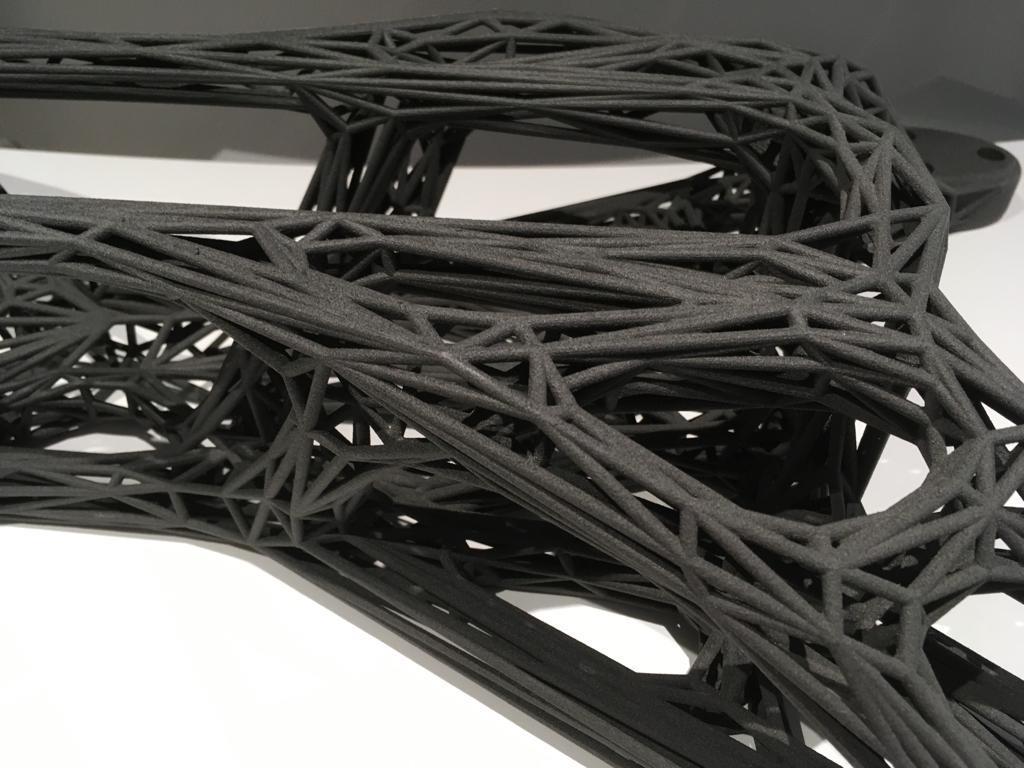
Hyper-Light Carbon: 20% in meno del peso
Oltre alla poliammide caricata con fibra di carbonio, Prosilas offre Hyper-Light Carbon, uno dei più leggeri nel mondo della stampa 3D.
La nuova formulazione di PA 12 con fibra di carbonio conferisce leggerezza, resistenza e facilità nella lavorazione, il materiale ha una finitura superficiale uniforme, un’alta precisione e un ottimo rapporto resistenza-peso.
Rappresenta un’ulteriore evoluzione per la produzione di telai di droni e componenti in cui la leggerezza è una caratteristica fondamentale.
Hyper-Light Carbon si distingue per la sua densità ancora più bassa (0,82 g/cm³), che consente di realizzare telai ancora più leggeri e performanti. Questo materiale offre anche un’elevata resistenza meccanica, un’ottima finitura superficiale e una facilità di lavorazione.
Con Hyper-Light Carbon si può:
- Raggiungere un nuovo livello di leggerezza e prestazioni.
- Migliorare ulteriormente l’efficienza e l’autonomia del drone.
- Ottenere geometrie complesse e ottimizzate per una migliore aerodinamica.
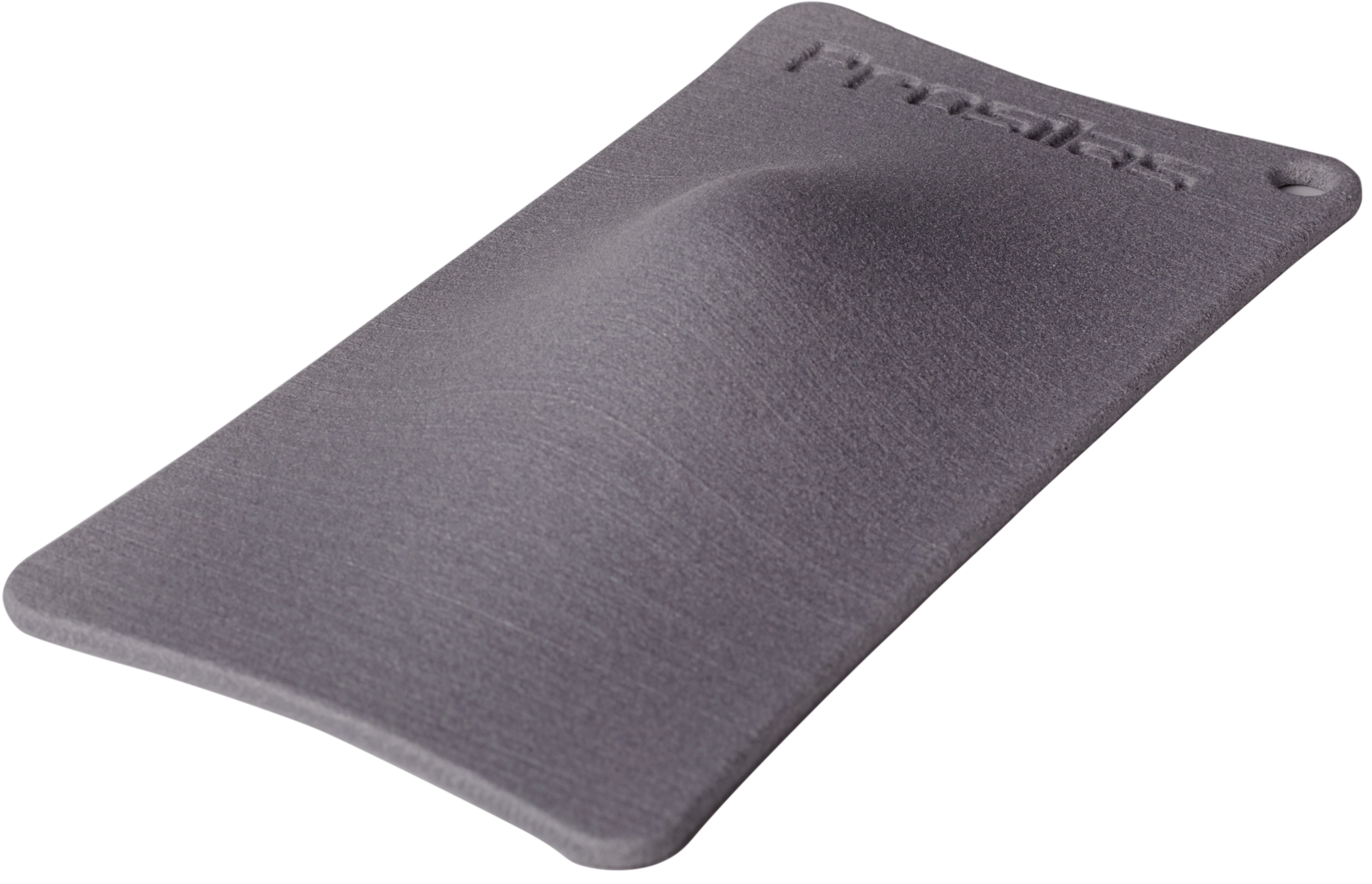