Prosilas and DUEPì join forces to revolutionize the production of silicone components.
The present article outlines a successful case study arising from the collaboration between Prosilas, a leading 3D printing company, and DUEPì Automazioni Srl, a company specializing in the design and manufacturing of industrial automation.
The shared objective? Harnessing the capabilities of 3D printing in PA2200 to create molds in short timeframes and at affordable costs, revolutionizing the production process of silicone components.
Silicone Components through 3D Printed Molds
The two companies collaborated on the production of molds in PA2200 using Selective Laser Sintering (SLS) technology.
The choice of PA2200 as the printing material was based on its excellent mechanical and chemical properties, combined with biocompatibility (certified according to EN ISO 10993-1 and USP/level VI/121°C).
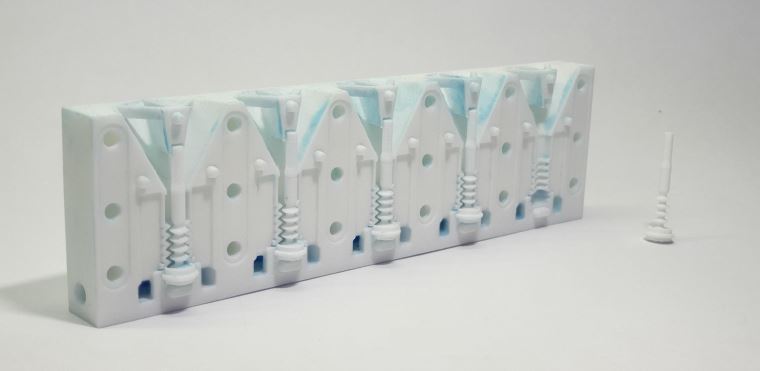
Creation of the PA2200 Mold
DUEPì handled the design of the mold geometries, while Prosilas took care of their 3D printing using SLS technology.
The synergy between the two companies allowed for the optimization of the mold geometries, significantly reducing production times and costs.
Production Technologies
Prosilas’ industrial 3D printers, based on SLS technology, ensure the production of individual parts and batches of ready-to-use products.
Laser sintering on polymeric powders currently stands as the most efficient solution for the production of industrial applications.
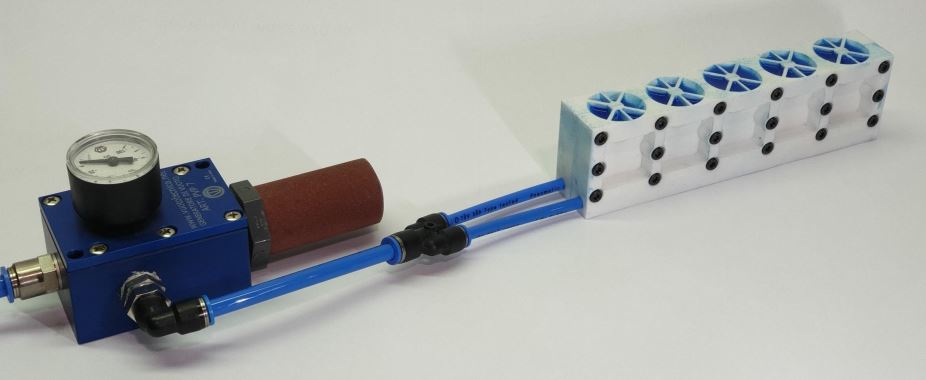
Materials for 3D Printing: PA2200 and Its Exceptional Properties
PA2200, or polyamide 12, stands out as an excellent choice among 3D printing materials. Its characteristics make it a versatile and high-performance material, suitable for a wide range of applications.
- A resilient and versatile material
PA2200 boasts high mechanical and chemical resistance, making it ideal for the production of robust components resistant to impacts, wear, and tension. Its rigidity and toughness make it suitable for bearing heavy loads and for use in various industrial environments.
- Biocompatibility and safety
The biocompatibility of PA2200, certified according to EN ISO 10993-1 and USP/level VI/121°C regulations, makes it safe for contact with the human body. This makes it an ideal material for the production of medical and food components, where safety and hygiene are fundamental requirements.
- Flexibility and printing performance
The versatility of PA2200 extends to 3D printing. The material can be used for printing complex and intricate geometries, offering high resolution and a premium surface finish. The ability to print in a variety of colors further expands creative and applicative possibilities.
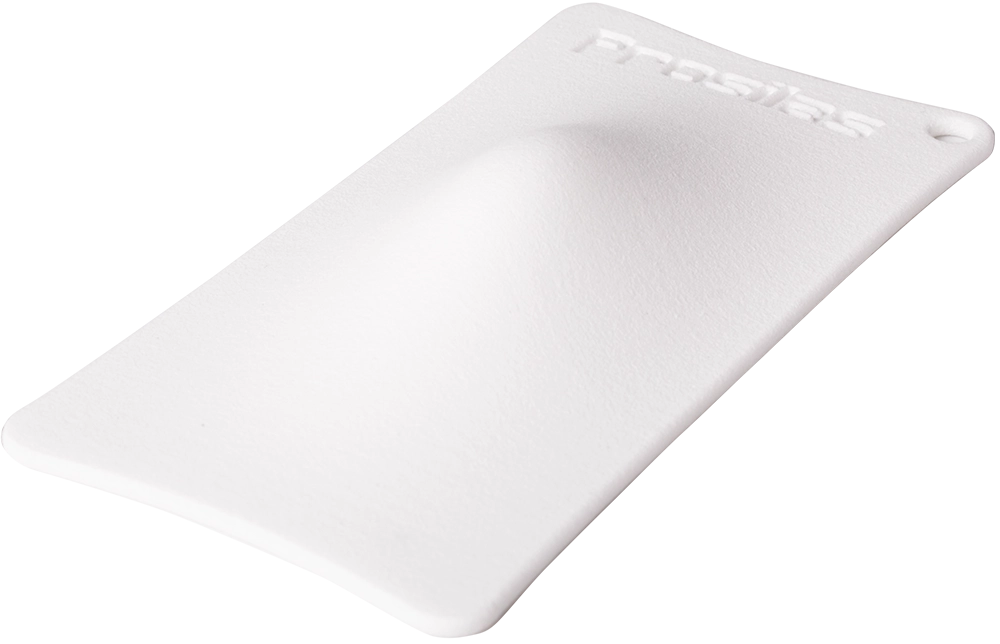
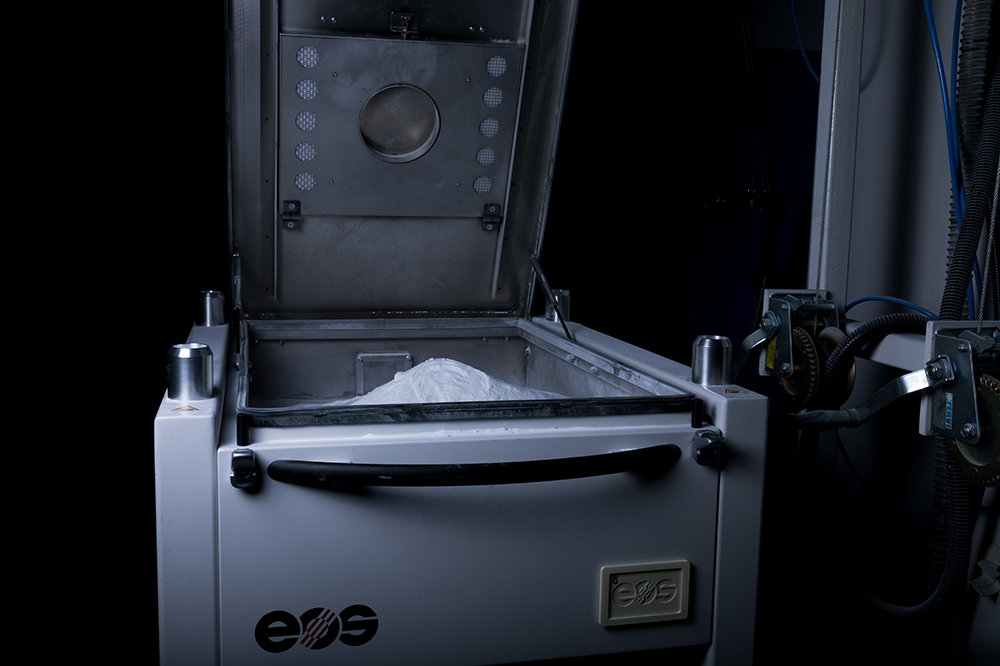
Advantages for Mold Production
3D printing of molds in PA2200 offers a series of significant advantages compared to traditional technologies. Firstly, it allows for a drastic reduction in production costs, up to -180% compared to CNC machining or vacuum casting. This is achieved through the optimization of mold geometries and the reduction of material waste.
Secondly, 3D printing enables the production of molds in significantly shorter timeframes compared to traditional technologies. The speed of production allows for the creation of prototypes and finished products in a short time, ensuring greater flexibility and responsiveness to market needs.
Design flexibility and sustainability
3D printing in PA2200 provides extensive design freedom, allowing for the creation of complex and customized geometries. This results in molds optimized for specific applications, with the possibility of integrating various functionalities into a single mold.
Furthermore, 3D printing in PA2200 aligns with sustainability goals, thanks to the reduction of material waste and the production of lightweight and durable components.