Bimota + Prosilas Caso studio
Grazie all’additive manufacturing di Prosilas, la casa riminese sviluppa nuovi modelli ad alte prestazioni nell’arco di pochi mesi. Si tagliano così tempi e costi, con risultati di assoluta eccellenza, su strada e su pista.
Bimota è la storica casa costruttrice di motociclette, fondata a Rimini nel 1973. Nel corso degli anni l’azienda ha vissuto diversi cambiamenti ed evoluzioni, fino alla rinascita grazie all’acquisizione da parte di Kawasaki Heavy Industries: nel 2019 del 49,9%, salito al 100% all’inizio del 2023. Così, Bimota può adesso contare sulla fornitura di tecnologia di Kawasaki, motori inclusi, e sulla relativa rete di vendita.
“Abbiamo cominciato la progettazione della nuova Tesi H2 sin da subito: carrozzeria in carbonio e motore sovralimentato super performante, con le prestazioni più elevate della categoria grazie ai 230 cavalli nella versione Euro 4 e 200 per la Euro 5”, conferma Pierluigi Marconi, direttore tecnico Bimota: “Però, ci siamo ben presto scontrati con un ostacolo imprevisto da molti – il Covid e quindi la necessità di lavorare da casa. È stata in realtà l’occasione per cambiare approccio e progettare interamente la moto in 3D, aprendoci così a una serie di interessanti possibilità”.
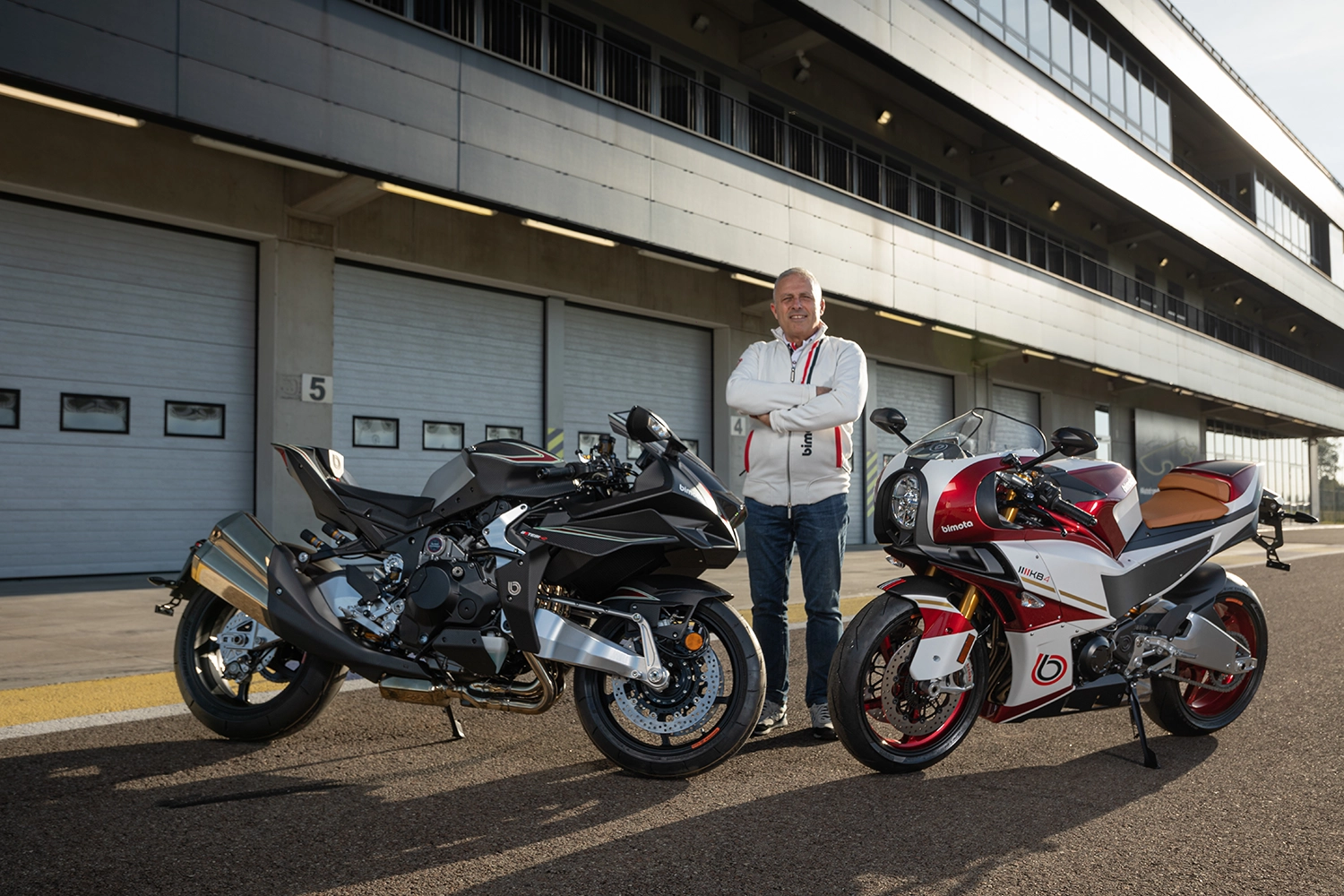
Pierluigi Marconi , Direttore Tecnico Bimota. Tesi H2 e KB4
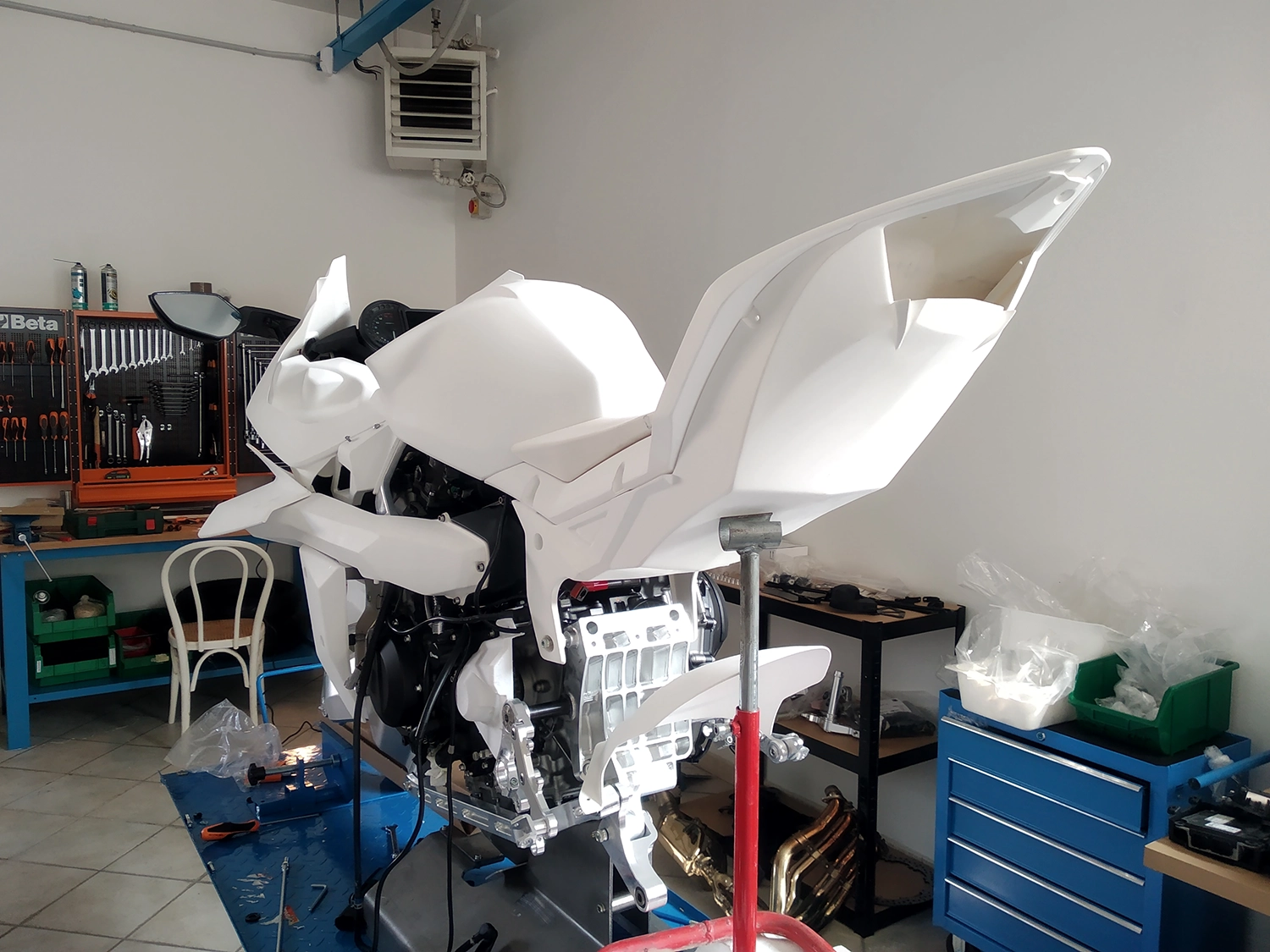
In officina Bimota il prototipo della Tesi H2
Da 12 a 4 mesi per il prototipo
Disporre del modello 3D di ogni parte della motocicletta è indubbiamente vantaggioso, perché consente di eseguire alcuni test virtuali e valutare “a schermo” l’effettiva correttezza di determinate decisioni prese dal progettista.
Però, “arriva comunque il momento in cui devi toccare con mano i pezzi, assemblarli e capire come si comportano, per stabilire se le scelte fatte sono corrette”, aggiunge Marconi: “In passato era necessario realizzare manualmente dei prototipi in Clay, dai quali costruire stampi rapidi per vetroresina. Un processo costoso e laborioso, i cui risultati non sempre erano precisissimi.
Ora invece, disponendo dei file 3D, abbiamo la possibilità di farli stampare tramite prototipazione rapida in appositi service: è così che abbiamo conosciuto Prosilas”.
Dall’idea ai primi mockup da esposizione si riescono così a ridurre le tempistiche da circa 12 a 4 mesi, con evidente riduzione anche dei relativi costi. Una volta accertata la bontà del progetto, si passa alla realizzazione delle attrezzature. Continua Marconi: “Lo sviluppo procede molto velocemente, la messa a punto dei componenti richiede qualche settimana e dal file si ottiene un prototipo stampato in 3D nel giro di un paio di giorni.
Controlliamo se le geometrie e le modifiche sono corrette o se è necessario intervenire di ancora. In questo caso, è sufficiente rimandare il file a Prosilas per ottenere il nuovo pezzo stampato da testare. In genere con un paio di passaggi otteniamo il risultato migliore possibile. In precedenza era necessaria la messa a punto degli stampi, un’attività molto costosa: nel migliore dei casi richiedeva qualche modifica, talvolta persino il suo rifacimento”.
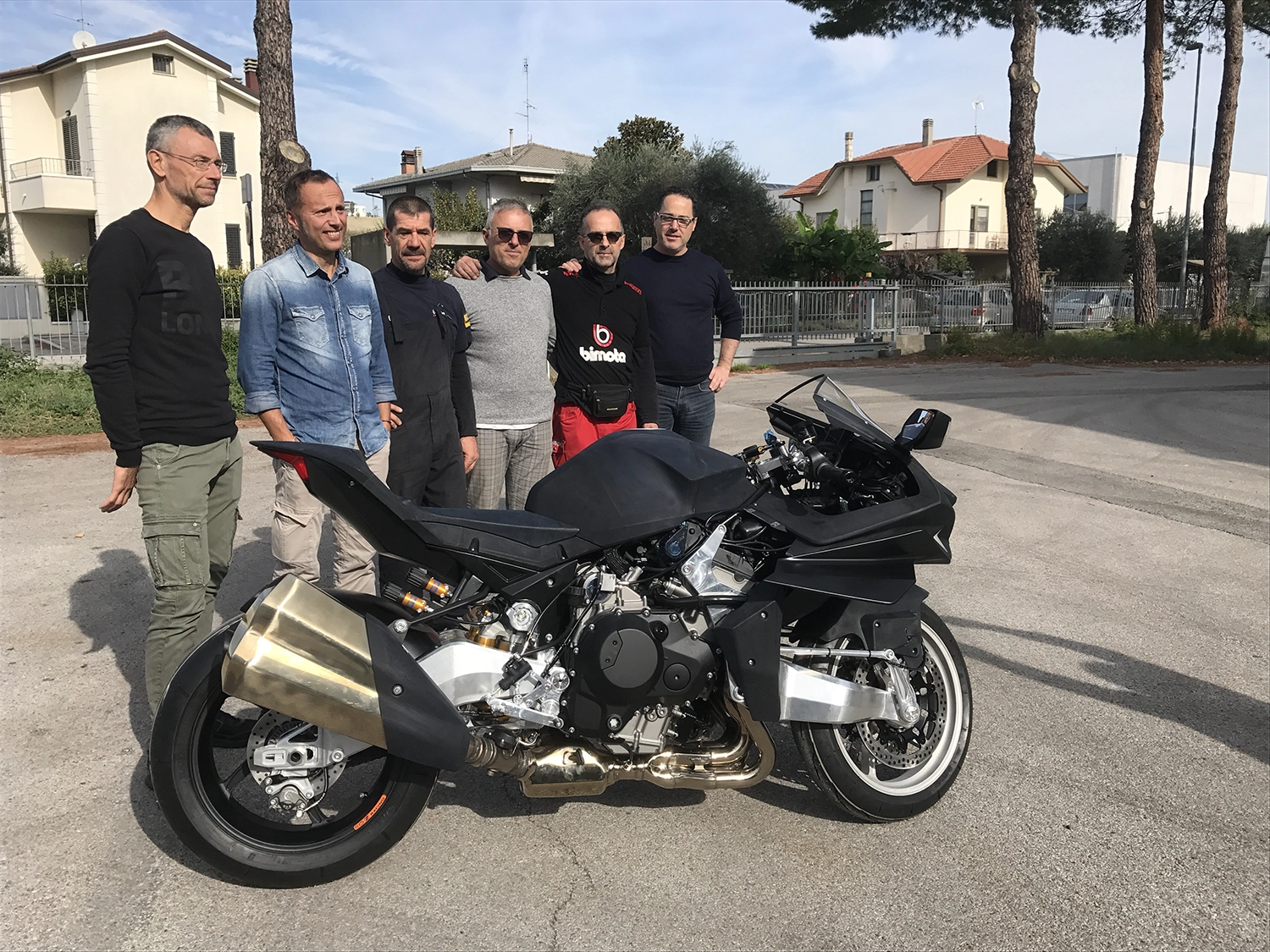
Staff Bimota con il prototipo della Tesi H2
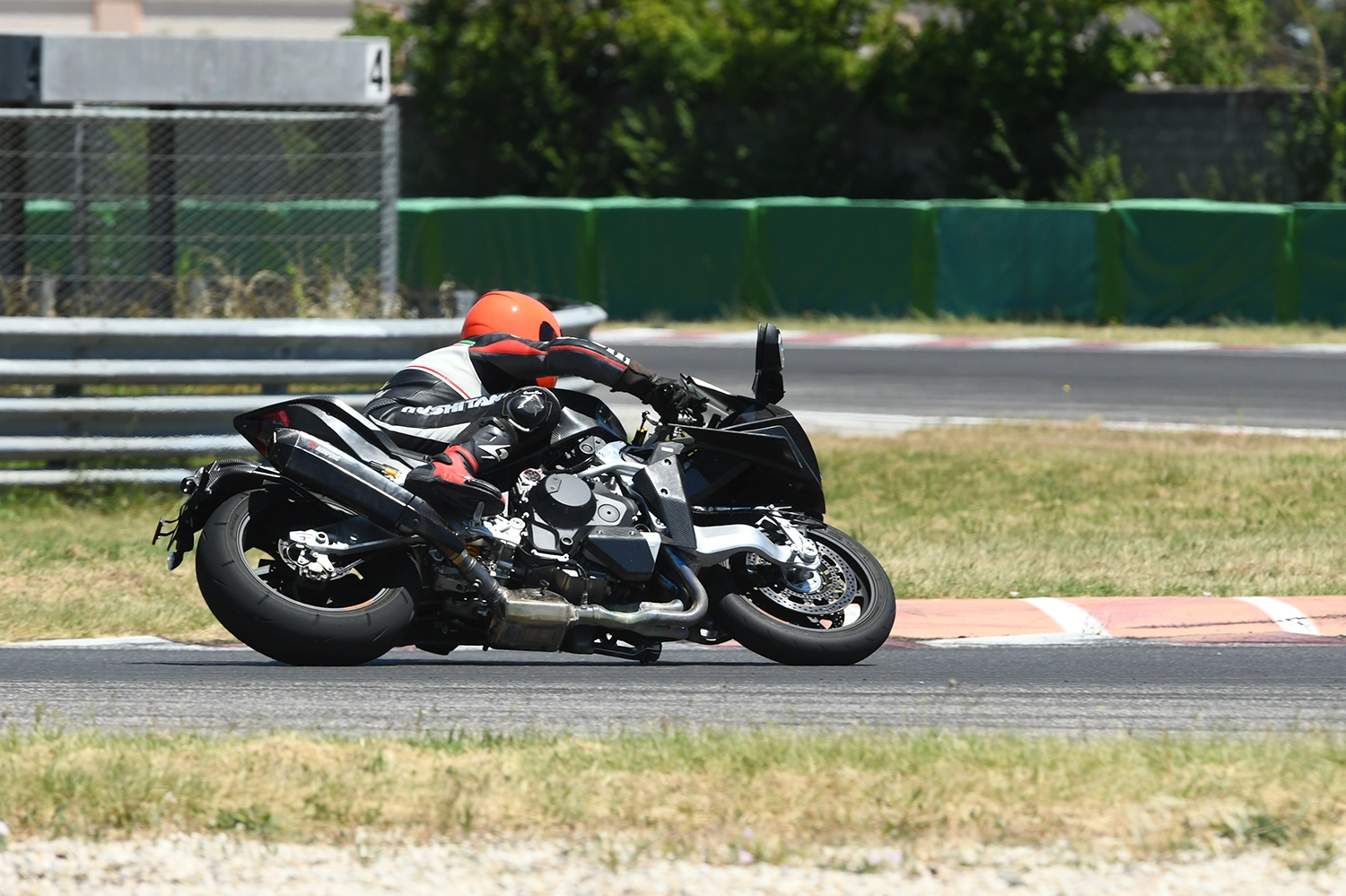
Test in pista con la Tesi H2
Con Prosilas la stampa 3D funziona anche su pista
Per una casa come Bimota è il risultato nella prova in pista: “Quando prenoti una giornata di test e organizzi la trasferta di alcuni ingegneri dal Giappone”, spiega Marconi, “non puoi mancare la consegna di un componente. Una giornata di test può costarci decine di migliaia di euro e oggi nessuno è disposto a sperperare un simile investimento”.
Quindi, è necessario trovare un partner in grado di realizzare anche i particolari più complessi, che difficilmente possono essere sviluppati solo sulla base di una simulazione fluidodinamica. Le molteplici variabili in gioco, come la temperatura dell’aria o la direzione dei flussi in entrata, rendono più pratico progettare un file 3D di buona qualità da utilizzare per prove pratiche su strada.
Ed è qui che la prototipazione rapida di Prosilas si dimostra affidabile e utile. “Una volta progettate alcune parti di carrozzeria e dei condotti, in un giorno abbiamo ottenuto i pezzi stampati e li abbiamo testati”, spiega Marconi: “L’uso di Nylon caricato con fibra di vetro ( PA12 GF) è ideale in termini di resistenza meccanica e alle alte temperature. Alcune parti sono infatti molto vicine all’impianto di scarico o ai radiatori e devono resistere a lungo, per offrirci i dati utili per comprendere se siamo sulla giusta strada. Inoltre è un materiale che non si deforma, caratteristica molto utile quando viene usato per l’accoppiamento di parti di carrozzeria”.
Tesi H2 ha dato il via a un percorso totalmente votato al 3D per Bimota. Con la KB4, dall’accattivante aspetto Vintage Inspired, l’additive manufacturing di Prosilas ha permesso ad esempio di realizzare un complesso sistema canalizzatore per l’aria. TERA, ultima nata del costruttore di Rimini, si è distinta in occasione della scorsa edizione di EICMA – Milano grazie a due kit esclusivi, che presto verranno aggiornati con ulteriori appendici aerodinamiche.
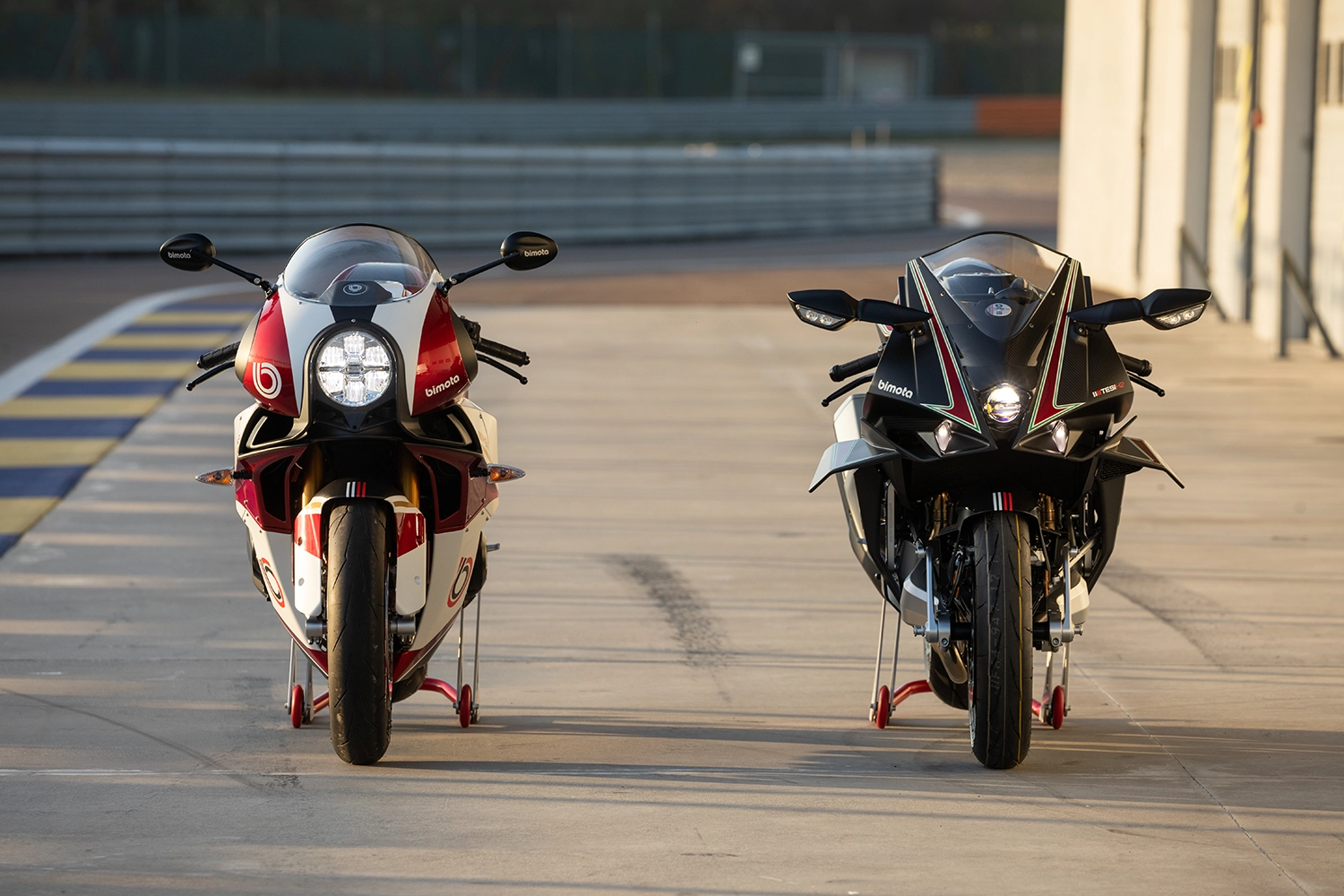
Vista frontale della Tesi H2 e della KB4
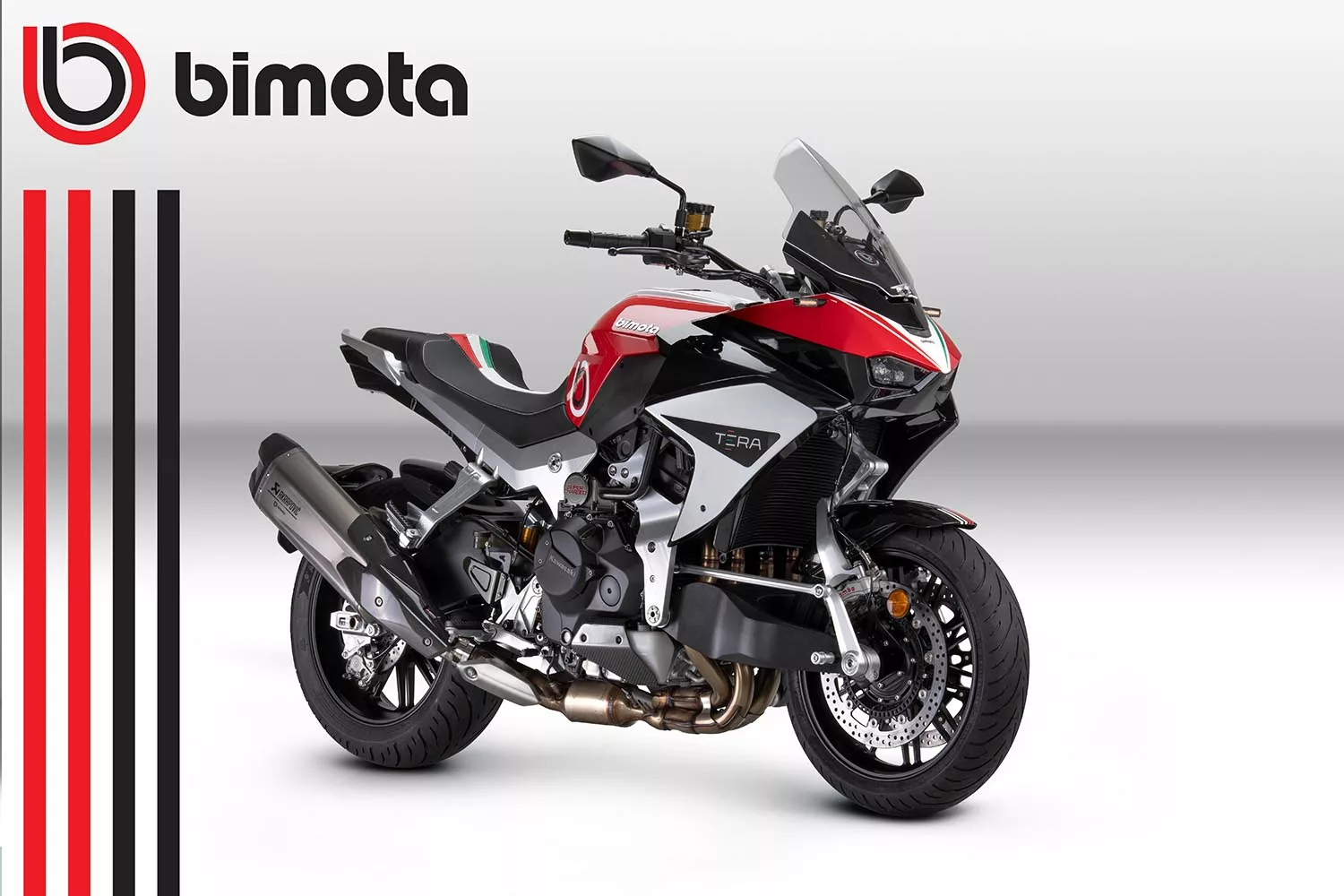
Bimota Tera
Il rispetto dei tempi stabiliti
Per Bimota l’approccio con la stampa 3D non era stato subito positivo. “Avevamo lavorato con fornitori che ci mandavano componenti deformati, fuori tolleranza, alcuni addirittura scollati”, ammette Pierluigi Marconi: “così i vantaggi della prototipazione rapida erano vanificati, perché se devi intervenire su un pezzo e questo nei test non risponde come ti aspetti, non puoi sapere se la colpa è del progetto, del materiale o della stampa. Anche per questo, secondo me, il fattore costo è secondario: spendere il 10% in meno, ma avere particolari che non rispecchiano le nostre aspettative, significa buttare soldi. Lo stesso vale per le tempistiche di consegna: se non posso fare affidamento su un fornitore, significa che è quello sbagliato. Quando abbiamo incontrato il personale di Prosilas, invece, abbiamo constatato sin da subito una grande attenzione nei confronti delle nostre esigenze e delle criticità del nostro lavoro”.
Un altro dettaglio critico è legato alle tempistiche: se da un lato la prototipazione consente di ridurre i tempi di sviluppo, dall’altro impone che la catena di fornitura sia assolutamente affidabile. Un’altra sfida che Bimota e Prosilas hanno vinto insieme. “Prosilas è tra i fornitori più precisi e puntuali che abbiamo mai avuto”, conclude Marconi: “Forniamo loro il file e otteniamo una tempistica di consegna che per noi è cruciale, poiché su quella impostiamo le successive attività”.
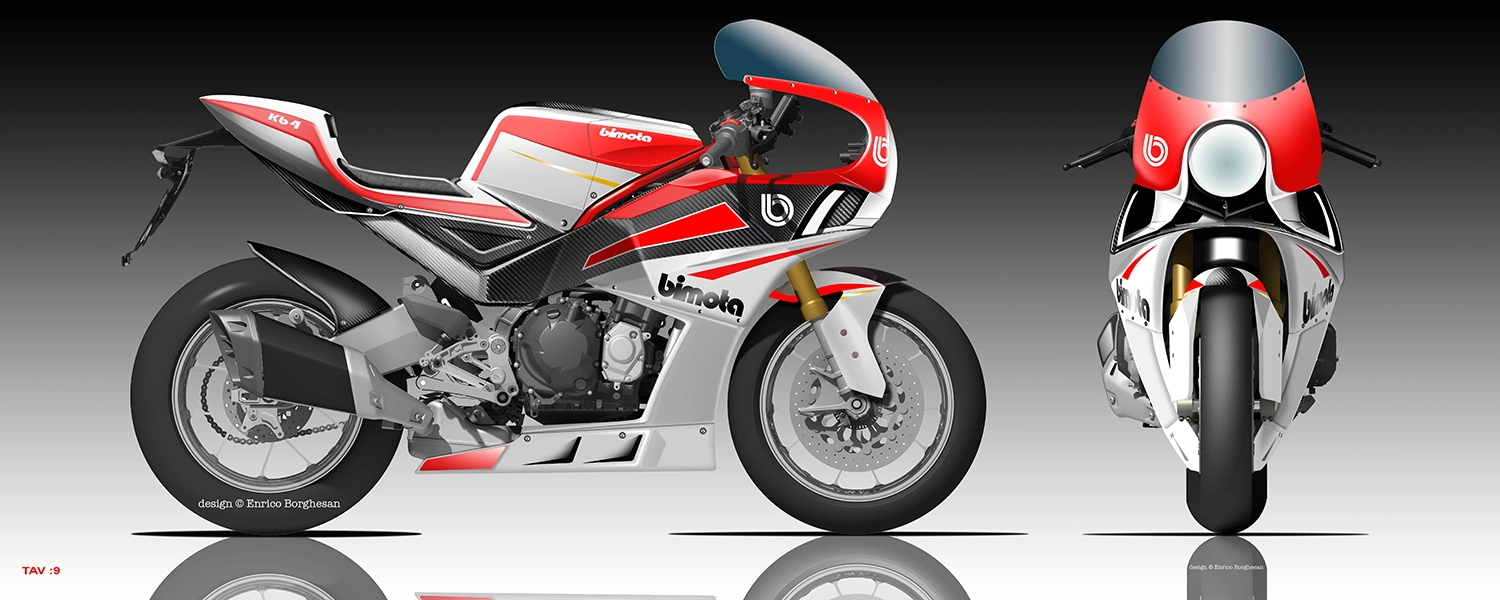
Render 3d della Bimota KB4
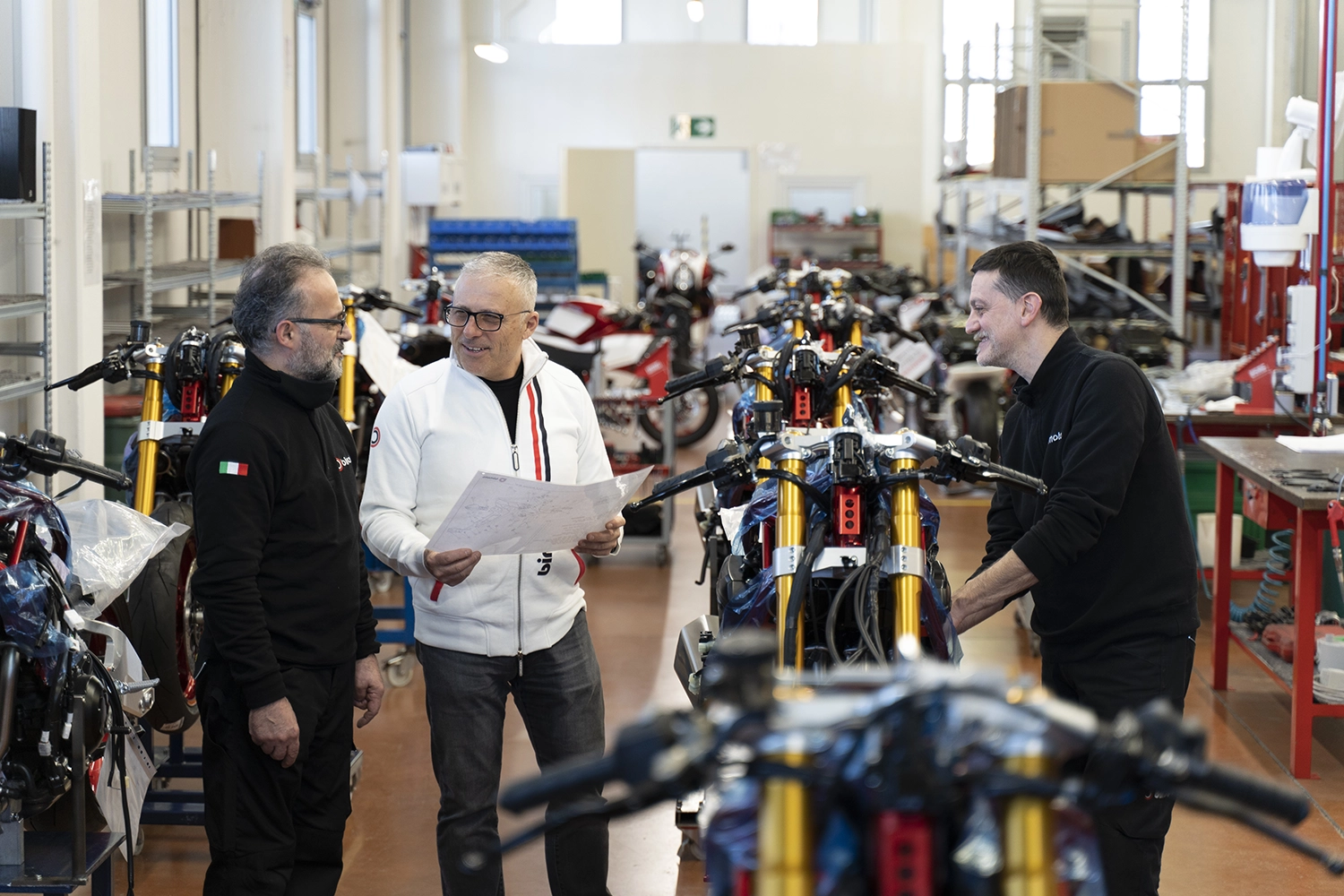
Pierluigi Marconi e lo staff Bimota in officina
Un futuro ricco di sfide per Bimota
Oggi che Bimota progetta in 3D i nuovi modelli e sfrutta la tecnologia additiva di Prosilas, tempi e costi del processo hanno subito un netto taglio. L’azienda resta alla costante ricerca di nuove idee e soluzioni per fare ulteriori passi in avanti sotto ogni aspetto: dalle prestazioni delle proprie moto al taglio dei budget di sviluppo, sempre con un occhio alle tempistiche complessive.
La consulenza degli esperti di Prosilas può rivelarsi ancora una volta l’arma vincente per raggiungere i risultati voluti e consolidare il successo di Bimota sul mercato.