Tips & Tricks: What are Dimensional Tolerances?
Dimensional Tolerance in SLS 3D Printing: Management and Control by Prosilas
Dimensional Tolerances
3D printing has revolutionized the way products and components are manufactured, offering unprecedented flexibility and customization.
Even in this innovative technology, dimensional precision is a crucial aspect, and Selective Laser Sintering (SLS) stands out for its ability to produce parts with remarkable precision.
Dimensional tolerance refers to the possible deviation within which the printed part can vary from the original geometry.
Specifically, we are talking about +/- 0.3 millimeters for parts up to 100mm and +/- 0.3% for larger dimensions.
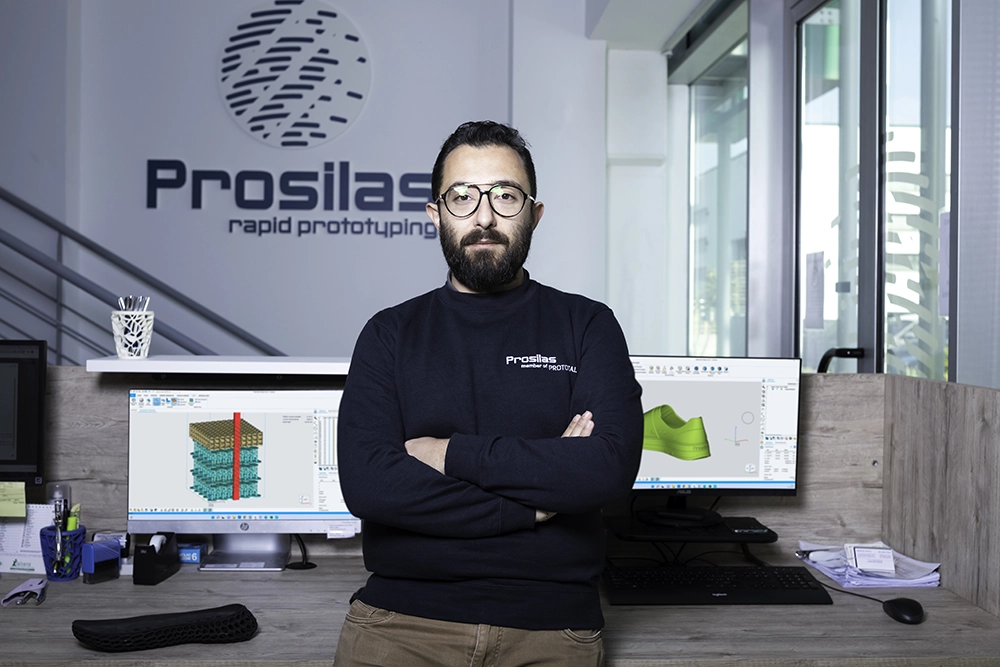

Photo courtesy Protototal Industries
Thermal Expansion
This difference between the nominal dimensions in the 3D file and the printed part is due to thermal expansion, an intrinsic phenomenon in SLS technology.
This printing methodology involves heating the materials to their melting temperature, such as 170°C in the case of polyamide.
During the subsequent cooling process, the part transitions from the melting temperature to room temperature, contracting by approximately 3%.
Our Approach
The parts are initially processed with larger dimensions, using scaling factors specific to each machine and material.
The determination of these factors occurs through the periodic production of samples, a practice that allows monitoring and maintaining control over the dimensional tolerances declared to customers
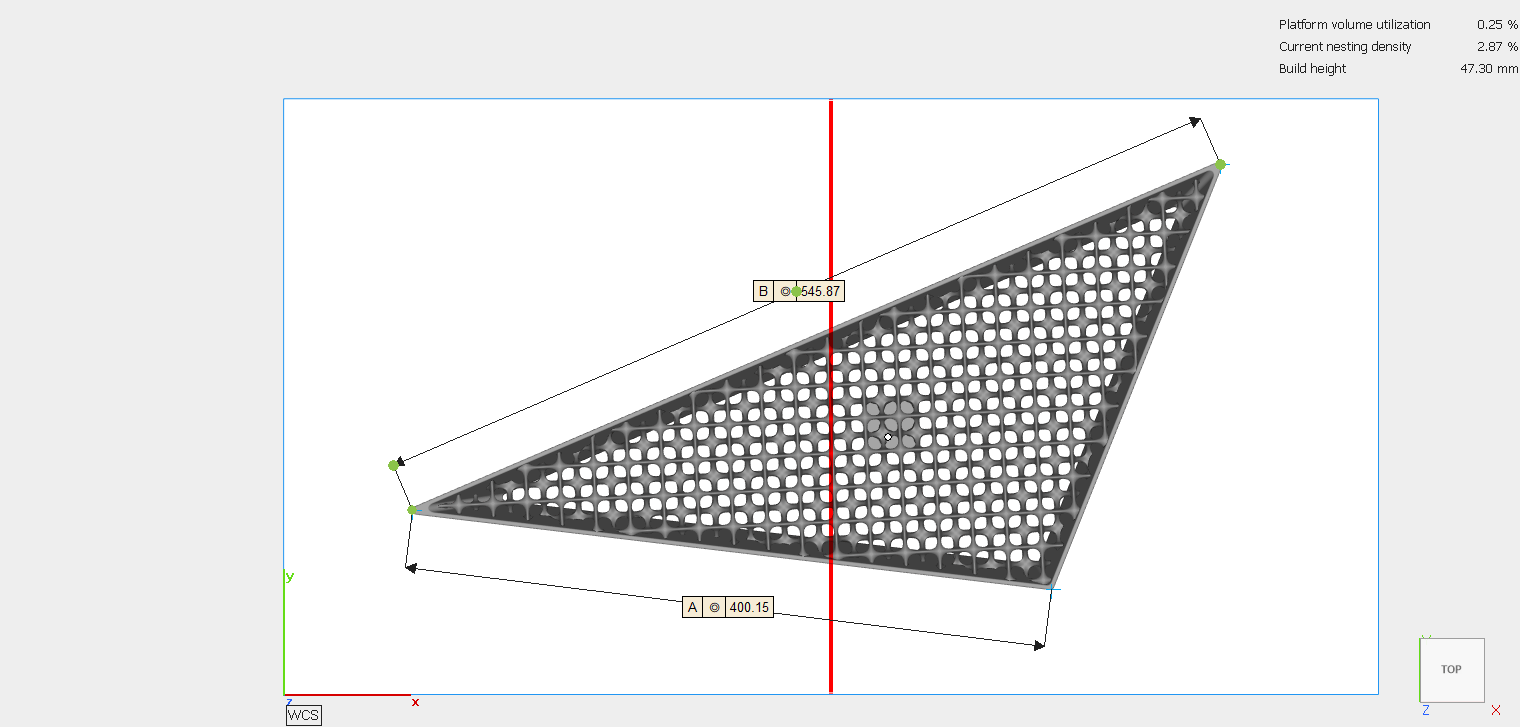
To achieve the highest level of precision, we incorporate this element during the job preparation stage.
Quality Standards
Thermal shrinkage is not entirely constant; hence, an average of the results is calculated and applied. This phenomenon can vary depending on various parameters, such as cooling times, part orientation, shape, and thickness.
To ensure maximum precision, we integrate this aspect during the job preparation phase. Geometries are carefully modified in the software, taking into account the inevitable dimensional variations that occur during material cooling.
This proactive practice demonstrates our commitment to providing 3D-printed components that strictly meet the quality standards required by our customers.
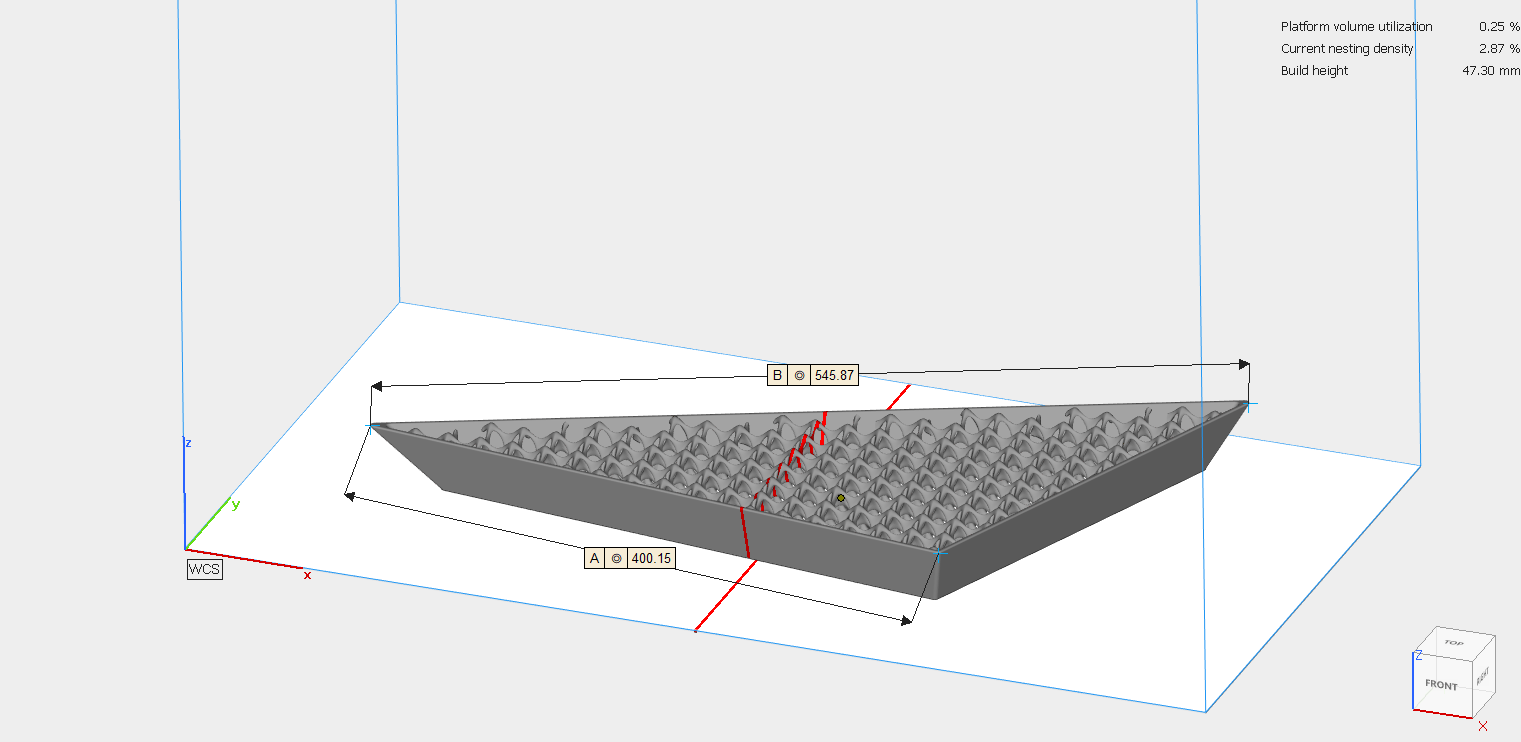
The software undergoes meticulous modifications to the geometries, considering the inevitable dimensional variations occurring as the material cools.