Post-process treatments
beyond the production
“The customer always has his reasons”, ie specific needs that require an exclusive evaluation and an ad hoc solution. Our commitment to propose ourselves as AM Service and Consulting from Mathematics to Post Process allows us to take into account this aspect, devoting particular attention to this last phase, that is to all those finishing treatments that are performed on the part already produced, in order to optimize functionality and aesthetics.
We deepen together with Marco Soldini, Head of Laboratory and Post Process of Prosilas.
At every result his Post-Process treatment
All parts developed with additive Manifacturing, whether made with polymer or metal, can receive end-of-process treatments for aesthetic and/or functional improvements. The most performing and suitable post process (automatic or manual) is chosen according to the needs and objectives that the final result must reach.
There are almost always two possible paths:
1. Automated Finishing
through a machine that the operator only cares to support
2. Manual Finishing
with an operator who performs the various operations required by the procedure.
The choice is determined by the required precision rate, also depending on the use of the workpiece in question.
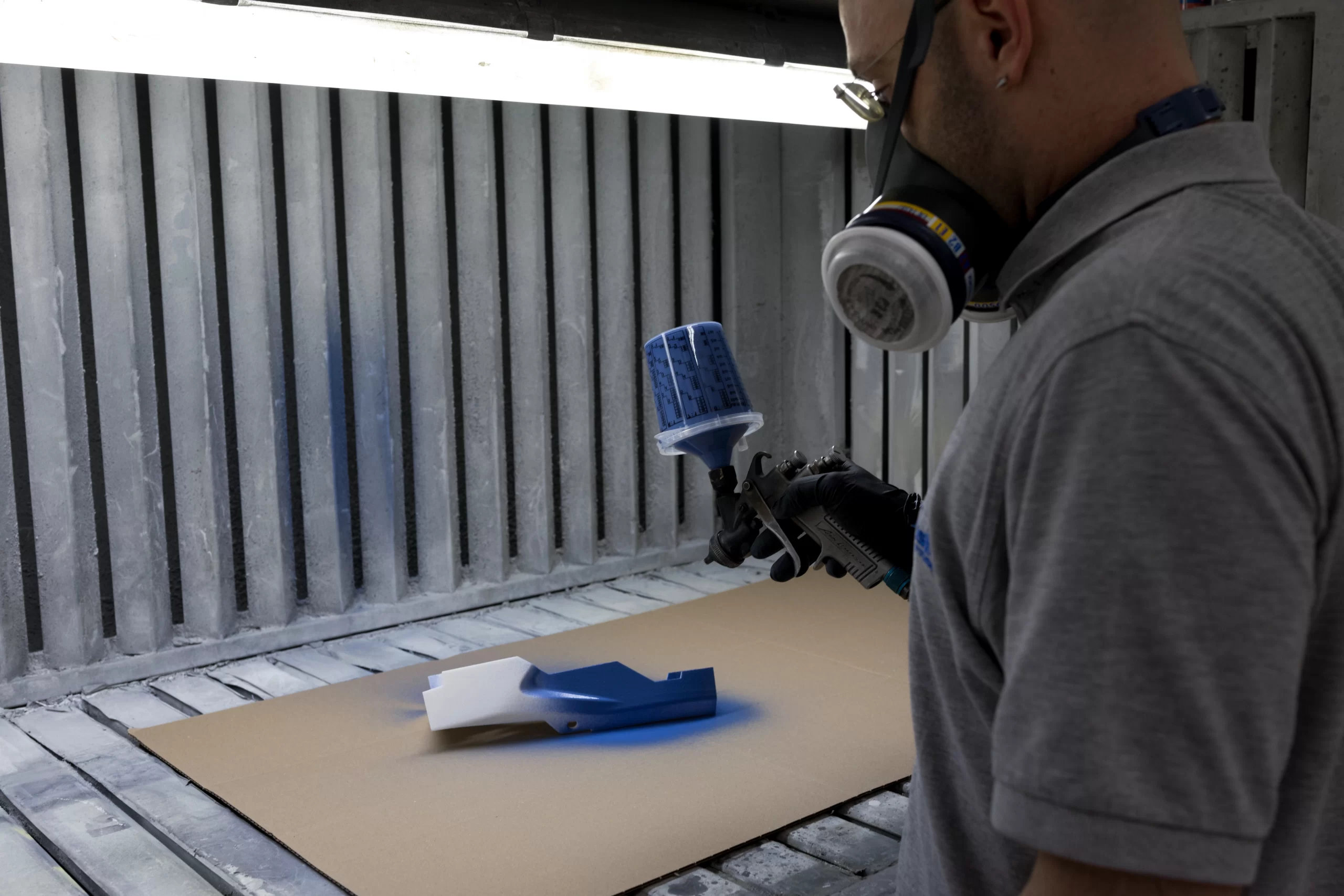
Automated Finishing
In Prosilas the Manual Finishing is the preferred option, even if there are cases in which Automated Finishing is used, such as vapor smoothing and coloring, respectively a chemical steam treatment and an immersion of the part in the color.
VAPOR SMOOTHING
The chemical smoothing is an acid vapor that applied on the piece allows you to smooth the surface, making it, depending on the case, waterproof, washable, shiny, food compatible and not only.
Examples of objects that can be subjected to this type of Post Process? A tank to contain specific liquids, but also dishes and glasses.
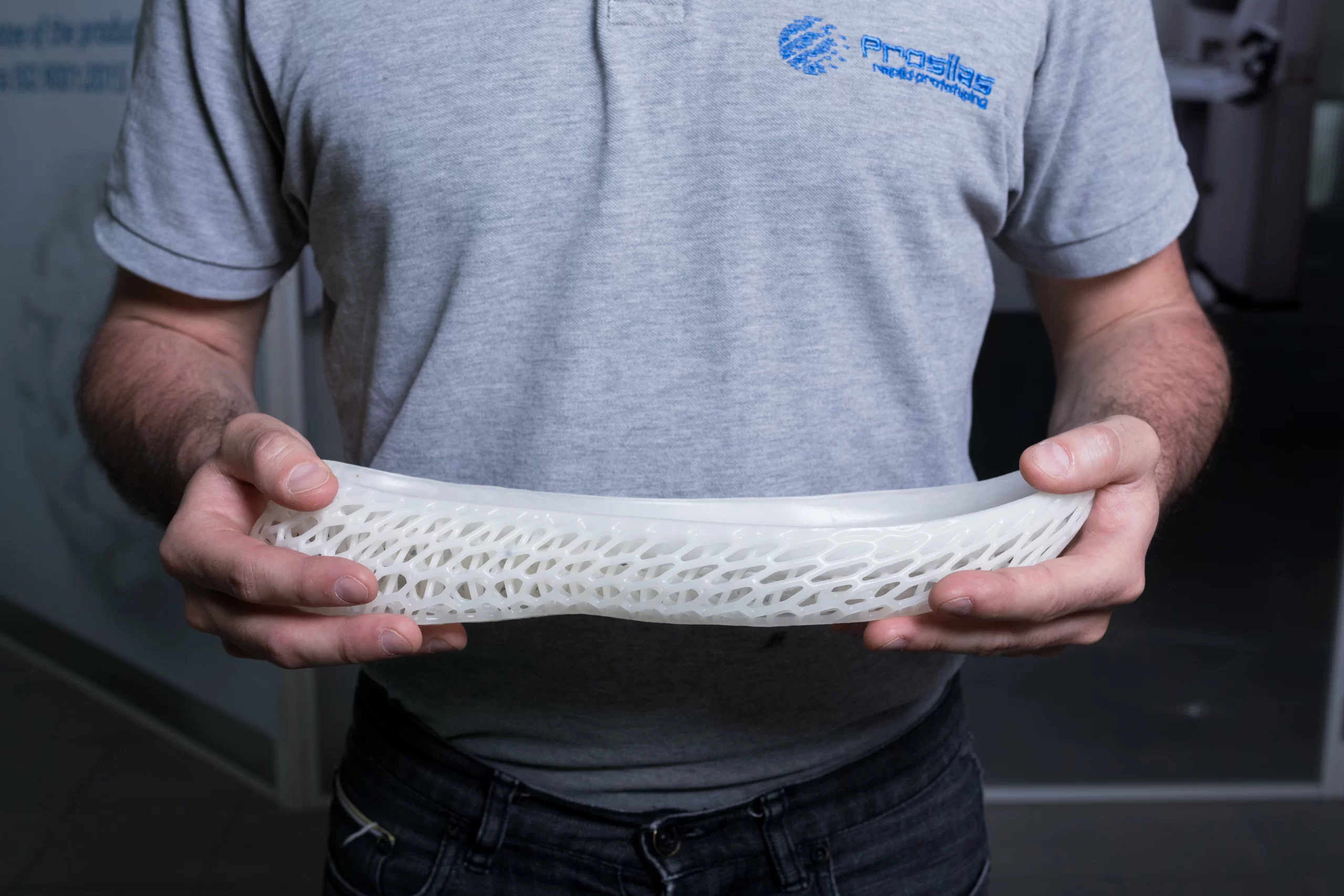
COLORING
With the coloring you go instead to change the color resulting from the construction material (white if polyamide, gray if metallic, for example) by immersing it in a liquid colored preparation that is absorbed, covering any surface imperfections without altering the thickness.
They can be subject to coloring design components such as those for eyewear, which require a uniform color even in the smallest parts, all potentially exposed. Or, they can be parts like pulleys, which have to move inside machinery without leaving residue, which would happen if they were painted.

Seven types of Manual Finishing
Manual Finishing is preferred not only in all cases where the skill of the operator makes the difference, but also when customers have only one piece, absolutely exclusive (something that often happens in rapid prototyping), to apply the post process and it is said that there is an ad hoc machinery.
Seven results that customers usually look for with manual finishes:
-
Waterproofing for liquids and vapors.
Sometimes the process is necessary only on one side of the product. Prosilas determines together with the customer, from time to time, which substance to use and whether to spray or bath, for example. It is different to waterproof a thermos for drinks, the tank of a motorcycle or a part of a hull exposed to salt. It must then consider what type of maintenance or treatment the object will be subjected to, for example if it will have to be disinfected.
-
Metal Insert – Helicoil.
The customer can supply parts with holes and Prosilas must put threaded inserts, embedded in the material, to allow – for example – to insert screws or other metal parts.
-
Metal Plating.
It is the arrangement of metal particles on plastic. It is useful, for example, in the case of restorations in which original spare parts are no longer available, to be created ex novo and then chrome.
-
Fuel Resistant treatment.
It is another type of waterproofing, excluded from the process nº1 for chemical reasons. It’s about the tanks, but also all the parts that could come into contact with the fuel, such as the protective cover of a part of the car near the tank. It is a very complicated process, especially when it comes to storing substances that are difficult to manage, up to those considered aggressive for which only glass works.
-
UV Resistant treatment.
It concerns all those parts that change due to exposure to the sun, white or transparent, which turn yellow, or objects for which the passage of UV rays causes chemical problems.
-
Painting.
When painting a blank piece, the surface is not smooth. Applying a primer, however, is free of imperfections and you can decide whether it is smooth or opaque.
-
Micro shot peening.
It owes its name to the microspheres that form the abrasive dust with which an object is treated by blowing, in an automated machinery. It leaves no residue.
When and where it is useful to employ with post processing
The post process has different uses depending on the purpose of the client.
A prototype of a tank, for example, may be required:
- as a prototype for its own sake, so it does not need a post process;
- for a static demonstration, so need an external painting but not internal;
- for a functional demonstration, so not needing an external finish but certainly a functional finish.
A single piece can therefore be used for very different uses, so the finishes that a process partner like Prosilas can recommend will be just as different.
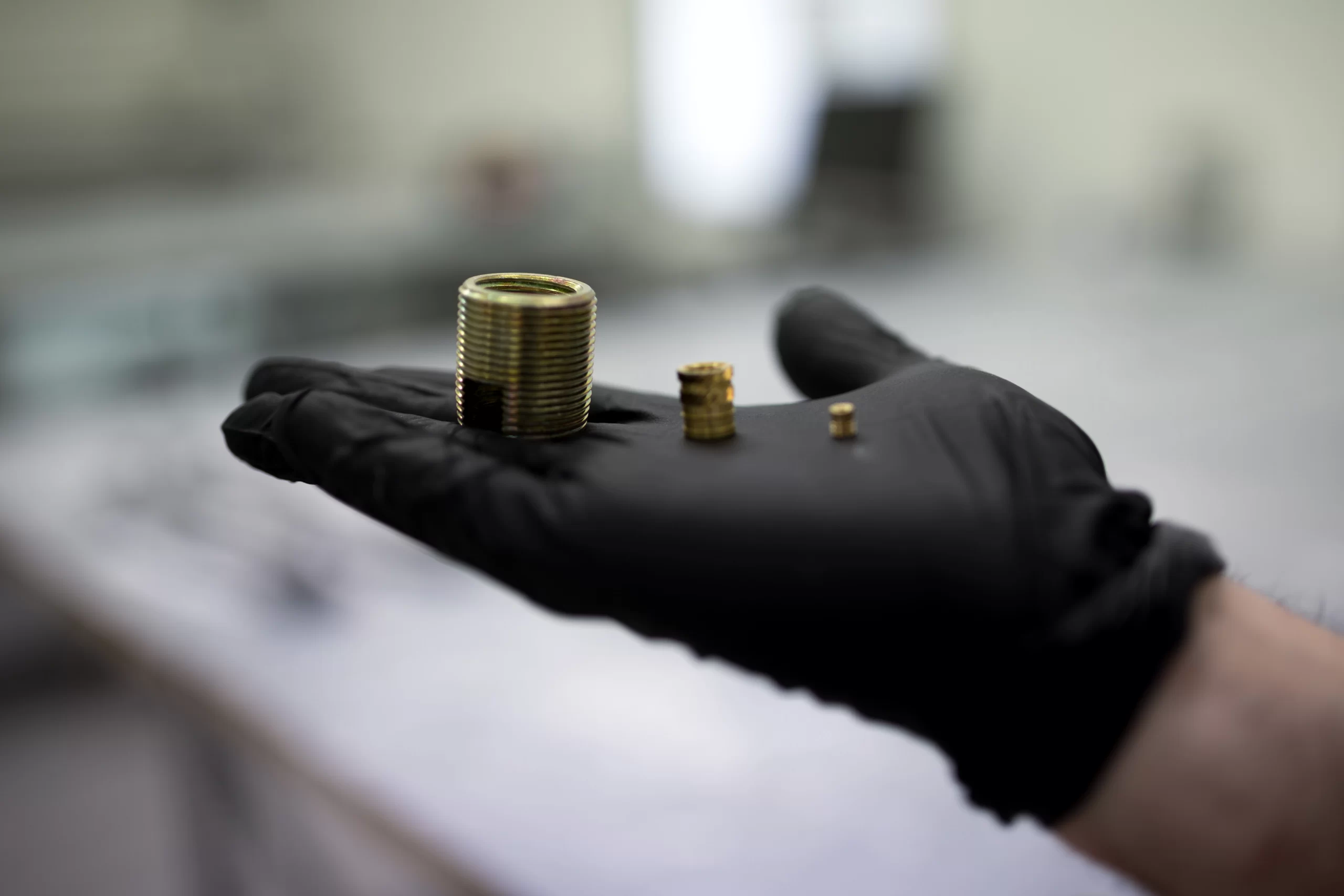

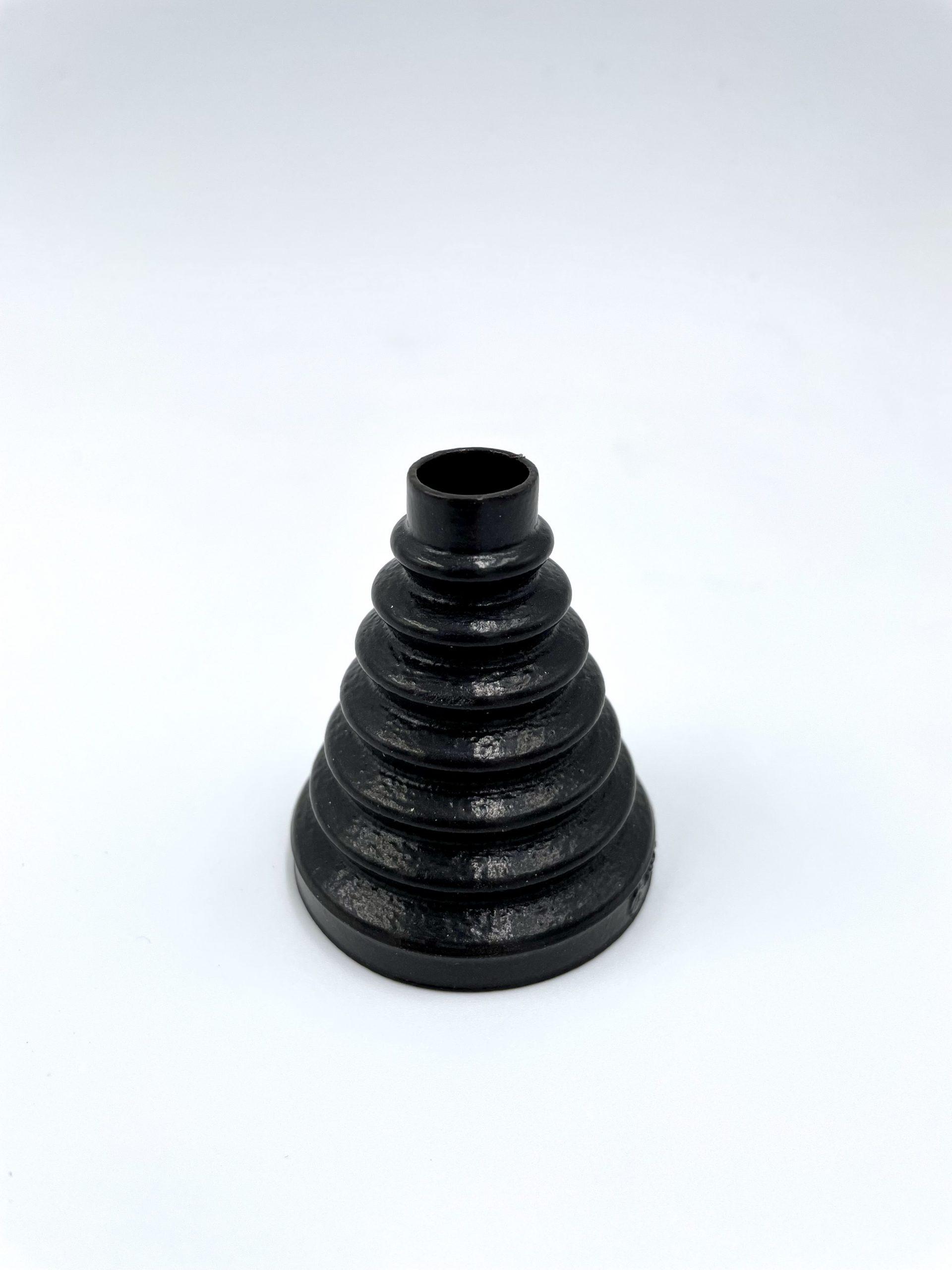
The smaller and more delicate the object, the less likely it will be finished in a machine. However, the automated process guarantees a more homogeneous result. Sometimes the post process modalities can be interchangeable: choosing the best one in a given case is part of the competence of the AM consulting service.
The most requested post processing systems
Based on our experience, there is a large demand for the primer ready for painting, which then intervenes the customer’s paint, and waterproofing, including food, especially in terms of FPA certifications and biocompatible materials.
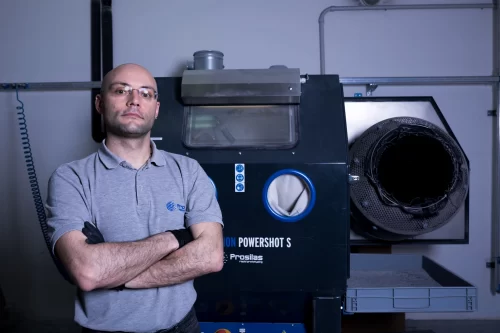
MARCO SOLDINI
Plant Manager
Marco Soldini is member of TAB – Prototal Group Technical Advisory Board
Soldini’s professional figure is fully employed in the Company: he is R&D Finishing Manager and in charge of special projects: he researches and develops new techniques and new solutions so that the Company always has a cutting-edge offer.
Plus, he’s IT & Plant Manager at Prosilas.