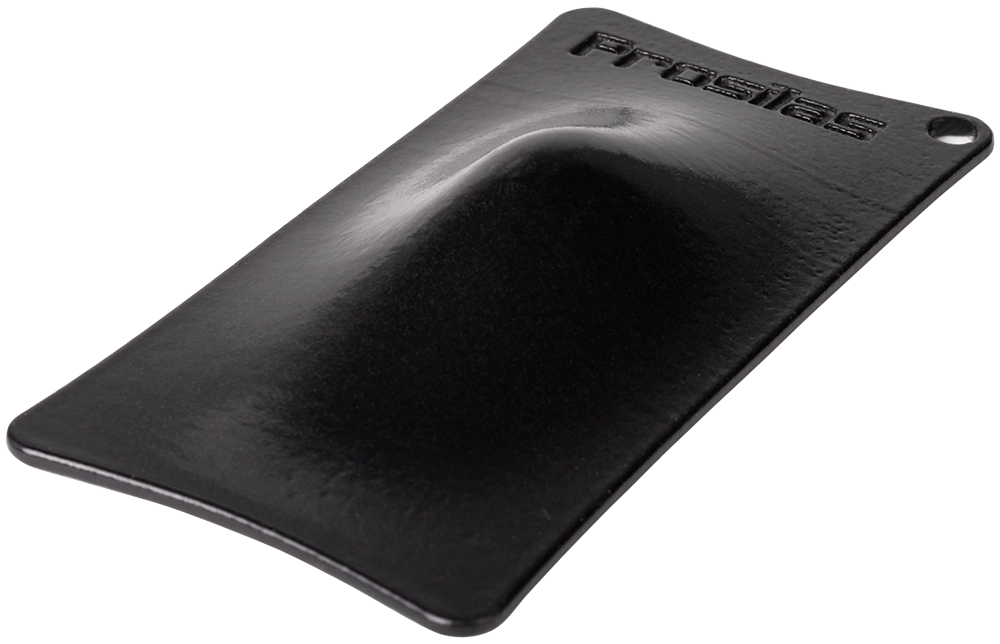
How vapor smoothing improves the quality of 3D-printed parts
Vapor Smoothing in 3D Printing: Optimizing the Performance of Printed Parts
In the world of 3D printing, the quest for methods to enhance the performance and aesthetic appearance of produced parts is a constant endeavor.
Among the various post-production techniques available, vapor smoothing stands out for its effectiveness in imparting new properties and significant improvements to printed parts.
How does the vapor smoothing process work in SLS 3D printing?
The process takes place within a processing chamber, where a series of chemical agents, selected based on the material of the part, act on the 3D-printed surfaces, making them uniform and smooth to the touch.
This system can simultaneously treat hundreds of parts, ensuring a consistent treatment for all products within the working chamber.
The potential
Vapor smoothing is a post-production process primarily applied to 3D-printed parts to enhance their surface finish, strength, and aesthetic appearance.
This technique offers several advantages, including:
- Surface Finish Improvement: Surfaces of 3D-printed parts can exhibit irregularities and porosity due to the 3D printing process. Vapor smoothing acts to eliminate these imperfections, providing surfaces with a smooth and uniform finish.
- Glossy Surfaces: One of the most appreciated features of chemical smoothing is its ability to give parts a glossy and shiny finish. This not only enhances the aesthetic appearance of the parts but also makes them more appealing for applications where appearance matters.
- Porosity Removal: Surface porosities can compromise the strength and durability of 3D-printed parts. Vapor smoothing can reduce or completely eliminate these porosities, thereby increasing the strength and lifespan of the parts.
- Improved Strength: Through the application of specific chemical agents, chemical smoothing can enhance the resistance of printed parts to liquids, chemicals, and mechanical stress. This makes them more suitable for a wide range of industrial and commercial applications.
- Ease of Cleaning and Maintenance: The smooth and uniform surfaces obtained through vapor smoothing simplify the cleaning and maintenance operations of printed parts, reducing the time and costs associated with these activities.
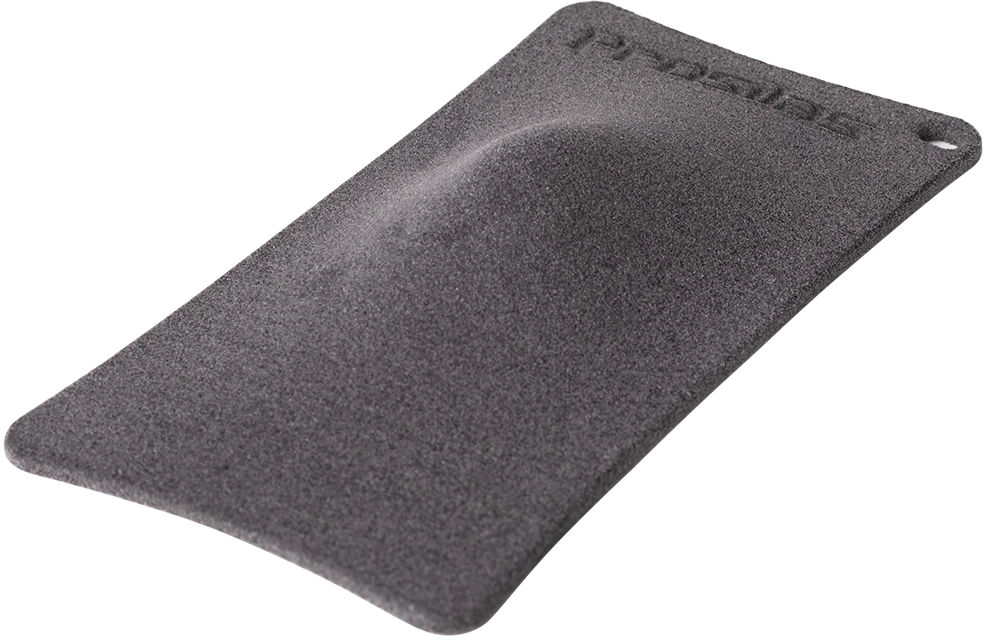
BEFORE
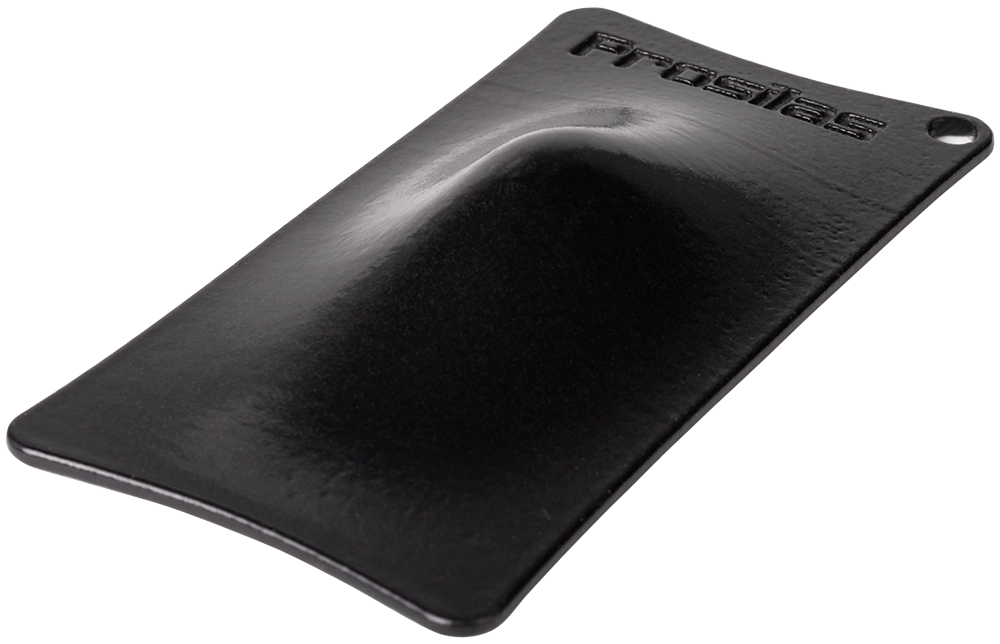
AFTER
Applications and Advantages
Vapor smoothing finds application in a variety of sectors, including aerospace, automotive, medical, and consumer industries. Parts printed through 3D printing technology can undergo this process to achieve optimal performance and a high-quality appearance.
This treatment represents a crucial step in the post-production process of 3D-printed parts. Thanks to its numerous advantages, this technique enables the production of parts with optimal performance, impeccable surface finishes, and increased durability.
For anyone involved in the production of 3D-printed parts, chemical smoothing emerges as an option to consider in ensuring the success of their projects and meeting the needs of clients.
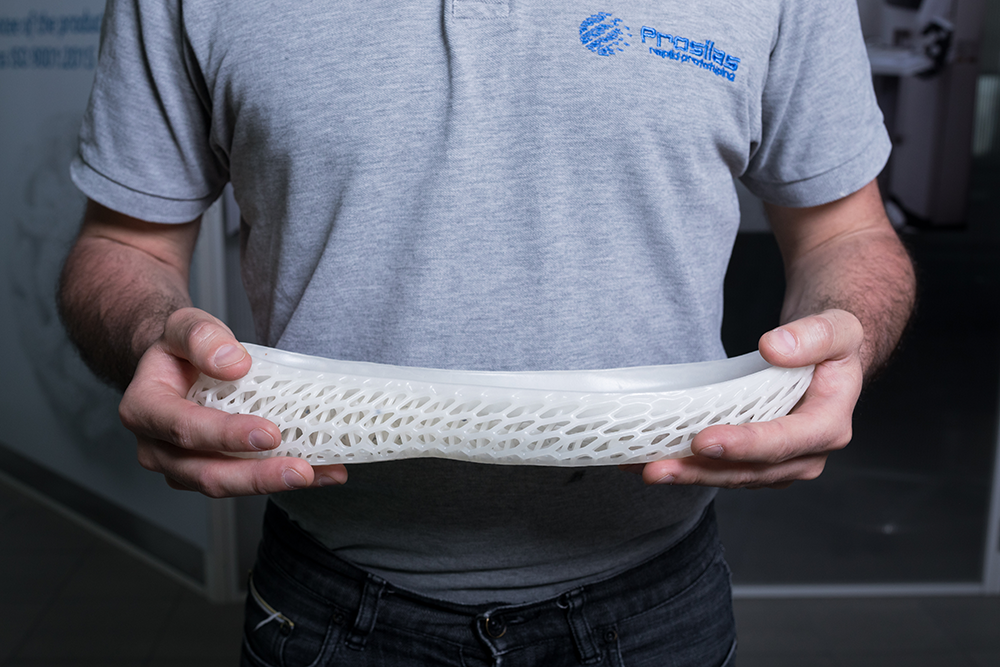