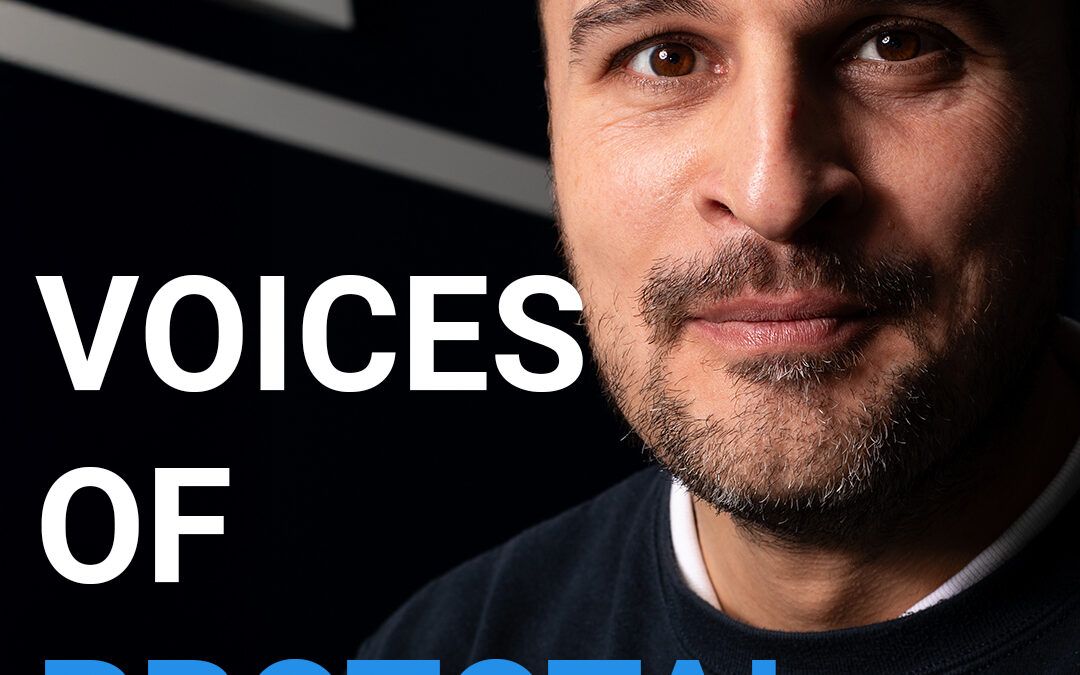
Voices of Prototal – Luca Ferroni
LUCA FERRONI
TECHNICAL MANAGER
“A superficially done task doesn’t give satisfaction. And it often takes the same amount of time as doing it well.”
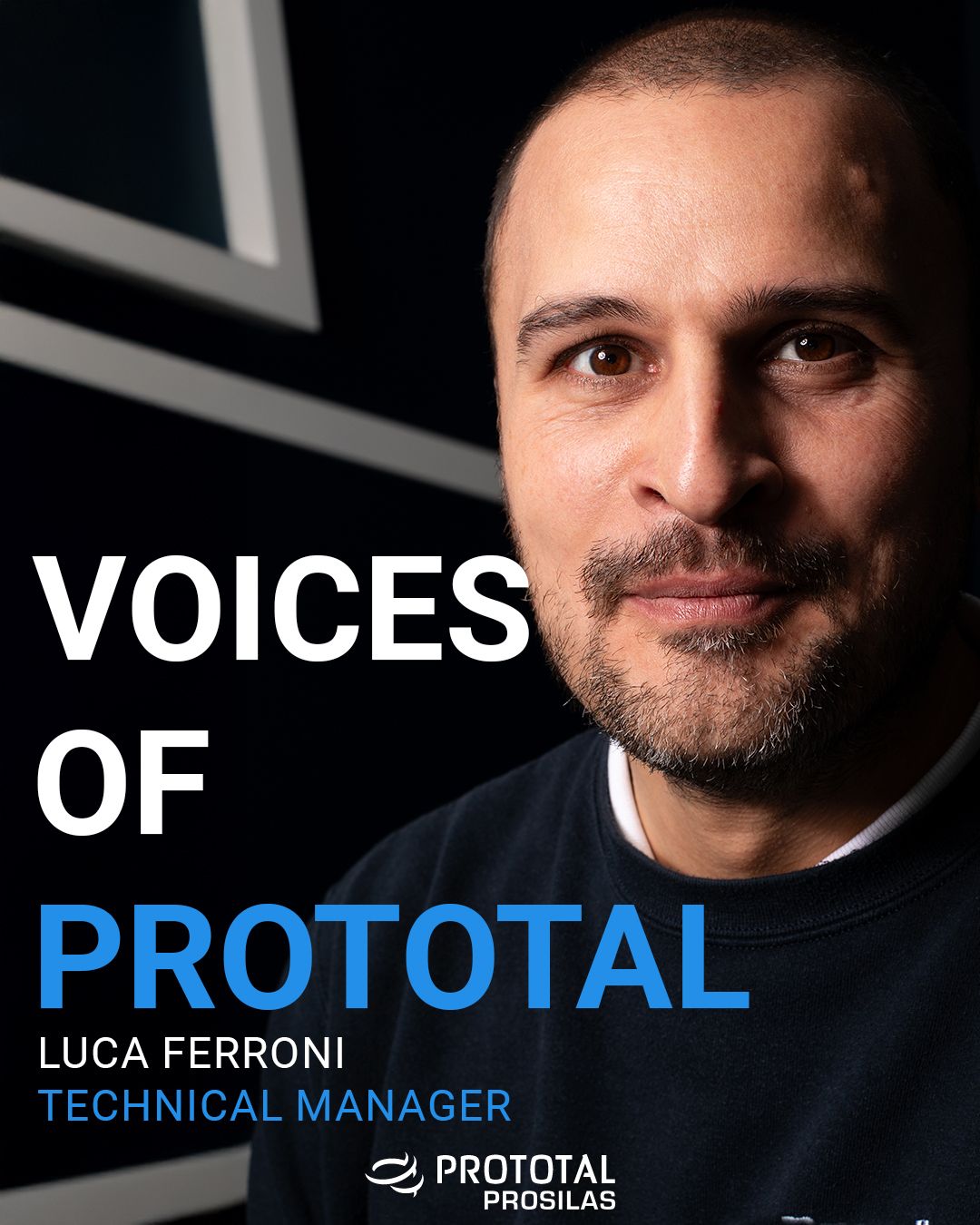
What is your professional background?
“My passion for 3D started almost by chance, but it changed everything. At the age of 19, I attended a course in computer graphics and prototype design for the footwear industry. I never imagined where it would lead me, but during that course, a teacher suggested I try joining Prosilas. In 2003, I began my journey as the company’s first employee. Twenty years have passed since then, and every day I keep discovering how fascinating this job can be.”
What energizes you outside of work?
“Outside of work, I strive to find balance. I spend as much time as possible with my wife, my 9-year-old daughter, and our dog. I love photography, and sharing this passion with my daughter—perhaps during a hike in the mountains—is one of the things that energizes me the most.”
How do you stay motivated, and what is your general work philosophy?
“For me, working well is a matter of passion. It takes commitment to achieve great results, and I firmly believe that true challenges are the best opportunities to grow. I enjoy spreading enthusiasm and motivating my team, even if it’s not always easy. However, when the team moves in the same direction, incredible things happen.”
Pride and challenges
“Over the years, I’ve often faced challenges that seemed impossible: processes considered unfeasible, difficult-to-handle materials, extremely complex productions. And yet, every time, we succeeded. From carbon-filled parts to tracheal stents in PCL, each achievement has been proof of what we can accomplish together. Of course, there have also been tough moments, like during COVID. But in situations like those, trust in decisions and team collaboration truly make a difference.”
“I’m naturally curious, and this job constantly keeps me on my toes. My goal is to keep improving, take on new challenges, and give my best for Prototal. Responsibilities don’t scare me; they motivate me.”
“My advice for anyone starting out? Don’t leave room for superficiality. Studying and diving deep are the keys to growing, in this field as in any other.”
Luca Ferroni – Technical Manager Prototal Prosilas