The vacuum casting process offers several benefits over other manufacturing processes. Firstly, it is a relatively cost-effective method, especially for small to medium-sized production runs. Secondly, it can produce high-quality parts with exceptional surface finishes and intricate details. Finally, it has a quick turnaround time, making it ideal for rapid prototyping and small production runs.
Vacuum casting and 3D printing are often utilized together to produce high-quality parts quickly and cost-effectively. 3D printing is employed to create a master model, which is then utilized to make a silicone mold for vacuum casting. This method allows for multiple parts to be produced from a single master model, making it an efficient process for small production runs.
Vacuum casting is a highly effective manufacturing process that has been utilized for decades to produce superior quality parts across various applications. Over recent years, vacuum casting has become increasingly prevalent in conjunction with 3D printing technology. In this article, we will explore the relationship between vacuum casting and 3D printing, their respective advantages and disadvantages, and how manufacturers can choose the best method for their specific needs and applications.
What is vacuum casting ?
Vacuum casting is a process that involves creating a silicone mold from a master model and subsequently pouring resin into the mold. This is achieved by pouring silicone over the master model and allowing it to cure. The silicone mold, once cured, is used to create a cavity into which the resin is poured. The mold is then placed under vacuum to eliminate any air bubbles. After curing, the final part is removed from the mold.
The creation of the mold
To create a mold for vacuum casting, the first step is to produce a master model of the desired part. This can be achieved through various methods, including 3D printing ( SLA is preferrred fot its high detailed surface), CNC machining, or even hand sculpting. The master model should be as accurate and detailed as possible, as it will be used to create the final mold and subsequent parts.
Once the master model is ready, a silicone rubber material is poured over it. The silicone rubber is chosen for its flexibility and ability to reproduce fine details. The silicone is typically mixed with a catalyst to initiate the curing process, and then poured over the master model in a vacuum chamber to remove any air bubbles.
After the silicone has cured and solidified, the mold is removed from the master model. The mold is then prepared for casting by adding sprues, vents, and other necessary features to enable the urethane resin to flow through the mold and create the desired part.
Once the mold is ready, the resin is poured into the mold under vacuum to remove any remaining air bubbles. The mold is then left to cure, and the final part is removed from the mold once the curing process is complete.
It is worth noting that the mold can be reused multiple times to create identical parts. However, over time, the mold may become worn or damaged, and eventually require replacement.
Overall, the creation of the mold is a crucial step in the vacuum casting process, as it directly impacts the quality and accuracy of the final part. By carefully preparing the mold and removing any air bubbles, manufacturers can produce high-quality, detailed parts that are suitable for a wide range of applications.
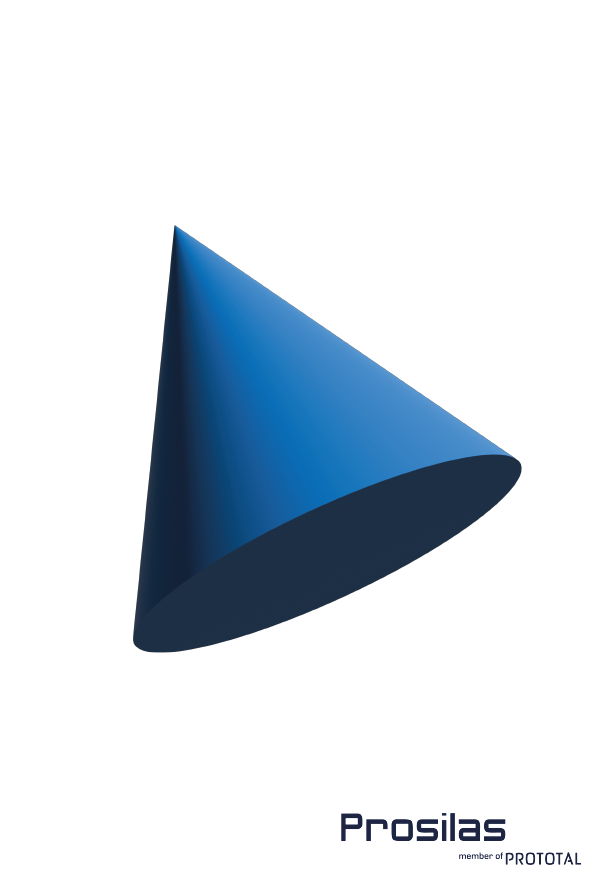

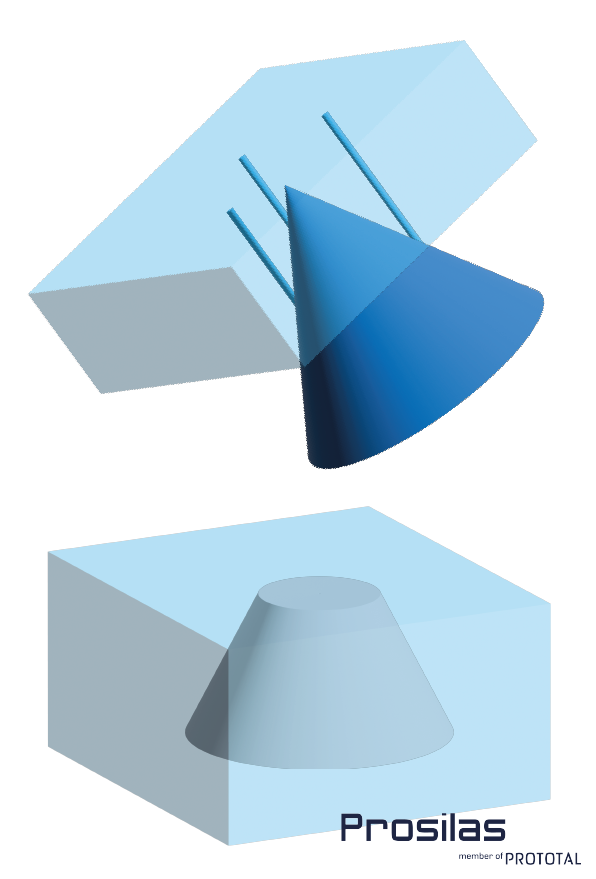
Vacuum casting materials
Polyurethane resins are chosen for their ability to replicate the fine details of the mold and for their strength and durability. Moreover those materials can simulate various mechanical properties and produce parts with properties close to polymers such as ABS, PC, PP.
There are many types of polyurethane resins available, each with their own properties and characteristics. Some common factors to consider when selecting a resin include:
- Shore hardness: This refers to the material’s resistance to indentation and is measured on the Shore hardness scale. A higher number indicates a harder material.
- Color: Polyurethane resins can be clear, white, black, or a range of other colors. The color of the resin used will depend on the desired appearance of the final part.
- Flexibility: Some resins are more flexible than others, which can be useful for parts that will be subject to bending or other forms of deformation.
- Temperature resistance: Some resins are designed to withstand high temperatures, making them suitable for use in applications where the part will be exposed to heat.
The specific polyurethane resin chosen for a project will depend on the requirements of the part being produced. For example, if the part needs to be highly detailed and have a smooth surface finish, a low viscosity resin may be used. If the part needs to be highly durable and resistant to impact, a higher Shore hardness resin may be chosen.
It’s worth noting that some polyurethane resins can also be tinted or painted after casting to achieve a specific color or finish.
Overall, the selection of the appropriate polyurethane resin is an important consideration in the vacuum casting process, as it directly impacts the properties and appearance of the final part. By carefully choosing the resin based on the specific requirements of the part, manufacturers can produce high-quality parts that meet the needs of their customers.
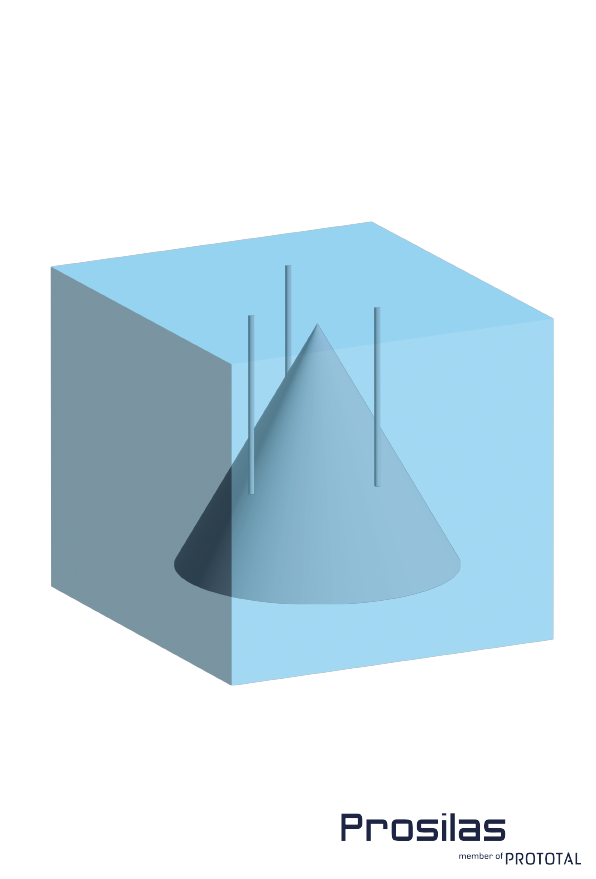
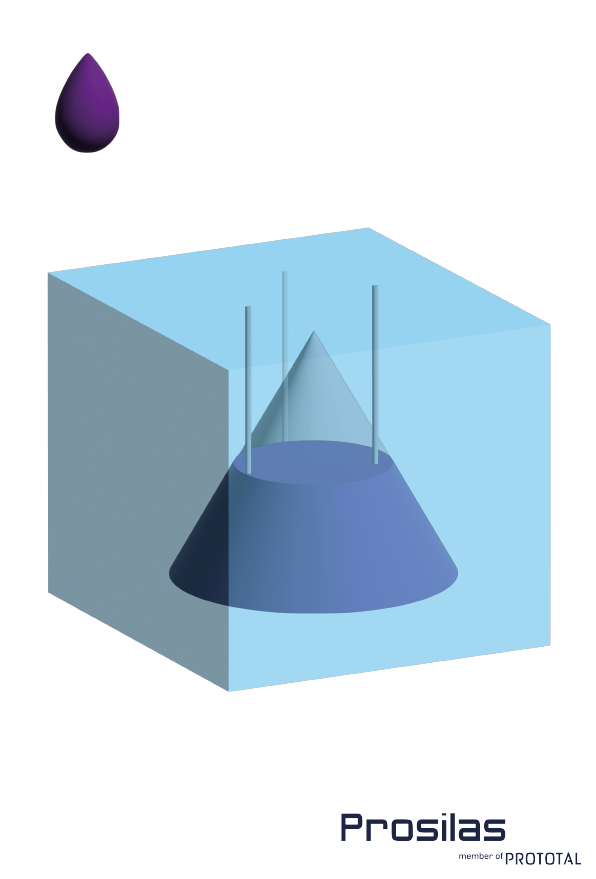
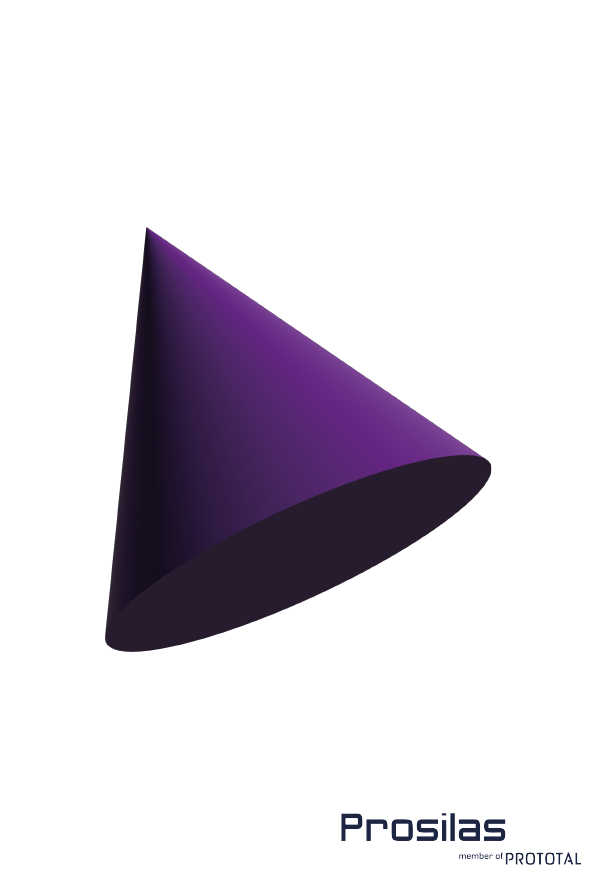
Vacuum casting & 3D print
While vacuum casting has many advantages, 3D printing also offers unique benefits. Firstly, it allows for greater design flexibility and the ability to create complex geometries that would be challenging or impossible with other manufacturing processes. Secondly, it offers customization and personalization of parts, making it ideal for one-off and small-batch production runs. Finally, it has a rapid production speed, with parts often produced within hours or days, making it ideal for rapid prototyping.
Choosing between vacuum casting and 3D printing depends on the specific application and requirements of the part being produced. Vacuum casting may be more cost-effective and efficient for small to medium-sized production runs, especially when 3D printing is utilized to create the master model. However, for one-off or highly customized parts, 3D printing may be the better option.
In conclusion, vacuum casting and 3D printing are both valuable manufacturing processes that offer unique advantages. Manufacturers can select the most suitable process for their specific needs and applications by comprehending the strengths and weaknesses of each method.
Advantages of Vacuum Casting
Vacuum casting has several advantages over other manufacturing processes, including:
- Cost-effective: Vacuum casting is a relatively low-cost manufacturing process, especially for small to medium-sized production runs.
- High-quality parts: Vacuum casting can produce high-quality parts with excellent surface finishes and intricate details.
- Quick turnaround: Vacuum casting can produce parts in a matter of days, making it an ideal process for rapid prototyping and small production runs.
The Relationship between Vacuum Casting and 3D Printing
Vacuum casting and 3D printing are often used together to produce high-quality parts quickly and cost-effectively. 3D printing can be used to create a master model, which is then used to make a silicone mold for vacuum casting. This allows for the production of multiple parts from a single master model, making it an efficient process for small production runs.
Advantages of 3D Printing
While vacuum casting has many advantages, 3D printing also has its own unique benefits, including:
- Design flexibility: 3D printing allows for greater design flexibility and the ability to create complex geometries that would be difficult or impossible with other manufacturing processes.
- Customization: 3D printing allows for customization and personalization of parts, making it an ideal process for one-off and small-batch production runs.
- Speed: 3D printing can produce parts quickly, often within a matter of hours or days, making it an ideal process for rapid prototyping.
Which is More Convenient?
The choice between vacuum casting and 3D printing depends on the specific application and requirements of the part being produced. For small to medium-sized production runs, vacuum casting may be more cost-effective and efficient, especially when using 3D printing to create the master model. However, for one-off or highly customized parts, 3D printing may be the better option.
The Prototal Group and its capabilities
Prosilas, a part of the Prototal Group, has extensive experience in 3D printing and the latest technologies in-house. With a wide range of machines for vacuum casting, they have become a reliable partner in manufacturing.
The Prototal Group has invested heavily in state-of-the-art equipment, making Prosilas an expert in producing high-quality prototypes and end-use parts. Their expertise in additive manufacturing has enabled them to offer customized solutions to their clients, ensuring that they meet all their needs and requirements.
In addition to their 3D printing capabilities, Prosilas can dispose of a vast array of machines for vacuum casting, making it possible for them to produce parts in various materials and quantities. Their extensive knowledge and experience in this area make them a reliable partner for manufacturing projects of any size or complexity.
Overall, the combination of their expertise in 3D printing and vacuum casting, as well as their large number of machines, makes Prosilas and the Prototal Group a reliable and efficient partner in the manufacturing industry.