Injection Moulding
Injection molding has transformed the manufacturing industry by enabling the production of components across a wide range of polymeric materials. This process supports both simple and highly complex designs, ensuring consistent, high-quality, and predictable results.
At Prototal, we have the capacity to produce millions of components, scaling seamlessly from prototyping to full-scale production. With over 100 automated injection molding machines across our group, we ensure efficiency and precision at every stage.
To optimize logistics and sustainability, we manufacture as close to you as possible, reducing transportation distances while maintaining the highest production standards.
Low volumes and high volumes – we have the capacity!
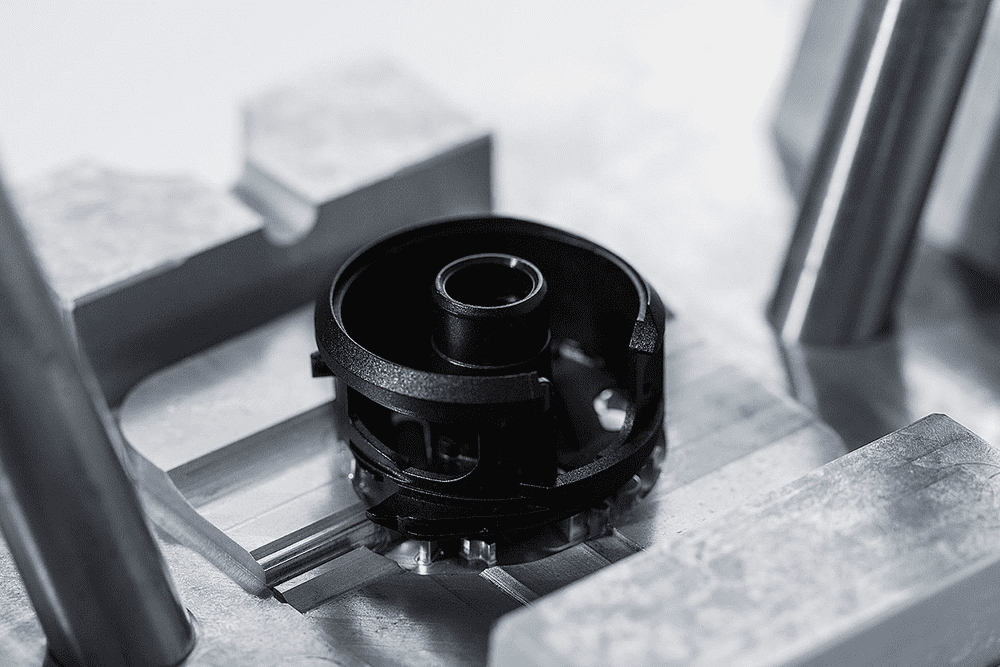
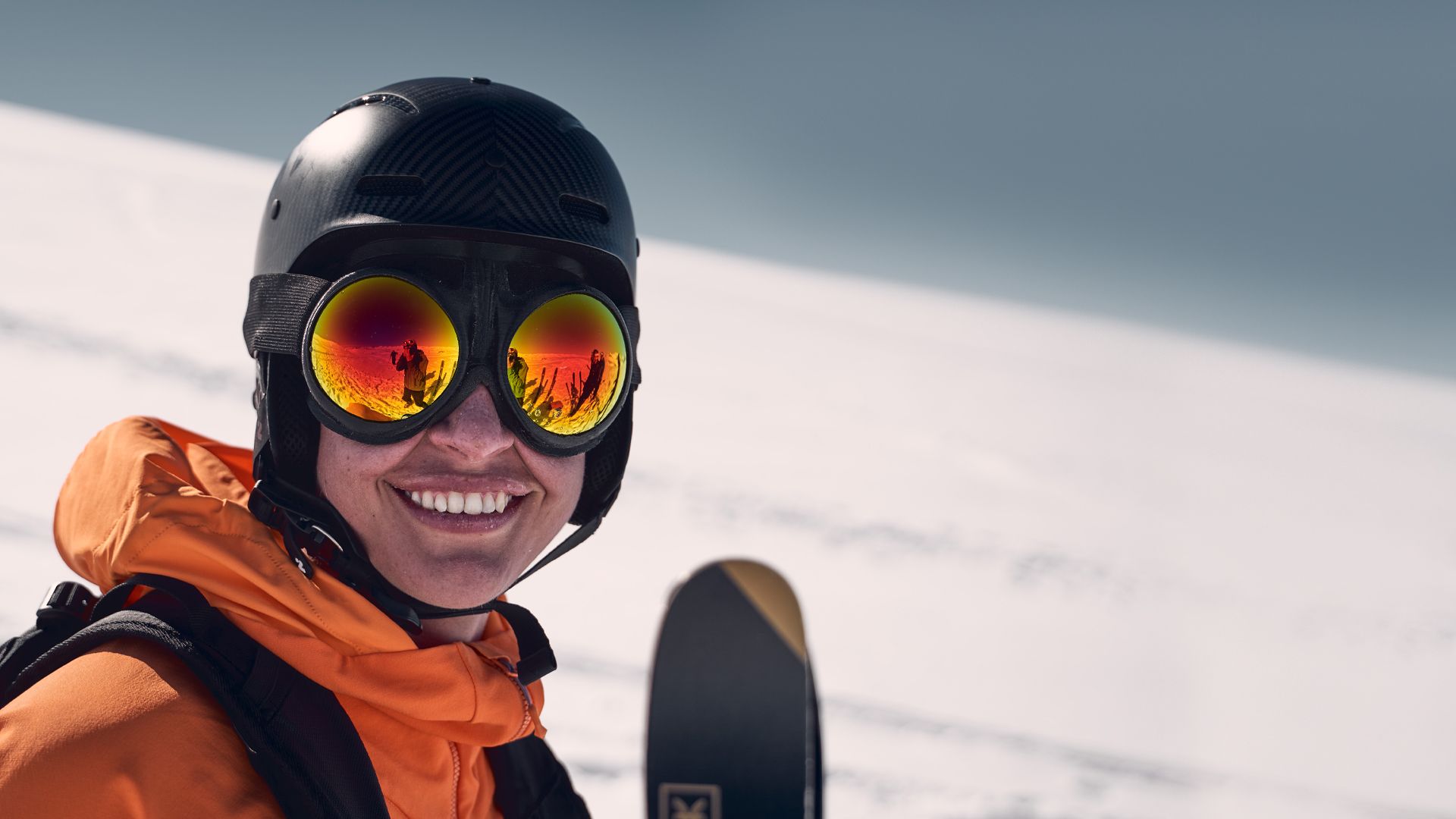
Prototal Prosilas: Superior Quality at Every Step
At Prototal , we specialize in secure and high-quality injection molding services. Before manufacturing begins, we conduct advanced simulations of the injection molding process to identify potential design issues and risks early on. Once the tool is designed, you gain access to trial samples and detailed process protocols.
To ensure consistent quality, we implement rigorous measurement and control procedures throughout the entire production process. Our expertise includes risk analyses, control plans, and PPAP (Production Part Approval Process), ensuring compliance with the highest industry standards.
Within our group, we have access to advanced quality control equipment, including a CMM measuring machine, 3D scanner, and X-ray technology, allowing for precise inspection and verification.
Get in Touch: If you’d like more information or want to discuss your specific project requirements, don’t hesitate to contact us—we’re here to help!
Further Processing & Value-Added Services
🔹 2K Injection Moulding
Depending on the number of components, we determine whether manual overmoulding or true double injection is the optimal choice. One of the most common applications is the creation of soft, ergonomic grip surfaces, improving both usability and design.
🔹 IML – In-Mould Labeling
A decorative label is precisely placed into the mould using robotic automation. During the injection molding process, the label fuses seamlessly with the molded part, creating a durable and high-quality finish.
🔹 Assembly & Sub-Assembly
We provide assembly services, including the integration of threaded inserts and other components. Additional sub-assembly and packaging solutions can be performed before delivery to streamline your production process.
🔹 Printing & Custom Marking
We offer a variety of printing techniques, including:
✔ Pad printing
✔ Digital printing
✔ Heat embossing
Printing can be integrated in-line during production or applied as a post-process for added flexibility.
🔹 Ultrasonic Welding
Factors such as thermoplastic selection, component geometry, and energy director design play a critical role in ensuring a strong and precise weld. A properly executed ultrasonic weld creates a joint stronger than the surrounding material, offering superior durability and performance.
Start a project
The Prosilas Staff will respond promptly by sending a detailed estimate with costs and delivery times.
FAQs
Do you have questions that needs answering? Here you can find the most common questions and answers.
Still got questions? Please do not hesitate to contact us.
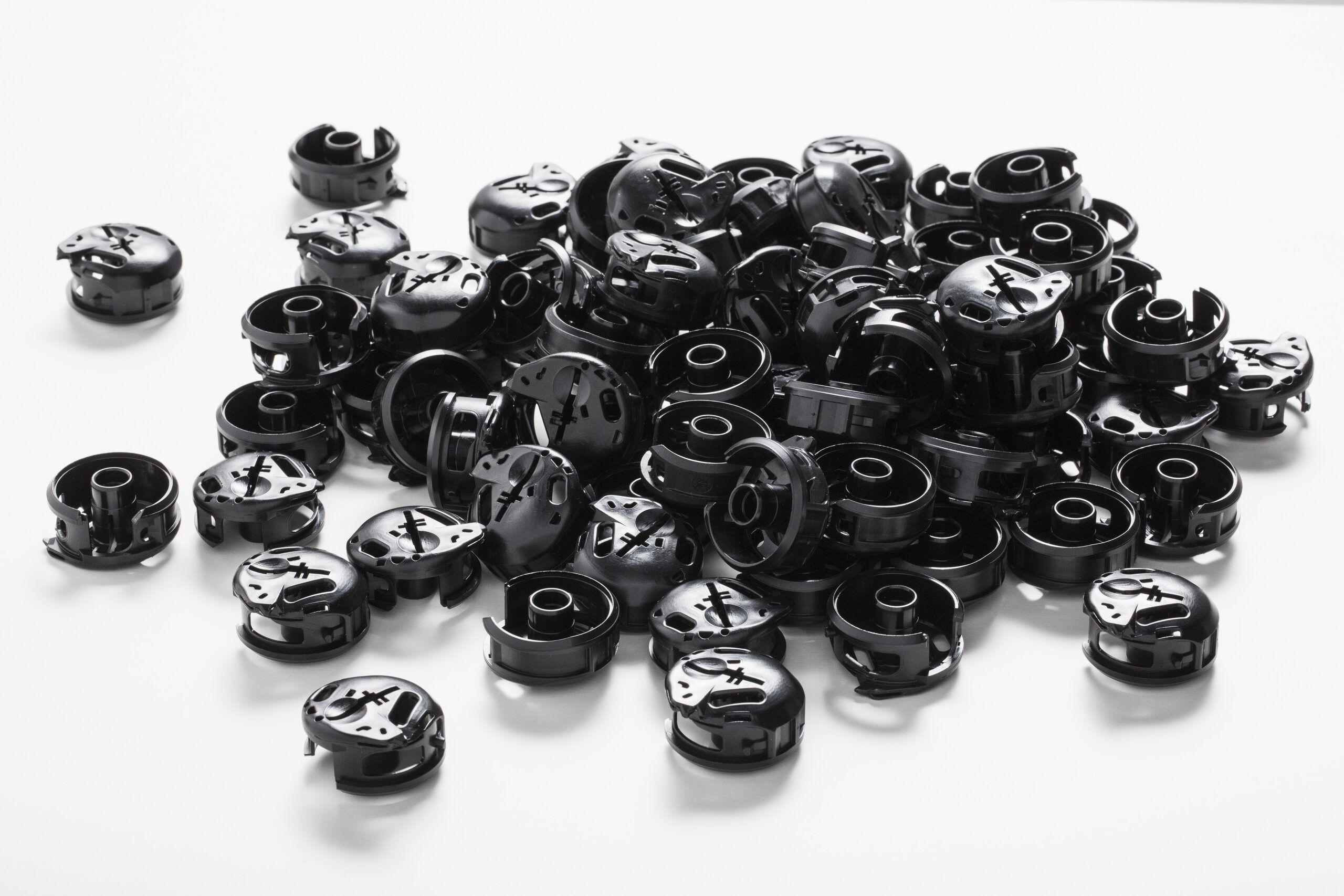
What materials are you able to offer?
At Prototal, we provide a wide range of thermoplastic materials to meet diverse manufacturing needs.
- Extensive Stock of Standard Materials – We maintain a large inventory of commonly used thermoplastics, ensuring fast availability and efficient production.
- Custom Material Sourcing – Need a specific material for your project? We can order unique materials tailored to your requirements.
- Broad Compatibility – We work with virtually all available thermoplastics, offering flexibility for various applications.
- Color Customization – We provide coloring options using masterbatch or compounding to achieve the exact shade you need.
Our material selection ensures optimal performance, durability, and precision for your injection-molded components.
What are the benefits of injection moulding?
Injection molding offers numerous advantages for efficient and high-quality production:
✔ Versatile Material Selection – A wide range of thermoplastics with diverse properties ensures the right material for every application.
✔ Fast Production & Scalability – Short cycle times allow for the rapid manufacturing of large volumes, making it ideal for mass production.
✔ High Process Repeatability – Consistent quality and precision across all components, ensuring reliability and minimal variation.
Injection molding is the go-to solution for cost-effective, high-precision, and scalable manufacturing.
Do you have any further processing options?
Yes! At Prototal, we offer a variety of post-processing solutions to enhance the functionality, aesthetics, and assembly of your injection-molded components.
- 2K Injection Molding
Depending on the number of components, we determine whether manual overmolding or true double injection is the best solution. This method is commonly used for soft, ergonomic grip surfaces, enhancing usability and comfort. - IML – In-Mold Labeling
A decorative label is precisely placed into the mold using robotic automation. During injection molding, the label fuses seamlessly with the molded part, creating a durable, high-quality finish with integrated branding or design elements. - Assembly & Sub-Assembly
We provide assembly services, including the integration of threaded inserts and other components. Additionally, we handle sub-assemblies and packaging, ensuring your products are ready for delivery. - Printing & Marking
We offer a range of printing techniques to customize your components, including:
✔ Pad printing
✔ Digital printing
✔ Heat embossing
Printing can be performed in-line during production or applied as a post-process for greater flexibility. - Ultrasonic Welding
For strong and seamless joints, we provide ultrasonic welding, ensuring:
✔ High-strength bonds, often stronger than the surrounding material.
✔ Optimized weld quality based on thermoplastic selection, component geometry, and energy director design.
Can I Have My Logo Printed on the Product?
Yes! You can customize your product with your logo using various printing methods or by incorporating it directly into the component’s geometry.
Printing Options:
- Pad Printing – Ideal for curved or irregular surfaces.
- Digital Printing – High-quality, full-color prints.
Alternatively, your logo can be integrated into the mold design, making it a permanent part of the component’s structure.
What is Pad Printing (Tampoprinting)?
Pad printing, also known as tampoprinting, is a versatile and precise printing method used to apply designs, logos, or text onto plastic components and other materials.
Key Advantages:
✔ Flexible color options – Allows for a wide range of colors and designs.
✔ Suitable for complex surfaces – Works well on curved, textured, or irregular shapes.
✔ In-line or post-processing – Printing can be integrated into the production line or applied as a secondary finishing step.
How Does It Work?
Using a stencil (cliché) and a silicone pad, the ink is transferred from the etched design onto the component, ensuring sharp, durable prints with excellent adhesion.
How Does Injection Molding Work?
Injection molding is a highly efficient and repeatable manufacturing process that transforms plastic pellets into finished products.
The Process Step by Step:
- Material Preparation – Plastic pellets are fed into the injection molding machine.
- Melting – The pellets are heated until they reach their melting point, turning into a molten polymer.
- Injection – The molten plastic is injected under high pressure into a precisely designed mold cavity.
- Cooling & Solidification – The plastic cools inside the mold, taking its final shape as it solidifies.
- Ejection – Once fully set, the finished component is ejected from the mold, ready for further processing or assembly.
This process ensures high accuracy, consistency, and scalability, making it ideal for everything from prototypes to large-scale production runs.
Guidelines for Injection Molding
To ensure high-quality and efficient injection molding, several key factors must be considered:
- Material Selection
The chosen material affects shrinkage compensation, which must be accounted for in the tool design.
Different materials impact the dimensional accuracy of the final component. - Component Design
The design of the component plays a crucial role in maintaining dimensional accuracy and minimizing defects.
Features such as wall thickness, ribs, and undercuts can influence warping, sink marks, and overall part stability. - Early Project Involvement
Engaging us early in the project allows for design optimization, ensuring that the component is suitable for quality-assured manufacturing.
We provide expert feedback to enhance production efficiency and minimize costly adjustments. - Production Volume & Tooling Strategy
The number of components to be produced determines the most suitable tooling solution:- Prototypes – Quick turnaround with cost-effective aluminum tools.
- Low Volumes – Balancing efficiency and cost.
- High Volumes – Durable steel tools for long production runs.
By considering these guidelines early in the design phase, we help optimize the manufacturing process, reducing costs and ensuring superior product quality.