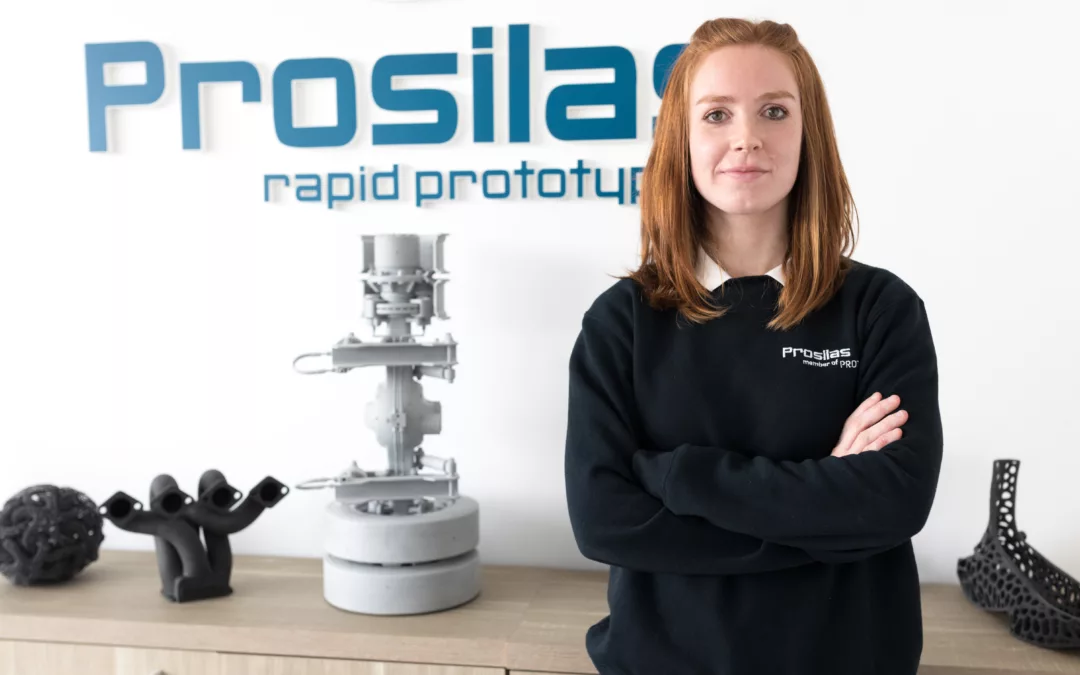
Design tolerances in 3D printing
Tips & Tricks: What are design tolerances?
Exploring design tolerances in SLS 3D printing
Design Tolerances
Let’s continue our journey into the world of tolerances, this time delving into the concept of design tolerances.
What are they, and how should they be managed? In this exploration, we will unveil the crucial role of tolerances in engineering, design, and the production of mechanical components.”
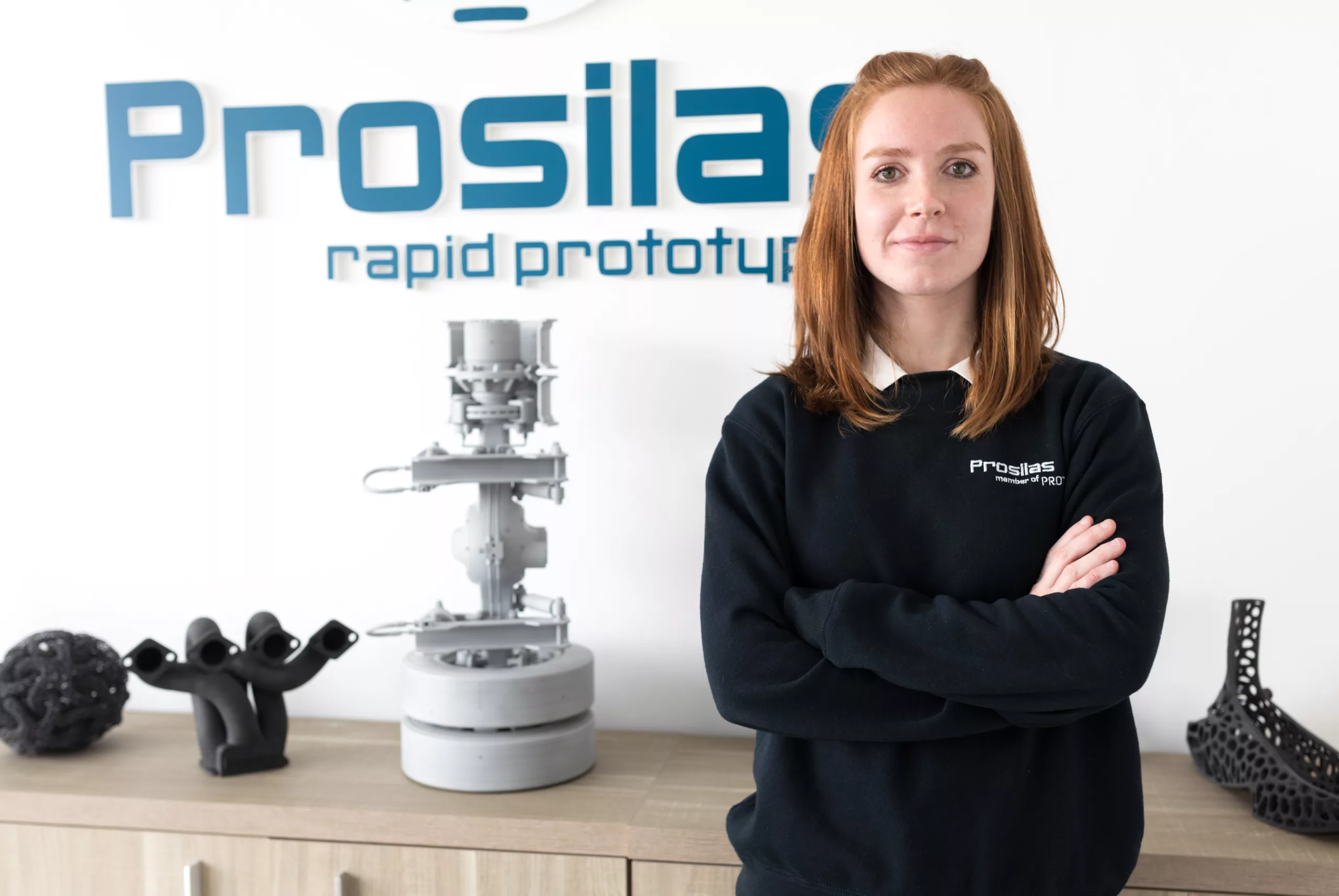
Why using tolerances?
The use of tolerances is a common practice in various industries, and their role becomes particularly evident in ensuring the flawless coupling of components.
But what exactly are design tolerances?
When designing or manufacturing a component, achieving precise dimensions in every unit produced can be a challenge.
Materials, subject to variations in temperature and other factors, can expand or contract. This is where tolerances come into play, defining the limits within which a specific dimension can vary without compromising the functionality of the part.
Prosilas Contribution
At Prosilas, our expertise in manufacturing processes, tolerances, and materials allows us to provide valuable input during the design phase.
Our targeted advice supports engineers and designers in achieving optimal results, ensuring the proper functioning of the parts
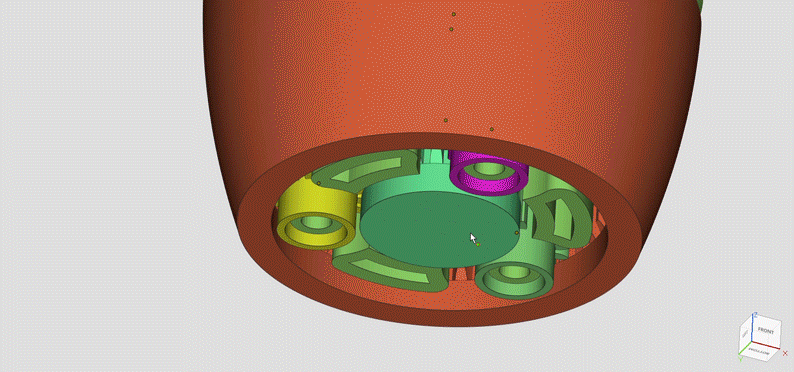
Managing Tolerances in 3D Printing
When dealing with the 3D printing of two parts intended to mate, recommended tolerances typically range around one-tenth to two-tenths of a millimeter. These targeted specifications ensure precise mating/fitting, eliminating potential issues of unwanted play.
If the component involves movable sections or joints and requires integrated printing, suggested tolerances increase to around three-tenths of a millimeter.
This distance takes into account the presence of unsintered powder between surfaces and the heat generated by the machine, preventing unintended fusions between moving parts.
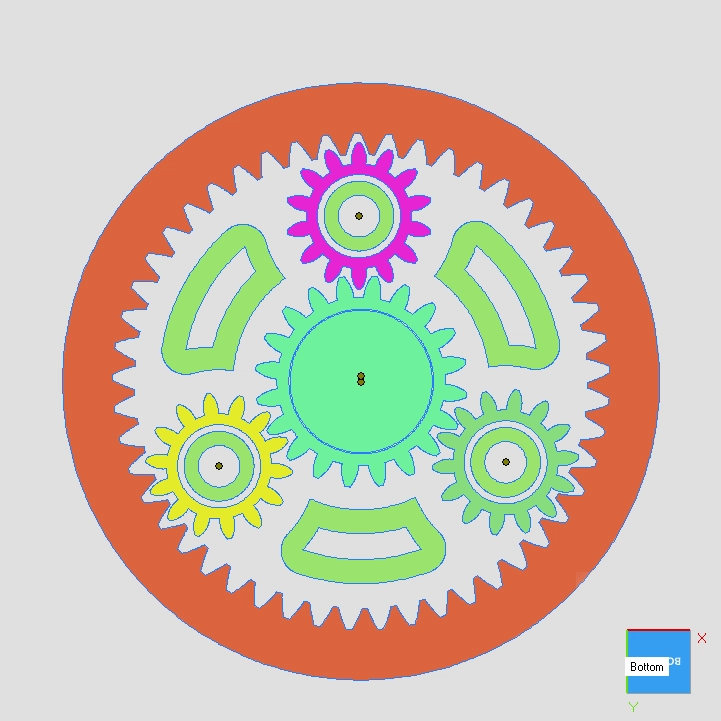