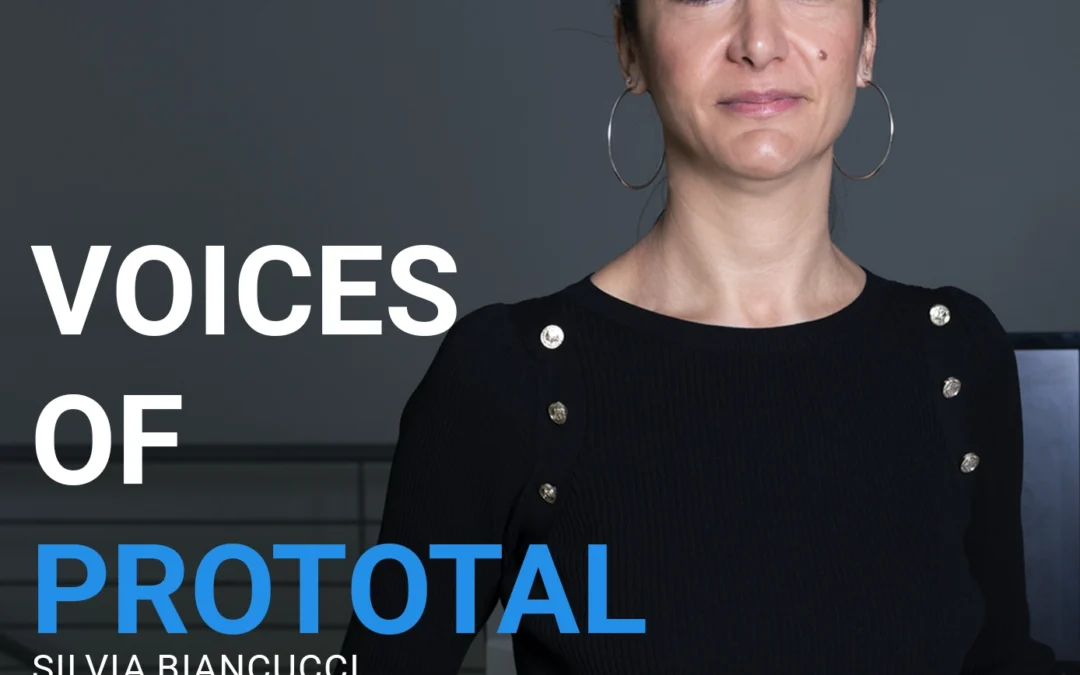
Voices of Prototal – Silvia Biancucci
SILVIA BIANCUCCI
ADMINISTRATION MANAGER
“There is nothing we can’t do, we just need to put in the effort and determination.”
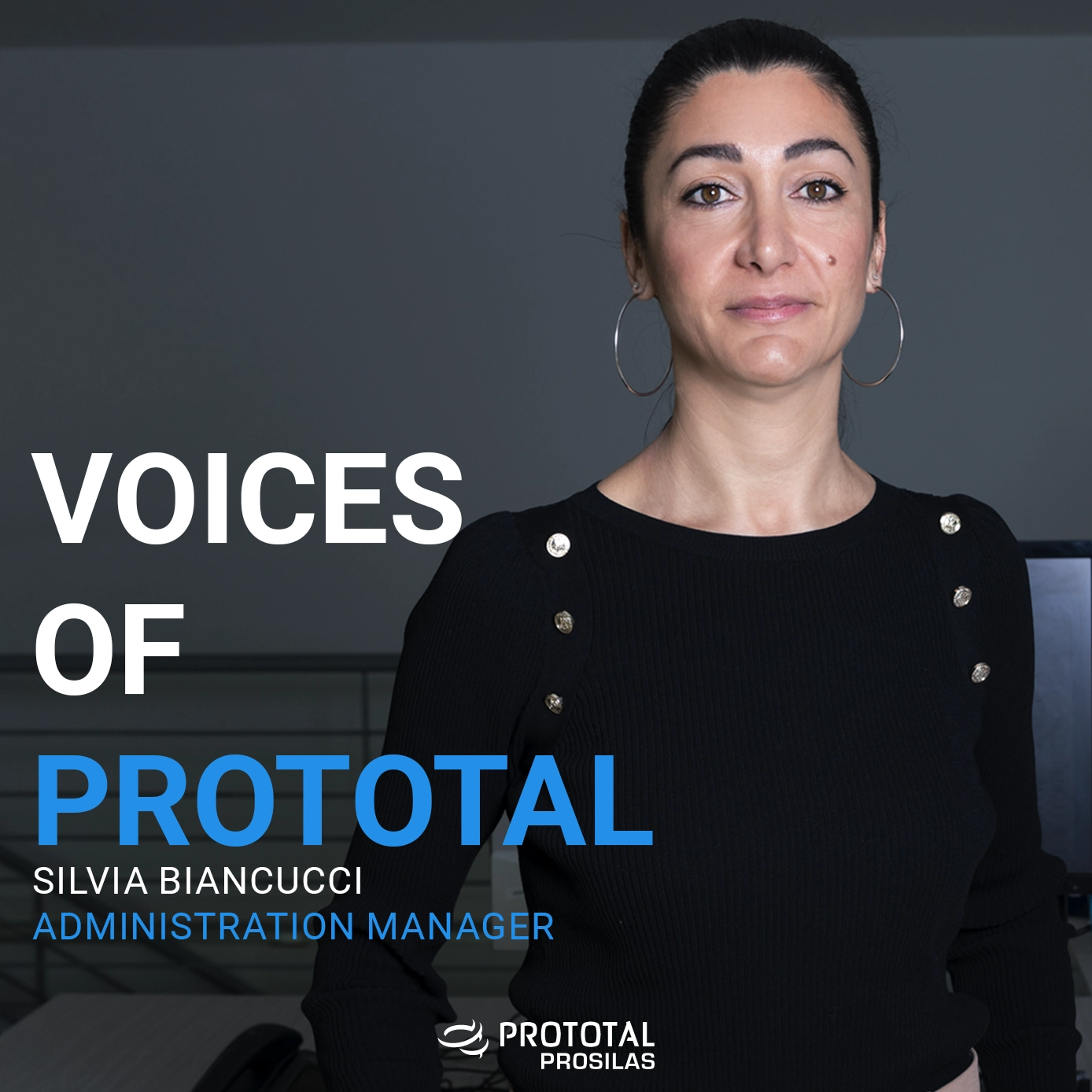
What is your professional background?
“My professional journey began in 2001, when I took my first steps as an accountant. Over the years, I’ve been fortunate to grow and develop on the job, learning something valuable from every consultant, colleague, and manager I’ve worked with. Each of them has contributed a piece to the puzzle that defines my skills today. The path that led me to Prototal Group was somewhat unexpected: I was working for an American luxury shoe company when, through a consultant, I came across Prosilas. Joining this group has been incredibly stimulating, and every day I am proud to be part of such a dynamic system.”
What gives you energy outside the office?
“My true passion is traveling. Whether alone, with family, or friends, every trip is an opportunity to discover, grow, and recharge. When I need to relax, I love taking a walk in nature with my dog—it’s my favorite way to clear my mind. I also enjoy reading and listening to podcasts, which keep my mind active, and I practice yoga to stay flexible, both physically and mentally.”
How do you stay motivated, and what is your general work philosophy?
“My approach to work is very similar to my approach to life: I don’t stop in the face of challenges. My motivation lies in knowing that I can contribute to something meaningful, being an active part of a system, and achieving results, no matter how big or small. I am a direct and decisive person, qualities I consider essential for my role. I try to tackle difficulties with practicality, using humor to ease tense moments and finding solutions that work for everyone.”
Pride and challenges
“Working at Prototal excites me, but it comes with its challenges. Transitioning to a new system after the acquisition was a complex moment but also the most stimulating of my career. It’s in challenges that opportunities for growth arise. On the other hand, tight deadlines can be demanding, requiring impeccable management. To handle these, I rely on strict procedures and checklists that help me stay focused and precise.
My goal is to keep improving: standardizing repetitive tasks and dedicating more time to thorough control and verification work. In the short term, I plan to perfect my English with an intensive course abroad, as I firmly believe that learning never ends.”
My advice to beginners?
“Humility, consistency, dedication, and seriousness. And never give up: even when faced with challenges, push forward with determination.”
Silvia Biancucci – Administration Mananger Prototal Prosilas