One to ONE MILLION STARTS
The 3D printing sector is experiencing extraordinary growth, with an expected annual rate of 20.8% until 2027. This progress reflects a profound change in production processes: traditional manufacturing, often anchored to consolidated techniques, is having to face increasingly complex challenges. Innovation cycles are getting shorter, while customization demands are constantly increasing.
In this scenario, 3D printing offers a unique opportunity: transforming an initial idea, a prototype, into a product that can be replicated on a large scale, from one to millions of specimens. It is the perfect synthesis of scalability and versatility: starting with a single iteration to refine the design and, once perfection has been achieved, moving on to seamless series production. This ability to adapt makes 3D printing a revolutionary tool in the product development landscape.
With over 750 printing material options available on the market, you can create prototypes and finished products with specific technical characteristics that seemed unattainable just a few years ago. It’s not just about reducing costs or development times, but about redefining every phase of the production process.
A Strategic Planning for Innovation
The implementation of 3D printing in the product development process requires a solid strategic foundation. For companies, planning is not just a question of timing or budget: it is a phase that defines the overall vision of the project. Each product is born from a technical analysis which, like an exploration, probes the boundaries of possibilities.
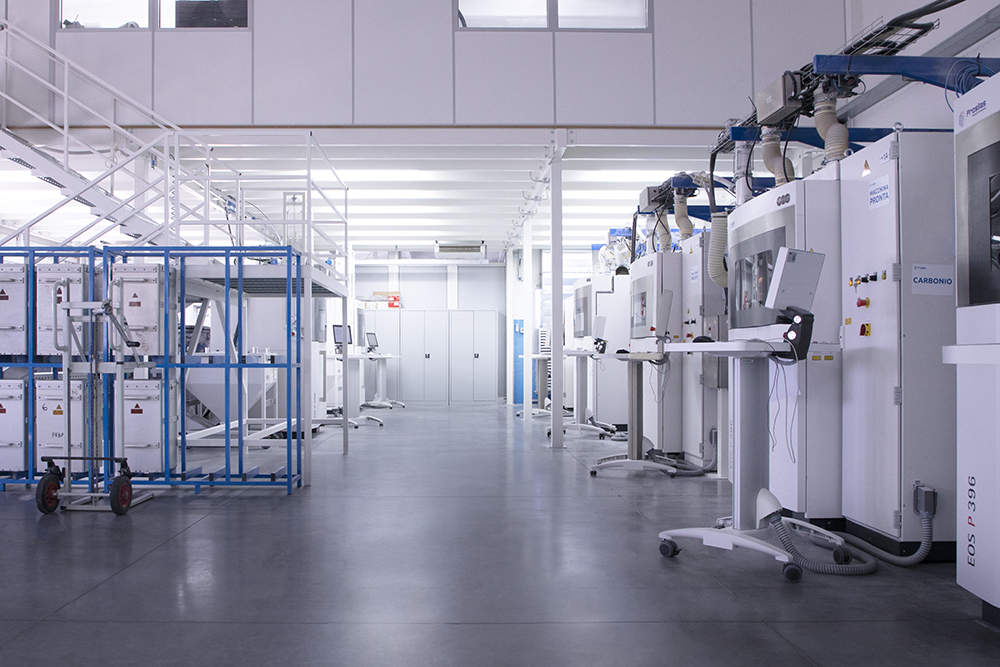
Let’s think, for example, about the complexity of the designs required or the levels of customization desired. Here, 3D printing shines: its versatility allows you to abandon traditional manufacturing restrictions. But there is a cost to consider. We are not just talking about machines and materials, but also about the human resources and skills necessary to embrace a new production paradigm. It’s an investment, sure, but the long-term benefits can far outweigh the initial expenses.
And then there’s time. The development of a complete product takes 22 months on average, but well-structured planning can shorten design cycles. The key phases — initial prototyping, advanced prototyping and production — become stages of a journey where each iteration represents a step towards perfection.
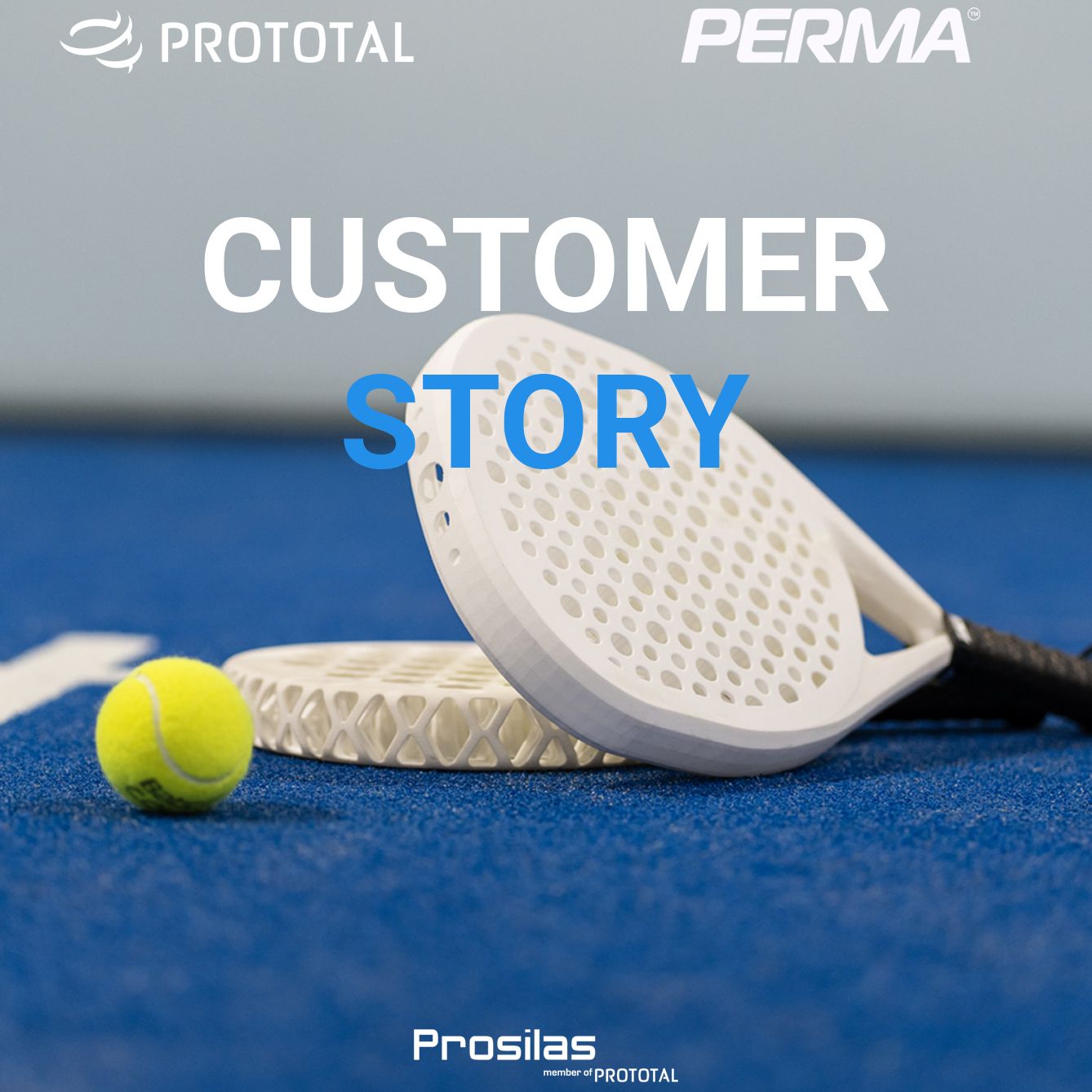
CUSTOMER STORY
An emblematic example is represented by the Perma Padel case, an innovative startup which, with the support of Prosilas and Prototal Damvig, has redesigned the padel racket to make it recyclable and sustainable without compromising its performance.
Thanks to 3D printing, several prototypes were developed in record time, perfecting the design and demonstrating that innovation and sustainability can coexist.
Rapid Prototyping as the Core of Creativity
If there is a time when 3D printing demonstrates its full potential, it is during prototyping. This process is not just a technical step, but the beating heart of innovation. The ability to create, test and refine a design in just hours is a quiet revolution that is transforming the way we conceive new products.
Imagine a creative routine where a CAD model comes to life during the day, then is printed overnight and tested the following morning. This continuous cycle not only accelerates development times, but also fuels a constant dialogue between designers and product, driving rapid and significant improvements.
The prototypes themselves become protagonists. From simple proof-of-concept concepts to aesthetic models that explore ergonomics, up to functional versions that simulate the properties of the final product. Each prototype tells a story, a stage in an evolution towards innovation.
Integrating the New into the Productive Fabric
Incorporating 3D printing into an established manufacturing process is no trivial undertaking. It requires a rethink of infrastructure, a review of skills and, above all, an openness to change. For many companies, it’s like learning a new manufacturing language
This new language brings with it tangible advantages: fewer components to assemble, human errors reduced to a minimum and production times drastically shortened. But the key to successful implementation lies in training. Making staff experts in additive technologies means building a solid foundation on which to innovate
The transition also has its challenges. 3D printing may not be competitive for mass production, but when it comes to customization or limited batches, the benefits become clear. And here technology intertwines with strategy, integrating into business systems and transforming the way we monitor, manage and optimize production.
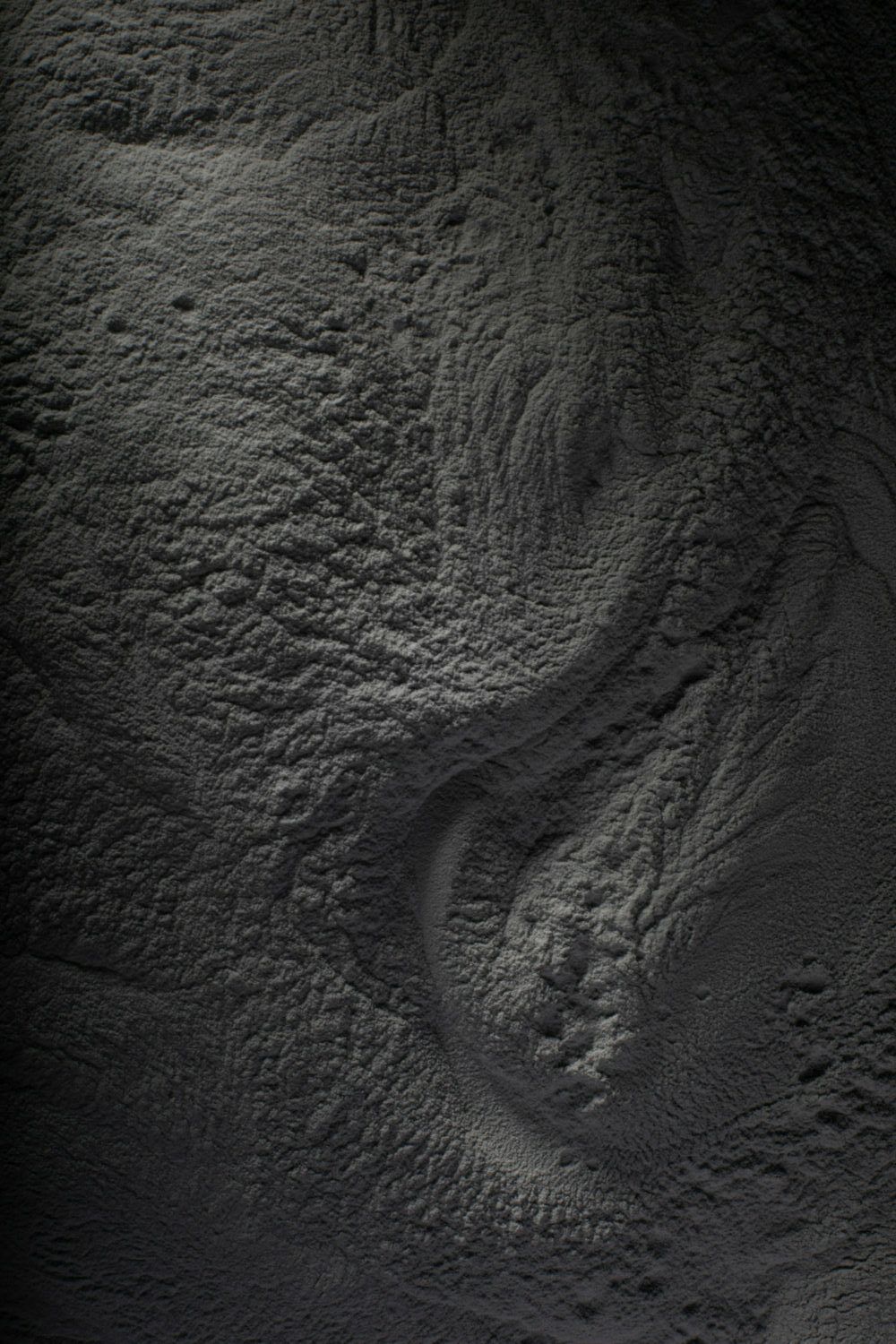
Rethinking the Supply Chain
3D printing is not just a technology, but a transformative force for the entire supply chain. Reducing physical inventories thanks to a digital warehouse, printing specific components on-demand, decentralizing production closer to end customers: all this translates into significant savings and unprecedented responsiveness.
This approach is particularly powerful in spare parts management. Where once huge warehouses were needed to store supplies, today a digital file ready for printing is enough. It is a radical simplification that does not compromise quality, but rather increases operational efficiency.
Choose the right supplier
Prosilas accompanies companies in this transformation, offering an integrated approach that combines advanced technology, quality certifications and specialized skills.
With a fleet of 13 SLS machines, we guarantee constant production capacity, ideal for tackling the challenges of customization and scalable production. Each project is supported by a highly specialized technical team, which offers tailor-made consultancy to optimize production processes and choose the most suitable printing materials.
Quality is at the center of our work: our metrology laboratories carry out rigorous checks to verify that each component meets the highest standards. Every step of the process is taken care of down to the smallest detail, offering companies a path towards modern, success-oriented production.
Furthermore, Prosilas is proud to offer quality, environmental, IATF and TISAX certifications (under certification), ensuring that each solution complies with the highest regulatory and sustainability requirements
Through a balanced approach, which combines technological innovation and compliance with standards, we can not only overcome the challenges of the present, but pave the way for a more agile, personalized and sustainable production future.
If you want to accelerate your projects and turn your ideas into reality, our team is here to support you. With Prosilas, the future has already begun.