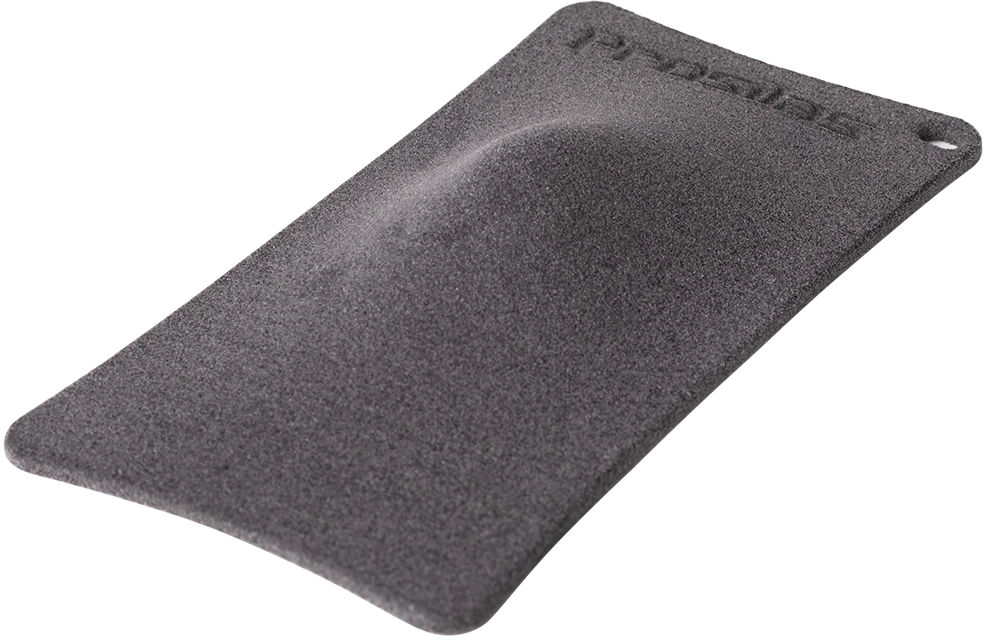
Tpu: un materiale flessibile per l’industria
TPU: Un Materiale versatile capace di soddisfare molte applicazioni industriali
Il TPU (Poliuretano Termoplastico) rappresenta un elemento fondamentale nella produzione industriale con tecnologie additive, soprattutto quando si tratta di applicazioni in stampa 3D SLS.
In Prosilas, siamo orgogliosi di lavorare con il TPU88A di BASF Forward AM, offrendo soluzioni nelle colorazioni bianco e nero, e aprendo le porte a una vasta gamma di applicazioni industriali.
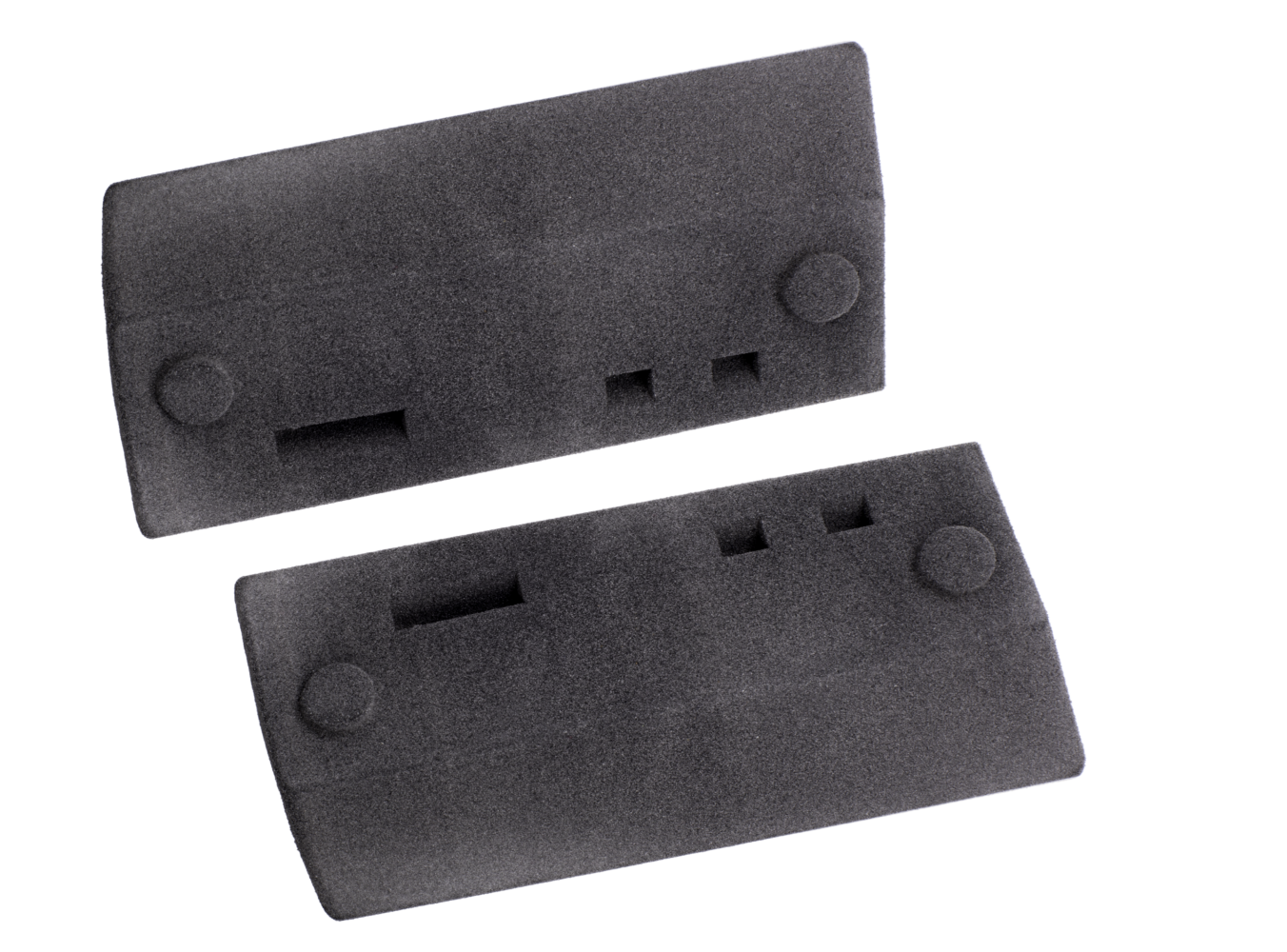
Caratteristiche del TPU 88A
Il TPU è un materiale che emula la gomma, ed è ampiamente apprezzato per la sua flessibilità, resistenza ed elasticità.
La sua lavorabilità consente la creazione di parti con eccezionali proprietà meccaniche, rendendolo ideale non solo per prototipi ma anche per produzioni in serie.
Collaborazione Produttiva con BASF Forward AM
La collaborazione tra Prosilas e BASF Forward AM ha portato a risultati significativi, come la Skeleton Sole per Philipp Plein, il caso studio Lube Volley e la validazione delle strutture lattice stampate in Ultrasint® TPU88A per il software Ultrasim®.
Questi progetti testimoniano l’impegno per l’innovazione e la sperimentazione in campo industriale.
Proprietà e Applicazioni Industriali del TPU
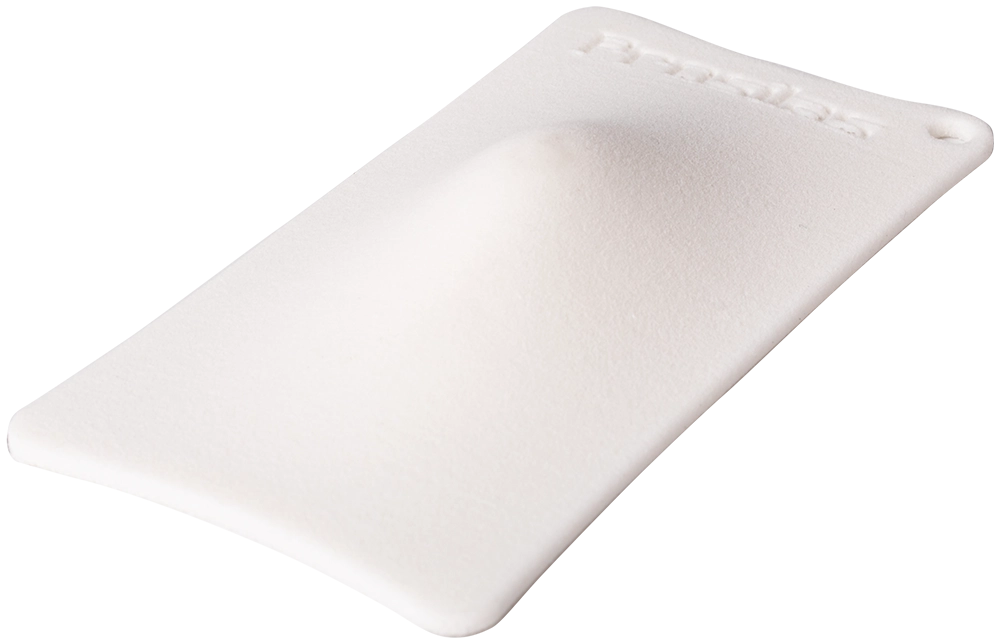
- Automotive
Il TPU eccelle nella resistenza e rigidità, rendendolo ideale per applicazioni che richiedono una struttura robusta e durevole. Nell’industria automobilistica, viene impiegato per componenti quali guarnizioni, tubi e posaggi, dove la solidità e l’integrità sono essenziali per garantire prestazioni ottimali nel tempo.
- Industria
La sua resistenza chimica lo rende prezioso in ambienti esposti ad agenti chimici aggressivi. Nell’industria industriale, troviamo il TPU impiegato in guarnizioni, posaggi e attrezzature per macchinari, dove la resistenza agli agenti chimici è fondamentale per la durata e l’efficienza delle attrezzature.
Il TPU mantiene le sue prestazioni nel tempo, garantendo stabilità e affidabilità anche in condizioni di utilizzo prolungato. Questa caratteristica lo rende particolarmente adatto per applicazioni industriali che richiedono una durata superiore nel tempo, come nel caso di guarnizioni e sigillanti per macchinari industriali.
- Medicale
La stampa 3D con TPU consente di ottenere parti con una risoluzione dei dettagli eccezionale, garantendo precisione nelle forme e nei contorni. Questa proprietà è cruciale in settori come l’industria medica, dove la precisione è essenziale per la realizzazione di prototipi e componenti per dispositivi medici come suole correttive e rivestimenti protesici.
La biocompatibilità del TPU lo rende sicuro per il contatto con la pelle, rendendolo ideale per applicazioni mediche come prototipi di dispositivi medici e componenti per dispositivi finali, dove la sicurezza e la compatibilità con il corpo umano sono fondamentali.
- Sportwear
Grazie alla sua alta resistenza agli impatti, il TPU è ampiamente utilizzato in dispositivi di protezione come caschetti di rimodellamento cranico e attrezzature per l’industria sportiva, garantendo una protezione affidabile e duratura in situazioni di potenziale impatto.
Finiture e post-process
La versatilità del TPU si estende anche alle molteplici finiture applicabili alle parti stampate in 3D.
Tra queste, verniciatura, colorazione, lisciatura chimica e diverse tipologie di coating. Dalla finitura senza trattamento alla lisciatura con vapore chimico, il TPU si adatta alle esigenze estetiche e funzionali delle applicazioni industriali.