From Rapid Prototyping to Industrial Production: The Advantages of 3D Printing
3D printing, initially developed as a rapid prototyping technology, has now evolved into an established solution for serial production as well.
Thanks to its numerous benefits, industrial 3D printing can provide companies with a significant competitive advantage, allowing them to reduce development and production times, cut costs, and enhance product quality.
Prototyping
The term “production” is often not associated with 3D printing technologies, as the very nature of additive manufacturing systems, at least in their initial conception, was intended for the creation of individual pieces: models or prototypes.
In the early development phase, additive technologies facilitated the rapid creation of prototypes and aesthetic models, useful in expediting all testing phases, as well as research and development for new applications.
Production
Today, thanks to advanced additive manufacturing systems, it is possible to produce functional prototypes, small to medium batch productions, or even mass productions.
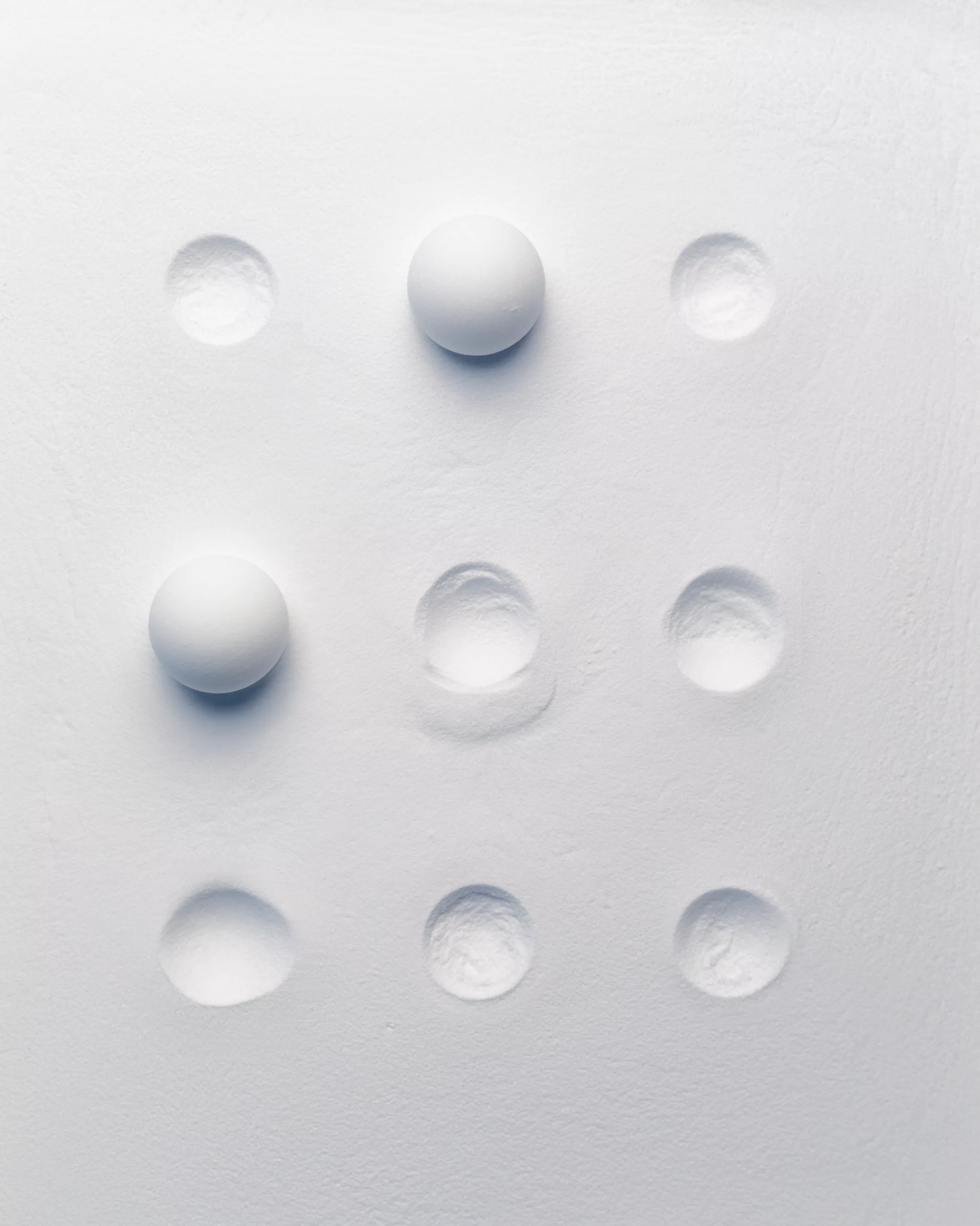
Advantages
Unlike the creation of individual parts or prototypes, additive manufacturing opens up highly advantageous scenarios that can improve and expedite aspects related to the development of new applications designed for mass production.
The main advantages of production with 3D printing can be summarized in five points:
1. Reduction of Development and Production Times:
3D printing allows for the rapid creation of functional prototypes, thereby accelerating the process of developing new products.
Moreover, even pre-series production with 3D printing can be carried out in much shorter times compared to traditional production technologies.
It is possible to introduce batches of components or objects into the market for collecting data from tests or feedback from end-users, facilitating the optimization of shapes or functions.

For example, a company manufacturing components for the aerospace industry can use 3D printing to create functional prototypes within a few days, instead of the months or even years required by traditional prototyping technologies.
In this way, the company can expedite the development process of new aircraft and reduce development costs.
2.Cost Reduction:
3D printing can decrease production costs through the use of advanced materials and the reduction of material waste. Materials employed in 3D printing are often lighter and more durable than traditional materials, potentially reducing product weight and, consequently, transportation and energy consumption costs.
Additionally, 3D printing allows for minimizing material waste since the material is used only to create the necessary parts of the product.
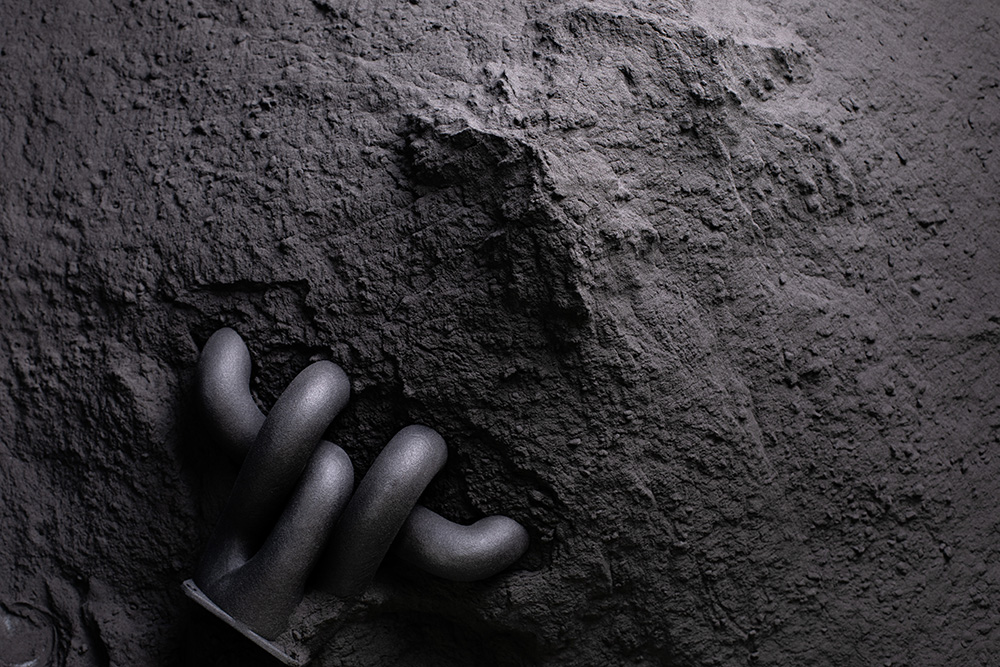
For instance, a company manufacturing components for the automotive industry can leverage 3D printing to produce lighter and more durable components.
This can contribute to enhancing vehicle efficiency, reducing fuel consumption, and promoting the metal-replacement process.
3. Quality Improvement:
3D printing can ensure greater precision and repeatability of products, enabling the creation of complex geometries and shapes impossible to achieve with traditional production technologies.
3D printing allows for the production of products with very tight tolerances, meeting the most stringent requirements.
Moreover, it can be used to manufacture products with intricate geometries that would be impossible to achieve with traditional production technologies.
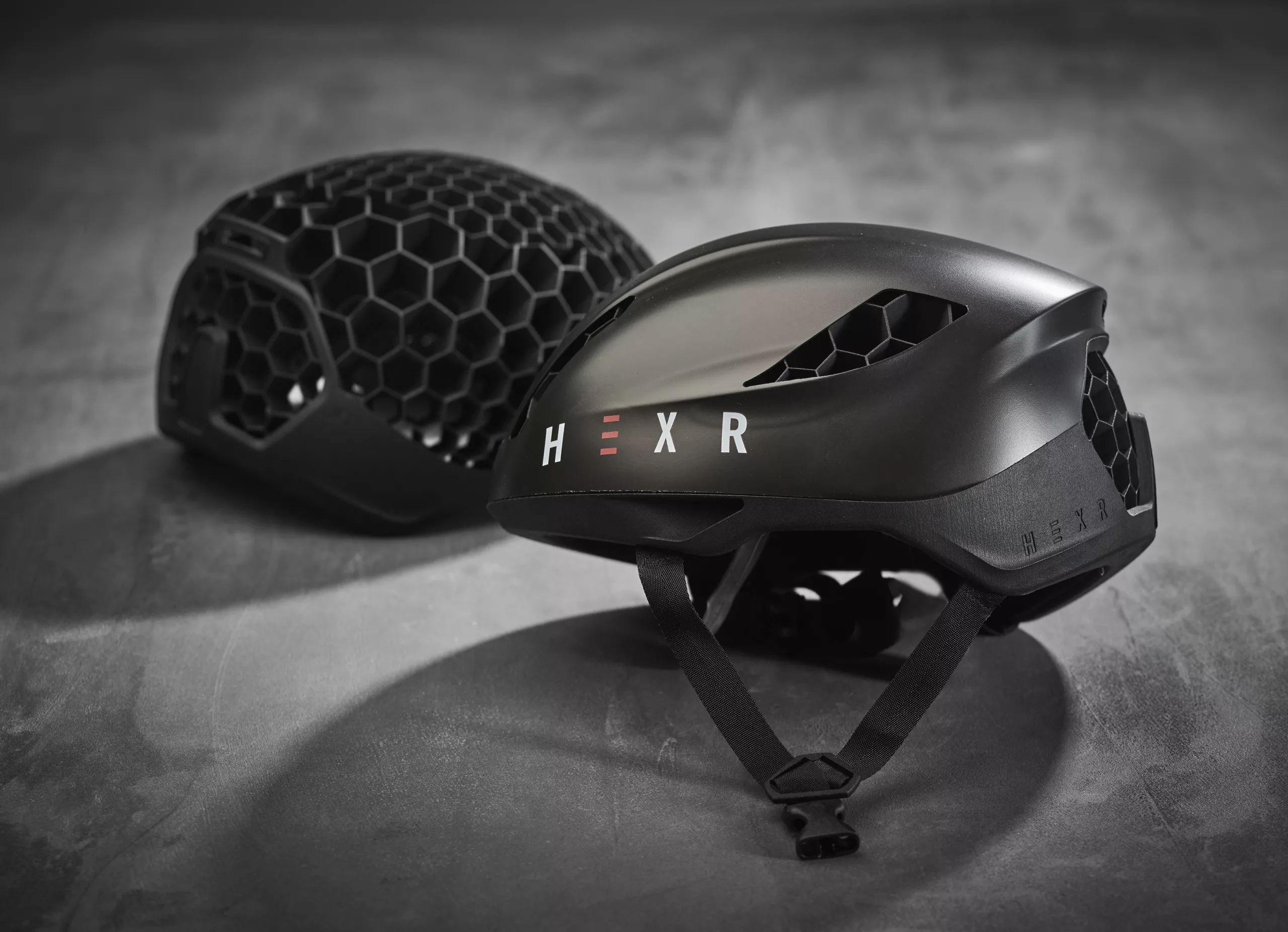
For example, a company specializing in medical prosthetics can utilize 3D printing to create customized prosthetics that perfectly fit the patient.
By employing 3D scanning technologies and reverse engineering, an exact model of the part can be created to tailor the prosthetic precisely to the individual’s needs.
4. Product Customization:
3D printing enables the customization of products based on specific customer needs, creating unique and distinctive items.
With 3D printing, products can be crafted with personalized features such as dimensions, shape, color, or material. This can be a competitive advantage for companies aiming to provide their customers with unique and customized products.
For instance, a company manufacturing eyewear could use 3D printing to create personalized jewelry with unique shapes and colors.

5. Production Flexibility:
3D printing is a flexible technology that can be adapted to various production needs, enabling the creation of products of any size and complexity.
3D printing can be employed to manufacture products of various sizes, ranging from small components to large objects.
With our industrial SLS printers, we can produce objects of considerable dimensions (680x370x540mm).
Furthermore, 3D printing can be used to create products of any complexity, including those with intricate geometries or shapes impossible to achieve with traditional production technologies.
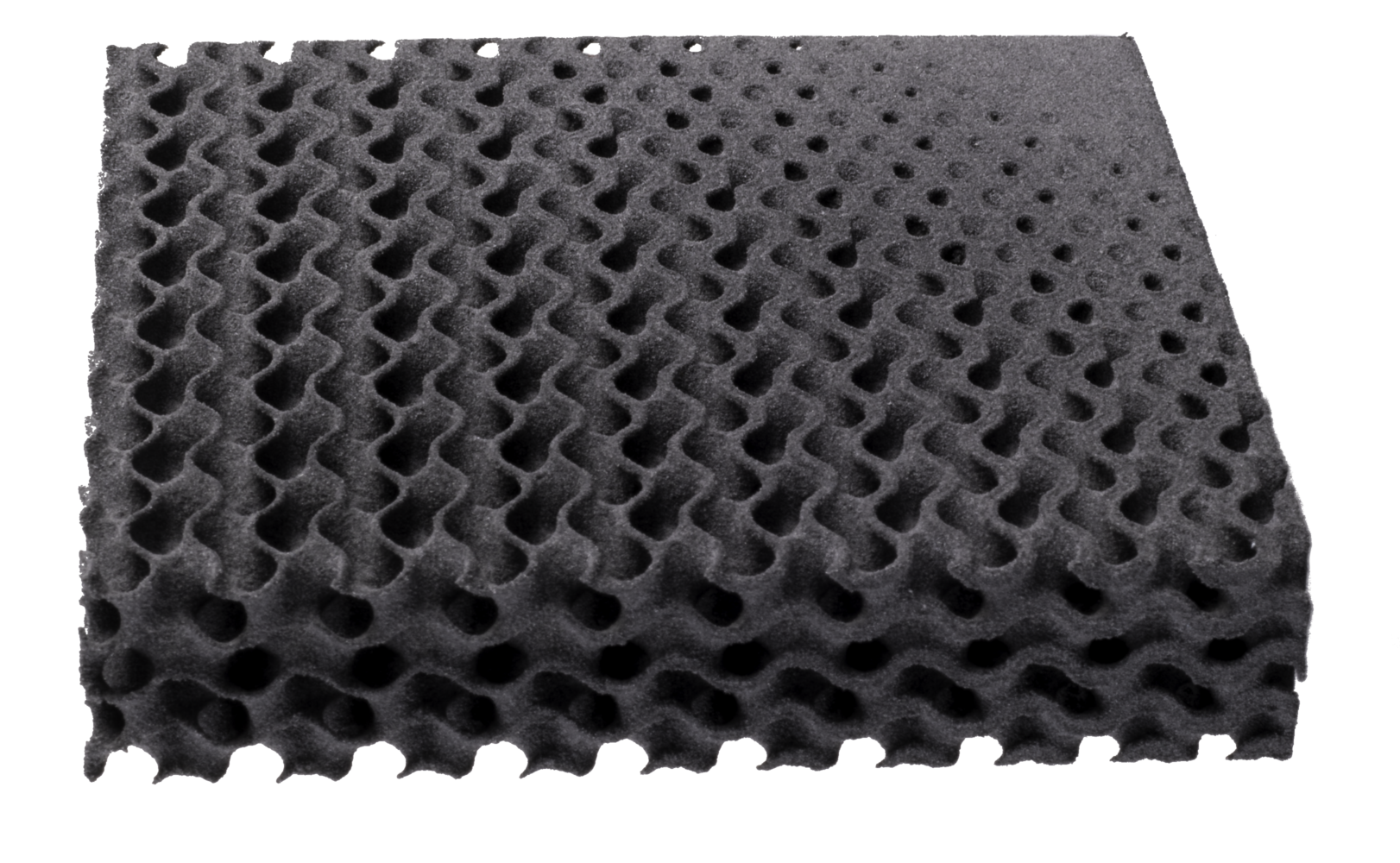
Entrusting production to 3D printing offers significant advantages to companies in terms of reducing development times, controlling costs, improving quality, enabling customization, and providing production flexibility.
This technology is emerging as a versatile and innovative solution, allowing businesses to successfully tackle competitive challenges and respond effectively to market needs.
With proper workflow and optimized design, 3D printing continues to prove itself as a key catalyst for the evolution of the manufacturing industry.