3D Production: Principles, Rules, and Technologies
Industrial 3D printing has evolved from rapid prototyping to mass production, offering significant advantages to companies: reduced production times and costs, improved product quality, and customization possibilities.
This technology enables the creation of complex components in a single phase, simplifying assembly and allowing greater flexibility in responding to market needs.
Workflow
At the core of conceiving productions through additive manufacturing technologies, fundamental aspects remain tied to the employed technologies, materials used, and the skills of designers and operators.
The intricate workflow characterizing a typical production with industrial 3D printers involves delicate phases that can be challenging to manage for less structured companies or those lacking experience and know-how.
A production process using additive manufacturing technologies can be achieved only through some fundamental stages:
- Design and optimization/lightweighting of geometries based on technologies and materials.
- Nesting and optimization of production parameters.
- Utilization of facilities and technologies with high production capacity.
- Application of post-processing technologies (aesthetic and functional).
- Quality analysis and repeatability.
- Certification of processes and materials.
Design for Additive Manufacturing
Design for Additive, or Design for 3D Printing (DFAM), represents an innovative approach in the design of components and products.
New possibilities emerge in the field of design, enabling the creation of complex shapes and intricate geometries that would be difficult or impossible to achieve with conventional methods.
Design for Additive focuses on maximizing the potential offered by 3D printing, optimizing the internal structure of objects to enhance performance, reduce weight, and minimize material consumption.
Moreover, this methodology allows for greater customization of products, adapting them to the specific needs of the user/client.
A profound understanding of the characteristics of 3D printing and the ability to fully exploit its potential are required to create innovative and efficient solutions.
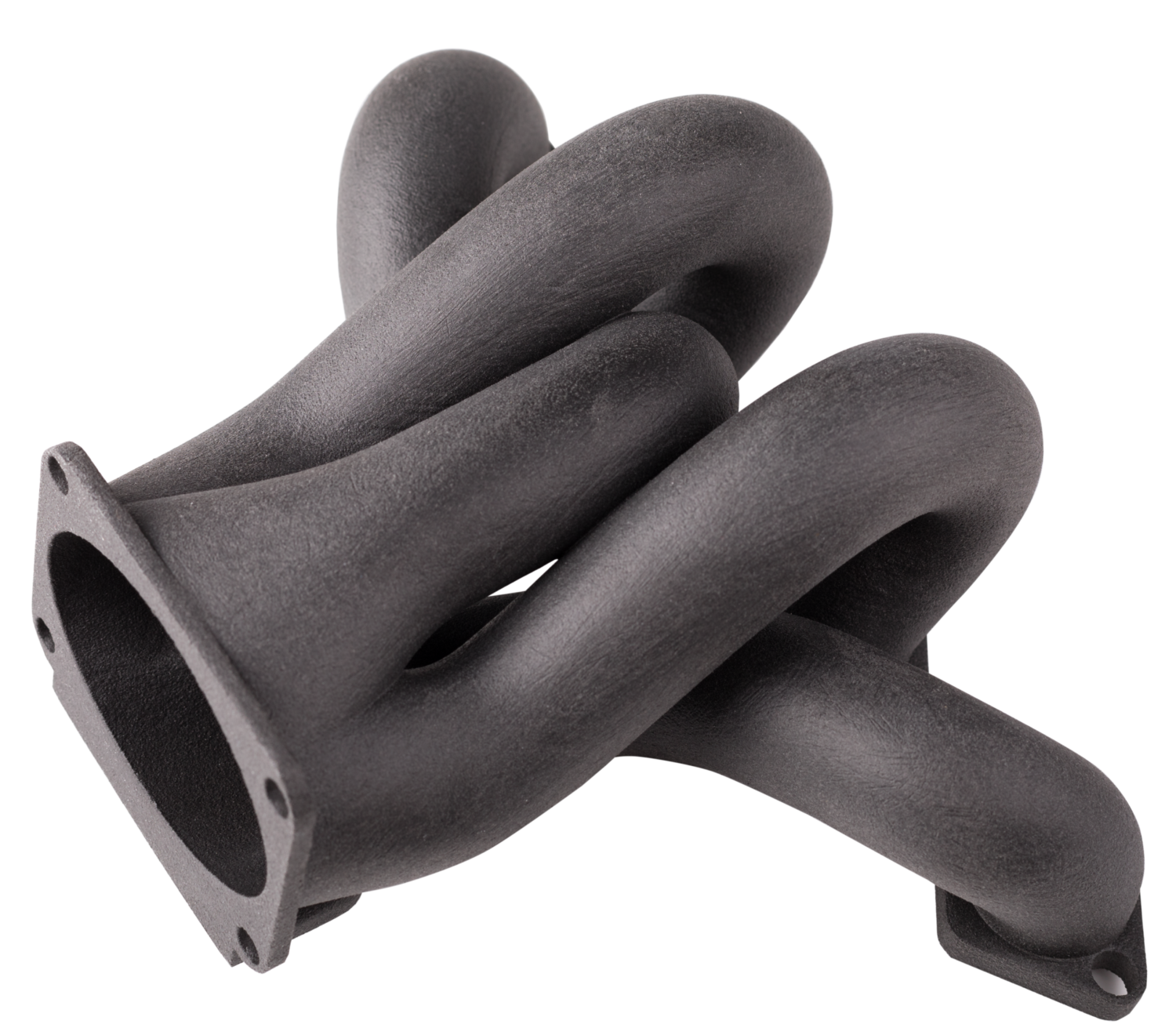
Nesting
Nesting, a specific technique for the orientation and organization of components in the setting phase of production, is crucial in every additive manufacturing project using 3D printers.
Unlike the production of individual parts, the production of medium to large batches with 3D printing requires a complex optimization process before printing.
Aspects such as orientation study and nesting have a significant impact on the times, quality, and costs of production processes, results achievable only through a deep understanding of processes and manufacturing technologies.
Thanks to the use of dedicated software, accumulated experience, and advanced management and control systems, Prosilas has established itself as one of the leading European players in the field of additive manufacturing for the industry
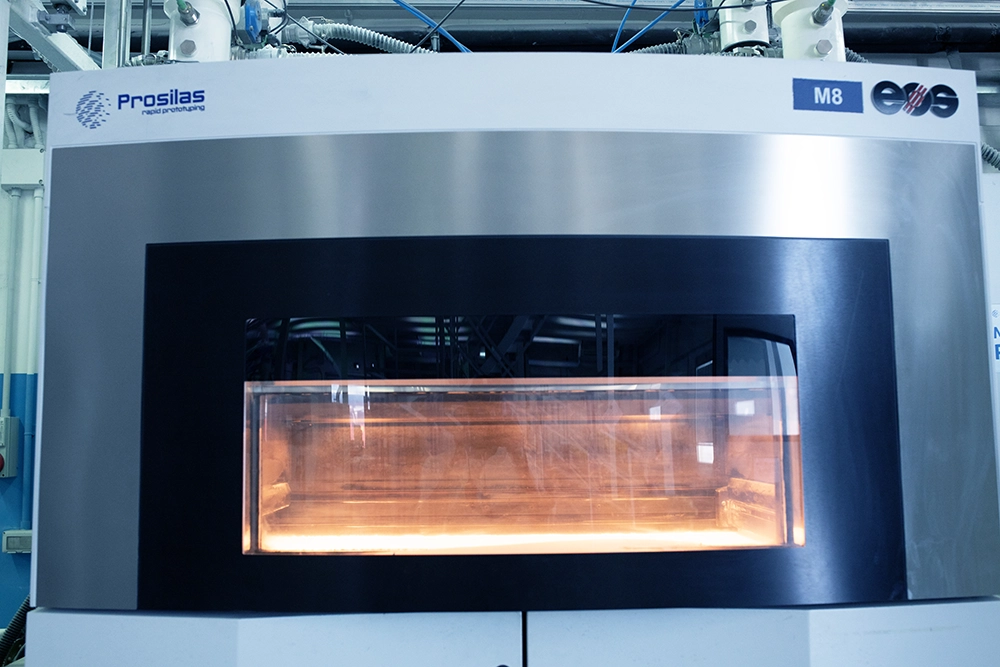
Technology
Prosilas’ machinery fleet, mainly composed of industrial production systems with SLS (Selective Laser Sintering) technology – 13 industrial Selective Laser Sintering printers, including 6 large-sized ones, has allowed the development of a complete and reliable industrial system capable of meeting customer needs from order reception to part realization and post-processing treatments.
The targeted choices made over the years have positioned Prosilas as one of the few entities capable of successfully operating in additive manufacturing for the industry.
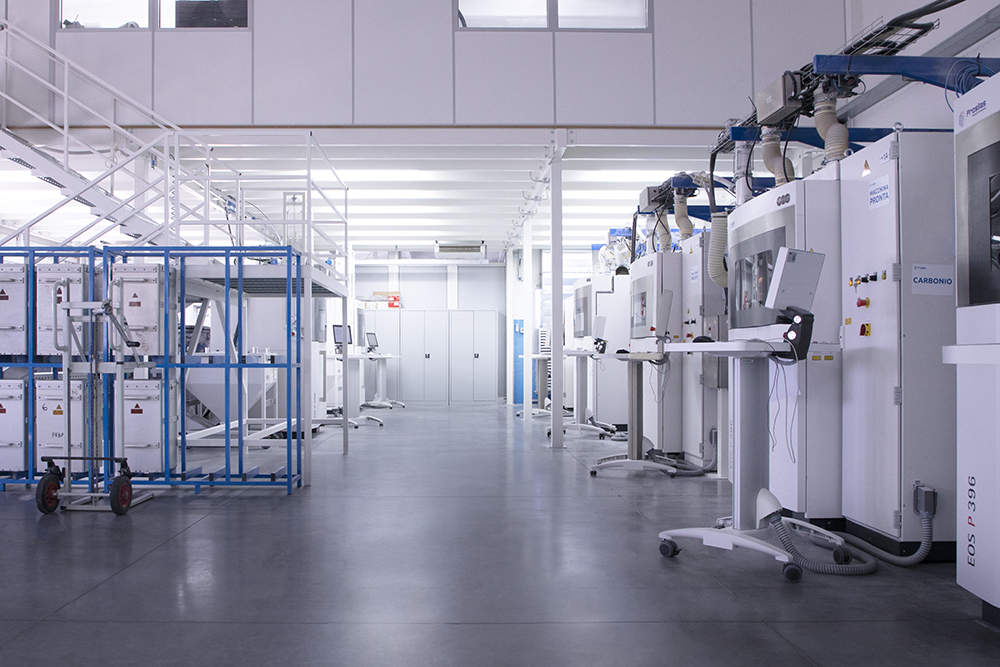
Post-Processing
Prosilas has invested significantly in enhancing the finishing department to deliver customized finished products to customers. Our primary commitment is to find flexible and high-quality post-production solutions that fully meet the aesthetic and functional needs of our clients.
We are continually refining our post-production processes to make them replicable and reliable. We have integrated automated finishes, such as vapor smoothing and coloring, along with manual processes to adapt to the unique specifications of each project.
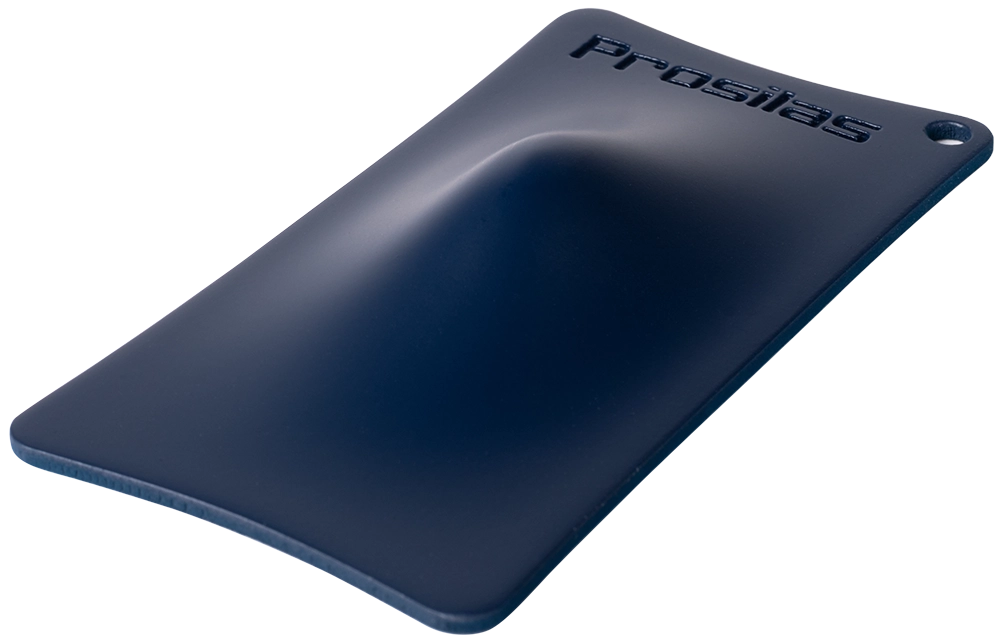
Quality and Certification
To ensure maximum precision and resolution, Prosilas implements stringent control procedures.
Productions undergo a series of detailed checks using specialized software and state-of-the-art 3D acquisition systems. These advanced tools enable our team to identify any non-conformities between CAD geometries and the physical parts produced through additive manufacturing.
Conformity is at the core of our operations, and our codified and certified procedures constitute a fundamental pillar of an integrated system.
This system is designed to ensure a high standard of quality for every stage of additive production, from the initial design to the final realization. Thanks to this commitment to excellence and our established expertise, Prosilas stands out as one of the few companies capable of providing reliable, repeatable, and certified additive manufacturing services
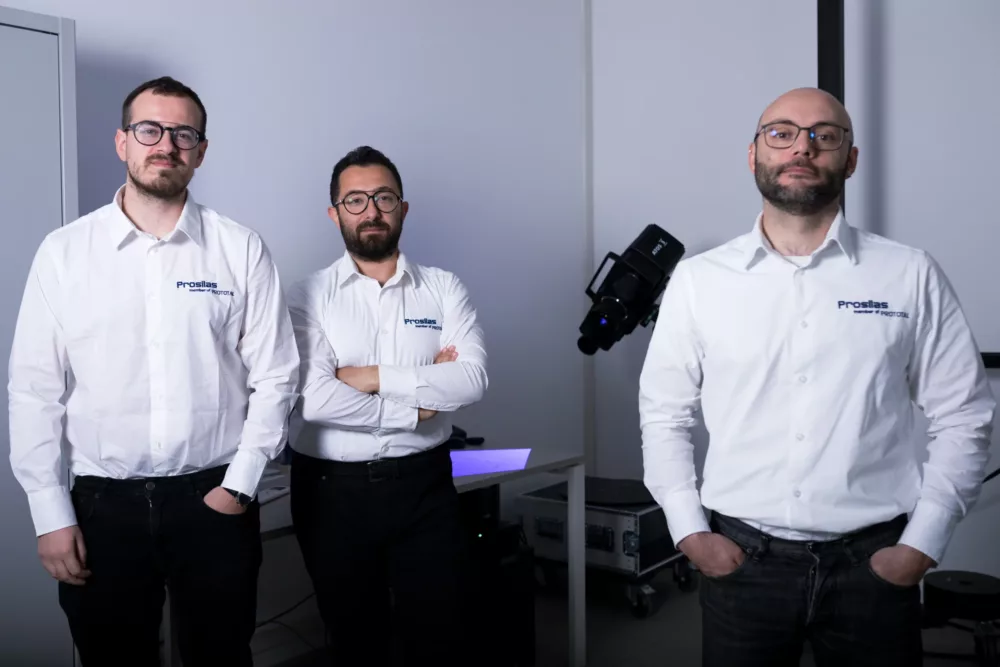